
What is the formula for cutting speed?
SFM to RPM Formula
- d – [Inch]
- n – [RPM] (Revolutions per minutes)
- Vc – [SFM] (Surface feet per minute)
How do you calculate CNC hour rate?
Those include:
- Programming: A programmer converts a CAD file into a CAM file for the CNC machine to process. ...
- Setup: A machinist will set up the machine/s for production. ...
- Quality control: Quality procedures differ from one shop to the next. ...
- Post-processing: Part-assembly, cleaning, support removal, and surface finishes typically require manual intervention.
How do you calculate the maximum speed?
Method 2 of 3: Solving Intermediate Problems
- Isolate the different variables to solve for distance and time. Once you know the basics of the speed equation, you can use it to find more than just speed.
- Convert your units as needed. Sometimes, you may calculate speed in one set of units but need it in another.
- Replace the "distance" variable with distance formulas as needed. ...
How do you calculate falling speed?
where:
- v₀ is the initial velocity (measured in m/s or ft/s);
- t stands for the fall time (measured in seconds); and
- g is the free fall acceleration (expressed in m/s² or ft/s²).

How do you calculate cutting speed and feed?
Using the imperial speeds formula, you would perform the calculation: RPM = (12 * surface speed) / (π * tool/workpiece diameter) RPM = (12 * 600) / (3.14159 * 0.5) RPM = 4584 rev/min....feed rate = RPM * chip load * number of teeth.feed rate = 4584 * 0.004 * 2.feed rate = 36.7 inches per minute (IPM)
How do you calculate the cutting speed of a lathe machine?
At constant cutting speed, a CNC lathe automatically applies the correct rpm based on the following formulas for inch and metric systems: rpm = 12 × sfm ÷ (π × cutting diameter in inches), rpm = 1,000 × m/min. ÷ (π × cutting diameter in millimeters).
What formula do you use for calculating the proper speed RPM of a cutter?
Calculating Spindle Speed (RPM) Using Imperial Cutting Speed:RPM=3.8 x SFMDiameterDec 24, 2010
How do you calculate cutting speed for milling?
Milling FormulasSpeed (RPM) = (SFM x 3.82) / D.Feed (IPM) = RPM x FPT x Z.SFM (Surface Feet per Minute) = (RPM x D) / 3.82.IPT (Inches per Tooth) = (IPM / RPM) / Z.MRR (Cubic Inches per Minute) = IPM * WOC * DOC.AFPT (@ less than 1/2 dia. WOC) = IPM x sqroot of (D / WOC)HP (Horsepower Consumption) = MRR x mf.
How do you calculate cutting length per minute?
Cutting time is the time required to machine the workpiece. As shown in the formula below, cutting time can be found by ℓm (workpiece length) ÷ ℓ(cutting length per minute). Example: When cutting length per min is 20mm and workpiece length is 100mm; 100÷20=5.
How do you calculate cutting speed for drilling?
S.F.M. = 0.2618 x Drill Diameter x R.P.M.
How RPM is calculated?
To calculate RPM for an AC induction motor, you multiply the frequency in Hertz (Hz) by 60 — for the number of seconds in a minute — by two for the negative and positive pulses in a cycle. You then divide by the number of poles the motor has: (Hz x 60 x 2) / number of poles = no-load RPM.
How is cutting load calculated?
The first step in establishing the cutting force is to determine the cut length area. The area to be cut is found by multiplying the length of cut by stock thickness. Generally for calculation purposes Shear strength is considered as 80% of tensile strength.
How do you calculate speed from diameter and RPM?
The RPM calculator helps you understand RPM (revolutions per minute) and compute the relationship between the speed of a vehicle and the RPM of its engine....To convert vehicle speed to a wheel's RPM:Multiply the wheel's RPM by the tire diameter.Multiply the product by 60 and π.Divide the resultant by 63360.
What is the unit of cutting speed?
RPM is the rotational speed of the cutter or workpiece. Speed is the recommended cutting speed of the material in meters/minute or feet/min. Diameter in millimeters or inches.
How do you calculate RPM on a machine?
How to Calculate Machine RPMConvert surface speed to feet per minute. To convert from meters per second, multiply by 196.85. ... Multiply your answer by 4. 393.7 * 4 = 1,574.8.Convert your cutter's diameter to feet. ... Divide your answer from Step 2 by you cutter diameter in feet.
How do you calculate RPM in metric?
4:2314:39How To Calculate Speeds and Feeds (Metric Version) - YouTubeYouTubeStart of suggested clipEnd of suggested clipAnd feeds here is our formula to calculate our RPM. Now I'm gonna start using some some symbols someMoreAnd feeds here is our formula to calculate our RPM. Now I'm gonna start using some some symbols some notation. Because those are the symbols being used by all of the tool suppliers now and you'll need
Cutting Speed Formula
When machining a part or a component, the cutting speed formula is one of the most critical criteria to consider. It is possible to boost the material removal rates by using the proper cutting speed and feed, hence improving the surface finish and the tool’s lifetime.
