
There are several ways that a business can improve process flow:
- 1. Identify the constraints in a production process
- 2. Determine the root cause of the constraints
- 3. Find solutions to eliminate the root cause of the constraints
- 4. Test the solutions to determine if they work
How to improve workflow efficiency?
Improving a workflow isn’t easy. It means breaking down a process, working out solutions, and communicating the changes company-wide. But taking these measures can improve your bottom line by making operations more efficient. Follow these steps to improve workflow efficiency. #1. Map Out an Existing Workflow
How can I improve my material flow?
The first step in the process of improving your material flow is having a system for tracking all your materials. Similar to when you purchase a product off Amazon or from an E-Commerce store you receive notifications throughout the whole flow of the shipment. In most cases it works as below:
How to improve work processes?
In most businesses, the leadership does not have detailed knowledge of the work processes. To improve work processes it is essential to understand the existing workflow. The goal is to determine current operating procedures and identify problematic areas. Once process analysis is done, the next step is to identify potential areas for improvement.
How do you visualize process flows?
You can visualize process flows using timelines or workflow diagrams. Learn more about the origin of process flows, what process flow diagrams are, and how to use them to improve your team’s efficiency. What is process flow? A process flow is a way to visualize each subsequent step that your team goes through when working toward a goal.
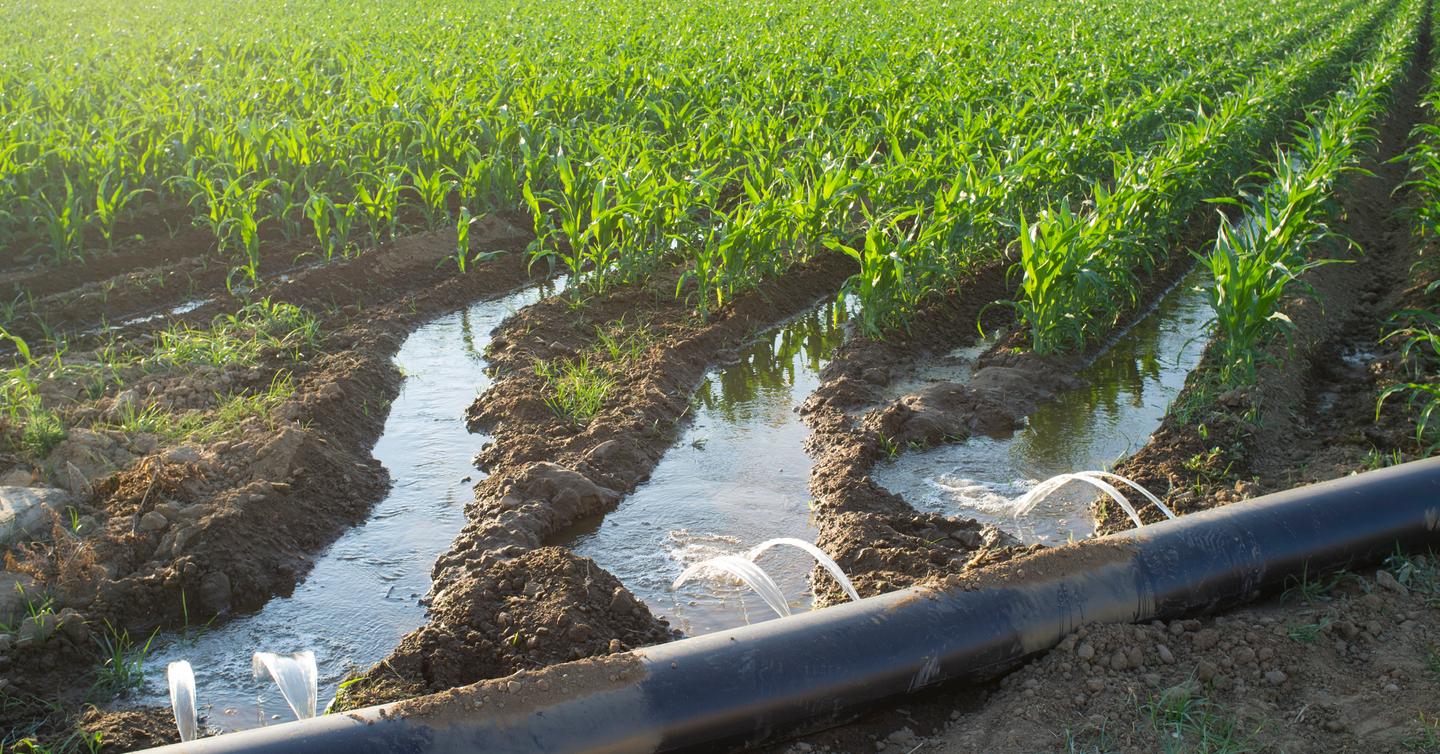
How can improve process improvement?
Improving processes involves the following seven steps:Choose a Process to Improve.Map Out the Current Process.Identify Bottlenecks & Areas for Improvement.Map Out the Potential New Process.Test the Process & Revise.Implement the New Process.Review the Process.
