
There are five main reasons why solder might not stick to metal. Typically, the issues lie with lack of heat, dirty equipment, or product material, which could ultimately come down to poor technique. Fortunately, these issues can be fixed easily and quickly with a few simple steps.
Can You epoxy pot metal?
Epoxy paint is mostly used as floor ... The product provides low VOC capability, long pot life, good and wet adhesion to various metal substrates, good corrosion resistance which is measured ...
How do you glue metal to pot together?
What can I use instead of welding?
- Brazing. Brazing is similar to welding but instead of melting two pieces of metal to join them together, you melt a filler metal that you place between the two metals ...
- Soldering. …
- Riveting. …
- Metal stitching. …
- Looking for sheet metal machinery?
How to mend pot metal?
There are three ways to restore pitted pot metal, all with varying levels of success:
- Sand or grind out the pits. Sanding or grinding out the pits does not usually produce good results.
- Copper plate the piece until the pits disappear. Copper plating can produce good results, on the surface.
- Drill the pits out.
How do you melt solder without a solder iron?
To prevent burns or other safety hazards, consider the following safety precautions:
- Never touch the end of the heated screwdriver. ...
- Always conduct soldering work in a well-ventilated area. ...
- Perform the work on a surface that is nonflammable and cannot be easily ignited. ...
- To prevent burns from hot solder, wear a long sleeve shirt, long pants, and closed-toed shoes.

How do you solder pot metal?
1:584:39Pot Metal Repaired By a True Beginner Using a Torch and Super ...YouTubeStart of suggested clipEnd of suggested clipTaani dipped the rod into the flux to add more flux to bring the solder together and bond the smallMoreTaani dipped the rod into the flux to add more flux to bring the solder together and bond the small pieces. Together remember this is her second time ever using a torch.
What can I use to weld pot metal?
0:194:24Pot Metal and Zinc Die Cast Repairs Made Easy With Super Alloy 1 Multi ...YouTubeStart of suggested clipEnd of suggested clipAfter drilling or drem bling the pits just heat with a soft flame add your flux and solder sand. NoMoreAfter drilling or drem bling the pits just heat with a soft flame add your flux and solder sand. No more pits. When the flux turns brown you add your solder. And you're done.
What metals will solder not stick to?
Solder will not stick to just any metal. For example you will never get solder to stick to Aluminum. With compatible metals, however, you must use a suitable flux after preparing the metal surface to remove any oxidation. The flux will prevent new oxidation from forming when you heat the metal.
What metal will solder stick to?
Of metalsSolderabilityMetalGoodCopper Bronze Brass Lead Nickel silver Beryllium copperFairCarbon steel Low alloy steel Zinc NickelPoorAluminium Aluminium bronzeDifficultHigh alloy steel Stainless steels2 more rows
What is the best glue for pot metal?
Top 10 glue for pot metal: Comparison Table#ProductScore1Gorilla Super Glue Gel, 20 Gram, Clear, (Pack of 1)9.82J-B Weld 33120H SuperWeld Glue - Clear Super Glue - 20g9.8320g Metal Glue,Glue for Metal,for bonding Between Metal and Metal,Metal and Other Material.Instant...9.57 more rows•Jul 8, 2022
Can you repair broken pot metal?
Whether you're soldering pot metal for a repair job or restoring original pot metal classic car parts, you can now work on these sometimes rare or irreplaceable parts with ease. Even beginners can repair pot metal pitting and build up broken or missing pieces with a quality pot metal repair kit from Muggy Weld.
Can you solder any metal?
By the American Welding Society's definition, soldering takes place with fillers (also known as solders) that melt at below 840°F (450°C). Metals that can be soldered include gold, silver, copper, brass, and iron.
Can I solder metal to metal?
The brazing method means using a sort of filler metal to connect two metal parts together. The filler metal is heated at a temperature of over 800 degrees. While this method is like welding, it's less costly. Plus, it's more like using an adhesive rather than melting the metal pieces themselves.