Selection Principle Of Cutting Parameters
In the process of CNC machining, the programmer must ensure the cutting parameters of each process and write them into the program in the form of instructions. Cutting parameters include cutting speed, back feed and feed rate. Different cutting parameters should be selected for different machining methods.
Credits
Sai Venkata Phanindra Chary Arendra has created this Calculator and 100+ more calculators!
Cutting Speed Solution
Diameter of rod - The diameter of rod is defined as the length of the longest chord passing across the rod under considerations. (Measured in Millimeter)
What is cutting speed
The cutting speed is defined as the speed at which the work moves concerning the tool (usually measured in feet per minute). It is obtained by the product of the job's perimeter and the job rotation speed.
How to Calculate Cutting Speed?
Cutting Speed calculator uses cutting_speed = pi*Diameter of rod*Number of jobs revolutions to calculate the Cutting Speed, The cutting speed is defined as the speed at which the work moves concerning the tool (usually measured in feet per minute).
What is the speed of a cutting tool?
Cutting speed is the speed at the outside edge of the tool as it is cutting. This is also known as surface speed. Surface speed, surface footage, and surface area are all directly related. If two tools of different sizes are turning at the same revolutions per minute (RPM), the larger tool has a greater surface speed. Surface speed is measured in surface feet per minute (SFPM). All cutting tools work on the surface footage principle. Cutting speeds depend primarily on the kind of material you are cutting and the kind of cutting tool you are using. The hardness of the work material has a great deal to do with the recommended cutting speed. The harder the work material, the slower the cutting speed. The softer the work material, the faster the recommended cutting speed (Figure 1).
What are the factors that determine the cutting speed of a material?
The three factors, cutting speed, feedrate and depth of cut, are known as cutting conditions. Cutting conditions are determined by the machinability rating of the material. Machinability is the comparing of materials on their ability to be machined. From machinability ratings we can derive recommended cutting speeds. Recommended cutting speeds are given in charts. These charts can be found in the Machinery’s Handbook, textbook, or a chart given to you by your tool salesperson. In Table 3 you will find a typical recommended cutting speed chart for drilling.
How to determine RPM for countersink?
The drill press RPM setting for countersinking and counterboring also depends on the cutting speed of the material and the size of the tool. The RPM setting will change with the size of the tool. As the cutting tool gets smaller, the RPM must increase to maintain the recommended surface footage. Although you will find specific cutting speeds for countersinking and counterboring, a simple rule of 1/3 the speed of a drill of the same size will work for most countersinking and counterboring operations. The RPM for a counterbore would be fairly simple to calculate using the 1/3 method, but calculating the RPM for a countersink brings about a different set of circumstances. The countersink is tapered (Figure 4).
How to determine RPM for a drill bit?
The RPM setting for drilling depends on the cutting speed of the material and the size of the drill bit. The RPM setting will change with the size of the bit. As the drill bit gets smaller, the RPM must increase to maintain the recommended surface footage. Take the case of the wheel. Think of the drill bit as a wheel and the cutting speed as a distance. A larger wheel (drill bit) will need to turn less revolutions to cover the same distance in the same amount of time than a smaller wheel (drill bit). Therefore, to maintain the recommended cutting speed, larger drills must be run at slower speeds than smaller drills.
What is the speed of countersinking?
One-third the speed for countersinking would be = 789/ 3 = 263 RPM.
How to set spindle speed?
To set the proper spindle speed, we need to calculate the proper revolution per minute or RPM setting. We stated earlier that cutting speed or surface speed would change with the size of the tool. So to keep the surface speed the same for each size tool, we must use a formula, which includes the size of the tool, to calculate the proper RPM to maintain the proper surface footage.
What does cutting speed need to decrease with?
Material to be tapped. Cutting speeds need to decrease with the hardness of the material.
What is the cutting speed of a tool?
Cutting speed may also be defined as the rate at the part surface, that is, how fast the material moves past the cutting edge of the tool. For different operations, the definition of surface may vary. In drilling and milling, the surface is the outside diameter of the tool.
What is the relative velocity of a cutting tool?
Cutting speed, also called surface speed, is the relative velocity between the cutting tool and the surface of the workpiece is being cut. The feed rate is the relative velocity at which the cutter is advanced along the workpiece, or defined as the distance of tool travels during one spindle revolution.
What happens if you cut too fast on a lathe?
Too high cutting speed will make the tool more easily damaged, while too low speed may be lost lots of time and reduce production efficiency. How to set the cutting speed on a lathe?
Does the depth of the cut affect the speed of a cut?
The depth of the cut and the feed rate will also affect the speed, but not to as great as the component hardness. The optimum cutting speed will be different if the types of material and machining conditions are changed.