What are the five ways is can improve a process?
The “5 Ways”Reduce Non-Value-Added Steps.Improve the Measurement System.Reduce Common Cause Variation.Reduce Special Cause Variation.Move the Mean to Improve Process Capability.
How can process control be improved?
Top tips for improving process controlInvestigate the current system. ... Check instruments and regulators. ... Make sure controls are working well. ... Identify improvements in control. ... Plan for implementation. ... Take action and improve controls. ... Monitor performance.
What are examples of process improvements?
Process Improvement Examples – Types of Process ImprovementImproving product quality.Upgrade service quality.Improve delivery times.Reduce billing cycles.Make production more efficient.
What is a process improvement plan?
A process improvement plan is a document that outlines the steps required to optimize process performance. Having a detailed plan is important for a successful process improvement project as it ensures that all team members are aware of the goals of the project, their responsibilities, and project timelines.
How do you find areas of process improvement?
5 Methods for Identifying OpportunitiesMeet your business goals. Your business strategy and IP strategy must be closely aligned. ... Involve the right people and tools. ... Consider how often the process is used. ... Identify physical bottlenecks. ... Determine how long current practices have been in place.
How do you stabilize a process?
Stabilise your processesIntroduction to process improvement.Prepare your business collaboration tool.Make a process hierarchy and a process blueprint.Appoint, nominate and educate process owners.Present process mapping to all colleagues.Review and map processes.Stabilise your processes.Maintain process focus.
How do you reduce process variation?
Here are four tips for reducing variability in your operations: Standardize materials and sourcing. ... Standardize work to reduce in-process variation. ... Standardize gaging. ... Do not be seduced by “low cost” or “magic solutions.” Remember: consistency is the goal.
How do you improve business processes?
Business process improvement consists of at least six steps that organizations can use as a guide.Identify what process needs to change. ... Analyze the pain points. ... Conduct a root cause analysis. ... Design and evaluate. ... Implement the new process. ... Evaluate and quantify.
How many stages are there in process improvement?
How many stages are there in process improvement? Explanation: Process measurement, analysis and change are the three stages.
Which are the 4 important things you need to do to assess a process improvement opportunity?
4 Steps for an Effective Business Process Improvement CycleIdentify the need for change: The first step in the BPI process is to identify the need for change. ... Analyze current process: ... Obtain commitment and support: ... Create improvement strategy:
What are the actions needed to improve a process in Six Sigma?
6 Tips for Process Improvement: Applying Lean Six Sigma at WorkDefine: Figuring out your work problem.Measure: Mapping out your processes as they exist right now.Analyze: Identifying the causes of your work problem.Improve: Implementing your remedy and verifying that it's working.Control: Maintaining the solution.
How can leaders reinforce the importance of process improvement?
Leaders can reinforce the importance of process improvement by encouraging team members to block off time to devote to it. Similar to Google’s “20% time” policy, which is meant to encourage employees to spend time on innovation, dedicating time to improvement activity is an investment into the future of your company.
What is the first step in process improvement?
The first step in process improvement is to clearly define and visualize your current process. Consider: How do we do things now?
What Is Process Improvement?
Process improvement is the proactive task of identifying, analyzing and improving upon existing business processes within an organization, with the goal of improving process efficiency.
What is continuous improvement?
Continuous improvement is the ongoing practice of process improvement; it’s a process improvement that is woven into the fabric of daily work , as opposed to process improvement that happens once a quarter (or less frequently) with no follow-up. Continuous improvement can be viewed as a formal practice or an informal set of guidelines.
How does software improve communication?
Software improves communication and collaboration by connecting people more closely (even when they work in two entirely different locations) and putting all relevant communications in a single place. Ultimately, it leads to fewer emails, which means team members spend less time digging through their inboxes trying to find answers and more time getting work done.
What does it mean to succeed in today's business environment?
Succeeding in today’s business environment means constantly looking for ways to do things better.
Why do businesses need to have processes?
Every business relies on many processes, or a set of activities to accomplish an objective. These processes help maintain order and consistency and should also increase efficiency.
What is Business Process Efficiency?
All effective businesses are process-driven. With several processes and documentation in place, it is challenging to manage business processes effectively. A business process is put in place to streamline the work and ensure uniformity in results.
How Does Streamlining Processes Help Improve Business Efficiency?
Enhanced business process efficiency allows enterprises greater control over their operations and improves their productivity.
Process Efficiency Measuring Techniques
Business process measuring tools help in visualizing the process flow. The most commonly used measuring technique is the flow chart, in which every individual box represents a task.
Steps to Increase Efficiency
We understand the benefits of improving processes, but how to make a process more efficient?
Evaluating Existing Processes
Before you can enhance, you have to first evaluate. It is a critical step in the process that can have a great deal of effect on the outcome. Understand the ‘as-is,’ map out the entire process flow, identify the stakeholders, and put everything on a flow chart, a spreadsheet, or a Swim Lane diagram.