What surface Can I solder on?
Soldering Surfaces: BoardsCeramic Soldering Boards. Although small, ceramic soldering boards can withstand intense torch work. ... Magnesia Block. Very popular among jewelers, a magnesia block can withstand up to 2,000º F (1,093º C). ... Charcoal Block.
How do you join two pieces of metal without welding?
The technique of brazing is similar to welding, but is less expensive. Also, brazing acts more like an adhesive as it bonds the two metals together with the filler metal....Here is a list of different ways to join metal without welding:Hardware assembly.Spot welding.Riveting.Brazing.Soldering.Glue.
What metal is easiest to solder?
The simple answer for the moment is that brass is guaranteed to work well, it's available and reasonably cheap. Other metals such as aluminium or regular steel can be soldered, but require special solder and flux and may need stronger equipment.
Will solder stick to anything?
Flux removes oxidation from metals, and it's crucial because solder won't stick to oxidized metals, and metals oxidize very quickly at soldering temperatures. 3. Not enough heat: A 15 Watt iron is fine for small chips, but any larger connectors or wire bigger than 16 gauge will cause problems.
Can you weld a cooking pot?
After some experimenting (and creating some hole in pots) I found a reasonable way to weld a solid handle to a thin walled pot. Please note that in order to get reasonable result TIG welding is required! Other welding methods like MIG, MAG or stick-welding (MMA) will not work.
How do you make homemade steel welding?
0:374:15Welding Basics for Beginners - YouTubeYouTubeStart of suggested clipEnd of suggested clipSo in welding you have three basic elements you have your heat source your filler metal. And thenMoreSo in welding you have three basic elements you have your heat source your filler metal. And then your shielding gas. Or your flux.
How do you weld aluminum pot metal?
0:367:45Aluminum Welding, Cast Iron Welding, Pot Metal ... - YouTubeYouTubeStart of suggested clipEnd of suggested clipIt's very simple to use just dip your rod into the flux and paint the flux on your parent metal andMoreIt's very simple to use just dip your rod into the flux and paint the flux on your parent metal and heat. When the flux turns brown you're ready to add the rod.
Can diecast metal be welded?
Die cast parts made from the alloy AlSi9MgMn (Silafont-36) are particularly well suited for welding, both the standard MIG and TIG methods (see Gas-shielded welding processes) and laser beam welding.
How to fix pot metal?
Pot metal repair via flux & solder is very similar to that of using a hot glue gun to stick items together. The only difference? With soldering, flux must be applied for cleaning while the two parts are heated to the solder’s melting point, roughly 350°. Pot metal repair by soldering is very easy however if you plan to re-plate, you will run into issues when presented to your chrome shop… For starters, the existing plating must be stripped due to the acid bath/electro “de-stripping” process which removes the chrome, nickel and copper, but everything else including solder! The rest is self explainatory.
What is pot metal welding?
Pot metal welding is by far the favorable way to go with pot metal repair. Unlike soldering which IS a form of Gluing, with welding pot metal, two or more pieces are fused together making them one piece creating a very strong and resilient to the plating process!
Who was the inventor of the pot metal welding problem?
James Ruther, the Innovator of solving this century old problem of Pot Metal Welding.
Does pot welding save time?
Pot metal welding also allows the repair to be done immediately without the need for a trip to the chrome shop for subsequent stripping. This alone will save you time and money.
Why does solder melt after plating?
For some reason after the part (s) have been plated many platters have experienced issues with the solder melting under the fresh plating from the heat caused by the polishing process. 90% of the time the new plating tends to develop bubbles around the repair. When this occurs, the shop must strip the new plating down to the base metal re-cleaning etc. for a second attempt. This has been confirmed by numerous chrome shops who’ve attempted to use soft solder for repairing pot metal.
What is epoxy for pot metal?
Although it works for some parts, not so much for others. You see, epoxy is a two part polymer adhesive that works very well on lighter porous materials such as wood and the like….