Cutting Speed (vc)
This formula is used to calculate the cutting speed from the spindle speed and the diameter of the workpiece. Example: Diameter (Dm) = 60 mm Spindle speed (n) = 500 min -1 In this case, the cutting speed (vc) is approximately 94 m/min.
Feed (f)
This formula is used to calculate the feed rate per revolution from the spindle speed and the length cut per minute. Example: Machined length per minute (l) = 150 mm/min Spindle speed (n) = 600 min -1 In this case, the feed rate per revolution (f) is 0.25 mm/rev.
Machining Time (Tc)
This formula is used to calculate the machining time from the length of the workpiece and the spindle speed. Example: Feed (f) = 0.2 mm/rev Spindle speed (n) = 1100 min -1 Length of workpiece (lm) = 120 mm First, the machined length per minute is calculated, in this case from the rotational speed and the feed amount. Machined length per minute (l) = n × f = 0.2 × 1100 = 220 mm/min Substitute this into the formula: Tc = lm ÷ l = 120 ÷ 220 = 0.55 (min) × 60 = 33 (sec) The machining time (Tc) is approximately 33 seconds..
Theoretical Finished Surface Roughness (h)
This formula is used to calculate the theoretical finished surface roughness from the blade corner radius of the insert and the feed per revolution. Example: Feed per revolution (f) = 0.1 mm/rev Insert’s blade corner radius (Re) = 0.5 mm In this case, the theoretical finished surface roughness (h) is 2.5 µm.
Net Power (Pc)
This formula is used to calculate the net power from the depth of cut, the feed per revolution, the cutting speed, the specific cutting force, and the machine efficiency.
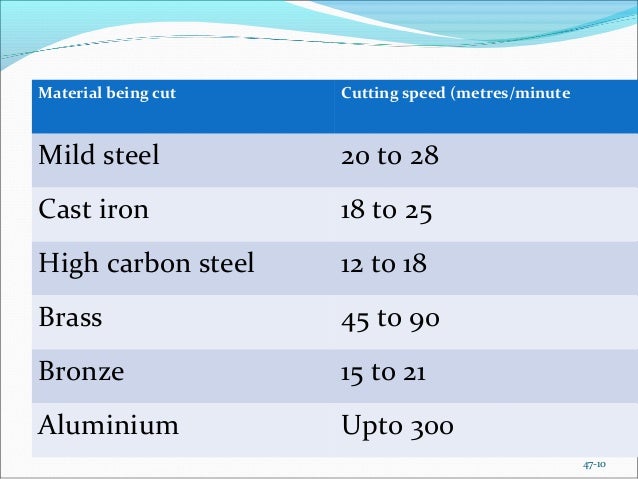
Charts
- The three factors, cutting speed, feedrate and depth of cut, are known as cutting conditions. Cutting conditions are determined by the machinability rating of the material. Machinability is the comparing of materials on their ability to be machined. From machinability ratings we can derive recommended cutting speeds. Recommended cutting speeds are ...
Format
- The RPM setting for drilling depends on the cutting speed of the material and the size of the drill bit. The RPM setting will change with the size of the bit. As the drill bit gets smaller, the RPM must increase to maintain the recommended surface footage. Take the case of the wheel. Think of the drill bit as a wheel and the cutting speed as a distance. A larger wheel (drill bit) will need to turn l…
Applications
- This simplified version of the RPM formula is the most common formula used in machine shops. This RPM formula can be used for other machining operations as well.
Example
- Let's put this formula to work in calculating the RPM for the drilling example below. Use the recommended cutting speed charts in Table 3. A 0.50 drill is being used to drill a piece of 1018 steel with a brinnel hardness of 200. Calculate the RPM setting to perform this drilling operation. Lets try an example. A high speed steel \"G\" drill is being used prior to reaming a 3/8 hole on a p…
Appearance
- The greatest indicator of proper and improper cutting speed is the color of the chip. When using a high-speed steel drill bit, the chips should never be turning brown or blue. Straw-colored chips indicate that you are on the maximum edge of the cutting speed for your cutting conditions. When using carbide, chip colors can range from amber to blue, but never black. A dark purple color wil…
Results
- cutting conditions. Carbide cutting tools are covered in much greater detail in another section of your learning materials.
Technology
- A 1.00-inch, high-speed steel (HSS) drill is being used on a piece of 1045 steel with a brinnel hardness of 300. Calculate the RPM setting to perform this cutting operation.
Equipment
- The drill press RPM setting for countersinking and counterboring also depends on the cutting speed of the material and the size of the tool. The RPM setting will change with the size of the tool. As the cutting tool gets smaller, the RPM must increase to maintain the recommended surface footage. Although you will find specific cutting speeds for countersinking and counterbo…
Use
- A center drill or combination drill and countersink (Figure 6) is used for spotting holes in workpieces or for making center holes for turning work. Center drills, as you can see from the illustration, are short and sturdy and will not bend or flex under pressure. When calculating the proper RPM for using a center drill, use the diameter of the pilot for your calculations. Center dril…