Identify Process Bottlenecks and Root Causes
Identify process bottlenecks and pain points that need to be addressed by the new restructured system. It is the step where you investigate all the problems within each stage. Take a look at each critical process and identify areas of inefficiencies and improvement.
Set Process Standards
In this step, you can set the ideal process and standards that you want to be implemented in your organization.
How to improve operational efficiency?
High-achieving organizations know this instinctively. Their efforts to improve operational efficiency result in: 1 More productive employees. Instead of spending time on needless administrative tasks or having unproductive conversations, they’re focusing on higher-value work that actually drives growth. 2 Financial savings. Instead of wasting money to carry out unnecessary tasks, they’re redirecting resources toward potential growth opportunities. 3 Better products or services. Instead of settling for processes that work some of the time, they’re supporting more consistent, high-quality output with better processes.
Why is it important to encourage employees to think about and suggest process improvements?
Leaders should encourage employees to think about and suggest process improvements regularly, as well as encourage collaboration across departments, so opportunities are more easily identified and discussed. Assigning owners to certain processes is also helpful, not just in the context of these process improvement steps but for the long term, so they can be on the lookout for potential opportunities continuously. When change becomes a mindset rather than a singular event, your organization will be well-prepared for growth—and anything the future throws at it.
Why is ClearPoint important?
ClearPoint offers an excellent way to track data for the purpose of making work process improvements. You can use it to collect and house data surrounding the process, before, during, and after the change.
Why do performance management systems go hand in hand?
Strategy execution and processes go hand in hand—that’s because outdated, inefficient, and unclear processes are obstacles to organizational growth . By some estimates, inefficient processes can reduce a company’s revenue by as much as one-third.
Why is process documentation important?
TIP: Process documentation is useful for more than just internal process improvement. It also promotes company knowledge sharing and helps when onboarding new team members (or getting help from a team member who may not know the process if you are bogged down with other tasks). 4.
How to ensure process is well understood?
To ensure the process is well-understood, document how it currently works. (If the process is already documented, test it to make sure those are still the steps you take.)
How to be a good candidate for a change effort?
Name a specific individual (or individuals) who will be responsible for driving the change effort. Someone who is involved on the ground level with the process is a good candidate for the job because they’re more likely to have useful insights.
What is process flow?
A process flow is a way to visualize each subsequent step that your team goes through when working toward a goal. By visualizing these steps in a diagram or flowchart, everyone can easily understand what order they have to complete tasks.
What is a process flow diagram (PFD)?
A process flow diagram is one way of visualizing your process flow. Depending on the type of process flow you’re depicting, you may call them top-down flowcharts, schematic flow diagrams, or process flowcharts.
Why is workflow important?
Workflows play a critical role for every organization. They ensure that processes like onboarding new employees and sending purchase orders follow the same steps every time. Making a single change to a workflow-removing an unnecessary task, automating a step, digitizing a form-can have a meaningful positive impact on how (and how quickly) ...
Why is mapping out a workflow important?
More importantly, a flowchart helps you identify potential bottlenecks.
How is Workflow Efficiency Measured?
Measuring a workflow is one of the most important steps to improving its efficiency. It allows you to define quantifiable metrics and establish a baseline.
Why is it important to address workflow inefficiencies?
It’s important to address any workflow inefficiencies before they start to have a negative impact on your bottom line.
What is the measure of resources-especially time-spent to complete a regularly-recurring process at work?
Workflow efficiency is the measure of resources-especially time-spent to complete a regularly-recurring process at work. More efficient workflows mean reduced operational costs and a more productive workforce. Let’s consider a workflow that’s common for many businesses — purchase orders.
How to reduce human error?
Mistakes inevitably happen from time to time. But you can reduce the risk of human error by automating workflows like expense approvals.
Why are workflows inefficient?
Manual tasks like data entry are another reason workflows are inefficient. They take away valuable time that could otherwise be spent on more productive works. Employees waste more than 10% of their time each week on repetitive tasks — more than 200 hours annually.
What is improving material flow?
Improving material flow is a way to remain competitive as a manufacturing facility. The three strategies in this article are just a few, yet vital actions to achieve a better material flow:
How can material flow be improved in the warehouse?
Because of this, there has been a concentrated focus on improving material flow and overall manufacturing protocols. These improvements can lead to better product quality, improved delivery times, a reduction in inventory, and a reduction in the number of defects.
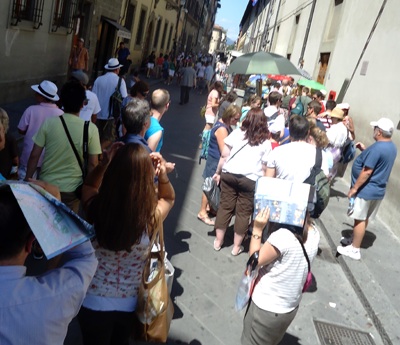