Can you soft solder a part?
The cost. Some soft solder kits are really over-priced for the average, person with no experience. Before you can perform a soft solder repair on a part you plan to have re-chromed, you must have the local chrome shop strip the existing chrome off the part. Otherwise if this is not done, the process of removing the old plating will cause the solder will come apart costing you more time or money.
Can pot metal be welded?
Long story short, Pot metal can be easily welded and is far more cost effective and is a permanent solution that doesn’t have any of the draw-backs previously mentioned with the other repairs.
Can you repair pot metal?
Pot metal repair is an art that many say that it can’t be done. However, there are just as many who claim to have the ability to repair pot metal. And the one’s who try their luck at welding pot metal, always winds up looking nothing like the original piece. Pot metal welding is no joke.
Can you gas weld pot metal?
This is a subject that not only a few believe, but can actually achieve. However the quality of their achievement is the question… 99.9% of individuals who can successfully get the job done are gas welding it with a jewelers torch. But there’s a couple of problems that keeps this method from being an ideal process for welding pot metal. Pot metal has two inherent problems. The first is it’s a very dirty metal. This is apparent when it starts to melt. The second, much like aluminum it oxidizes really quick about 10 times faster! This only adds to it’s volatility. If that’s not enough throw it’s heat sensitivity into the mix and you’ve got your hands full! Pot metal is a beast that most won’t even bother with.
What is solder made of?
Solder as an alloy is composed of tin and lead and which has a super-strong outer surface layer of oxidation.
What is the best flux for soldering copper?
Regular solder with rosin flux will stick to copper, tin, lead, brass and bronze. Regular solder with acid flux is needed for not so clean copper, brass or bronze. Acid flux is also needed for nickel, stainless steel, regular steel and zinc. Indium solder can be used with gold, glass and ceramics. Special tin-zinc alloys for solder can be used with a special flux to join aluminum and aluminum to copper or steel.
What is wetting solder?
Wetting is a property of liquids. Wetting is crucial to the formation of acceptable or superior solder joints. Wetting occurs as a phase change from solid to liquid (flux is crucial for this wetting as well), then heating it to the eutectic temperature.
Why do you need flux for soldering?
Flux helps solder wet properly, as the solder moves to the two surfaces being heating temporarily with the soldering iron tip.
What is lead free solder?
lead-free solder is mostly, tin, silver, copper :: Sn, Ag, Cu, or other metals. The temperature required to get a lead-free solder alloy into its molten, “eutectic”* state which allows for proper wetting is greater than that required for soldering with Sn60Pb40 or Sn63Pb37 Lead-tin solder; significantly hotter in centigrade or Fahrenheit (C or F).
Can you solder copper with rosin?
Pot metal doesn’t solder well if at all…All metals must be clean without oxidation…The copper and copper alloys, can be soldered using rosin as a flux.. Soldering paste can also be used on these metals…When soldering radiators, I believe they use an acid as flux.. This is of course very corrosive.. Must be well cleaned afterwards.. Galvanized steel that has never been oxidized can be soldered with an acid flux… Once it’s been oxidized it is about impossible to ev
Why do you need silver brazing?
Also Silver brazing might be useful if you want a stronger joint.
Why doesn't solder stick to metal?
There are five main reasons why solder might not stick to metal. Typically, the issues lie with lack of heat, dirty equipment, or product material, which could ultimately come down to poor technique. Fortunately, these issues can be fixed easily and quickly with a few simple steps.
How to solder metal?
To solder, you will need to place the soldering iron tip against the melt and then use this heat to melt the solder on top. If the surface temperature of the metal is not hot enough, the solder won’t melt properly or adhere to the metal. The iron itself might be hot enough to melt the solder, but if the metal isn’t hot enough, the solder will not stick.
What does it mean when a joint is under soldered?
You might find after soldering a joint that it is unstable and has a weak hold. This typically means that the joint was under-soldered and requires more solder for it to be fully secure. Again, this is an easy fix. Be sure to heat the joint and already present solder first before you add new solder on top.
What to do if solder isn't sticking?
If you notice your solder isn’t sticking, check your solder material and compare it to the wattage of your soldering iron. You might find that the iron isn’t the right match for the job in terms of wattage and needs to be switched out for another.
Why won't my solder melt?
This issue is usually caused by the soldering iron being set to an improper temperature, or the iron itself has a wattage that is too low for the solder size you are using.
How to prevent soldering iron from getting exposed to air?
Prevention. It is recommended that whenever you place the soldering iron down, coat the tip in a small amount of solder to eliminate its exposure to the air while it is on. It is also helpful to hold solder onto the tip as you heat the soldering iron to ensure it is coated. It reaches working temperatures and has minimal air exposure ...
How to clean a soldering iron tip?
To resolve this issue, you’ll want to clean the tip of the soldering iron. First, turn the iron on to a typical work range of about 300°C. Once it is sufficiently heated, you’ll want to apply a flux-colored solder onto the tip and wait for the heat to activate the flux. This will cause a chemical reaction that will remove any mild oxidation with the help of brass wool or specialized cleaners applied to the tip.
What metals are soldered?
For electronic purposes the metal surface should be copper, tin, zinc, silver, gold. If there is some other metal, then its surface must be treated so the solder adheres to it. Stainless steel and aluminum are very difficult to solder (there is a technique to solder aluminum — under mineral oil). For iron is doable but with some more precautions.
Why do I leave solder on the tip of a soldering iron?
Opinions vary on this, and I’m happy to be corrected with more up-to-date best practises, but when I’m done with soldering for the day, I leave a layer of solder on the tip, to protected it from oxidising and corrosion.
How to solder a joint?
Assemble the parts and apply flux to the surfaces to be soldered. Place the tip of the soldering iron on one side of the joint, then place the solder on the OPPOSITE side of the joint. When the surfaces are hot enough the solder will melt and flow into the joint. Remove the soldering iron.
How to heat transfer soldering iron?
Heat transfer is key to proper temperature. Start by bringing your soldering iron up to temperature and cleaning the tip. A wet paper towel will work for this. Tin the tip by applying a small amount of flux and then applying solder to the tip. You should have a cle
How to solder stranded wire to PCB?
If soldering stranded wire to a PCB, strip and tin the wires first, then solder to the board. Tin the wires by stripping them, apply flux, place the soldering iron on one side of the stripped portion and the solder on the OPPOSITE of the stripped portion. When the temperature is high enough, the solder will flow around and through the individual strands, effectively giving you a solid wire to work with. Again, should be smooth and shiny.
Why do you need a soldering iron?
If the parts to be soldered are big, then there is a need for a powerful soldering iron because the parts have to be at the melting point temperature (or a bit higher) of the solder. The parts have to be cleaned and deoxidized first and applied some flux to keep the surface clear for oxidation for a short time.
What does it mean when a solder joint is dull?
A dull and grainy solder joint indicates that the temperature was not high enough or the joint was moved before it cooled.
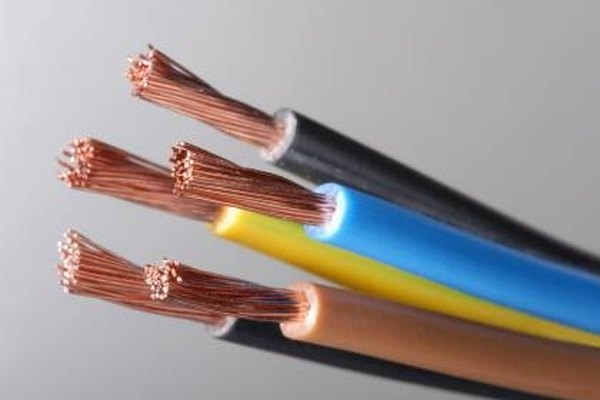