
Predetermined overhead rate = Estimated manufacturing overhead cost/Estimated total units in the allocation base Predetermined overhead rate = $16,000/4,000 hours = $4.00 per direct labor hour
- O/H is overhead.
- Total base units could be the number of units or labor hours etc.
How to calculate the overhead rate?
Typically, direct labor cost, direct labor hours, machine hours or prime cost is used as the allocation base, while the period usually selected is one year. Mathematically, it is represented as, Predetermined Overhead Rate = Estimated Manufacturing Overhead Cost / Estimated Units of the Allocation Base for the Period
What is predetermined overhead rate?
Predetermined Overhead rate Predetermined Overhead Rate Predetermined overhead rate is the distribution of expected manufacturing cost to the presumed units of machine-hours, direct labour hours, direct material, etc., for acquiring the per-unit expense before every accounting period.
How do you calculate direct labor cost in accounting?
For example, if the annual budget is based on a production quantity of 10,000 units and the direct labor required for each unit is three hours, the total direct labor is 10,000 x 3 or 30,000 hours. The total overhead expenditure is then divided by the total labor hours to arrive at the overhead rate.
How does Albert Shoes company calculate its predetermined overhead rate?
Example 2 Albert Shoes Company calculates its predetermined overhead rate on the basis of annual direct labor hours. At the beginning of year 2021, the company estimated that its total manufacturing overhead cost would be $268,000 and the total direct labor costwould be 40,000 hours.
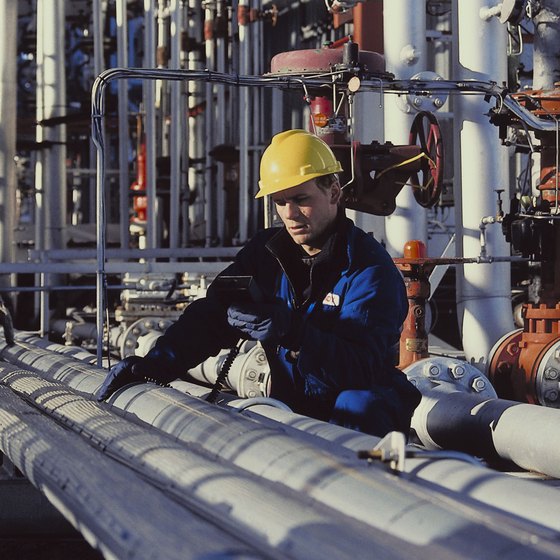
How is a predetermined overhead rate calculated?
A predetermined overhead rate is calculated at the start of the accounting period by dividing the estimated manufacturing overhead by the estimated activity base. The predetermined overhead rate is then applied to production to facilitate determining a standard cost for a product.
How do you calculate overhead rate per hour?
Most of the time, software companies calculate overhead costs by taking the total number of billable hours in all projects in a given period and divide their total overhead costs by that number. This is how they get the overhead rate per hour.
How do you calculate direct cost of labor with overhead rate?
The overhead rate or the overhead percentage is the amount your business spends on making a product or providing services to its customers. To calculate the overhead rate, divide the indirect costs by the direct costs and multiply by 100.
How do you calculate plantwide overhead rate based on direct labor hours?
To calculate the plantwide overhead rate, first divide total overhead by the number of direct labor hours used to find the overhead per labor hour. Next, multiply the overhead per labor hour by the number of labor hours used to produce each unit.
How do you calculate labor cost per hour?
How to calculate labor cost per hour. Calculate an employee's labor cost per hour by adding their gross wages to the total cost of related expenses (including annual payroll taxes and annual overhead), then dividing by the number of hours the employee works each year.
How do you calculate overhead rate per employee?
Companies do often determine the average overhead cost per employee by simply taking the total expense for an item, such as a particular piece of machinery, and then dividing the cost per the total number of employees at the firm.
How do you calculate overhead absorption rate per machine hour?
The total budgeted number of machine hours was 500 hours (2,000 * 0.25). We can now calculate the variable and fixed overhead absorption rates and show the standard cost card. Variable overhead absorption rate = $6,000/500 = $12 per machine hour. Fixed overhead absorption rate = $4,500/500 = $9 per machine hour.
What is a typical overhead rate?
Typical overhead ratios will vary significantly from industry to industry. For restaurants, for example, overhead should be about 35% of sales. In retail, typical overhead ratios are more like 20-25%, while professional services firms may have overhead costs as high as 50% of sales.
What are overhead hours?
The overhead rate allocates indirect costs to the direct costs tied to production by spreading or allocating the overhead costs based on the dollar amount for direct costs, total labor hours, or even machine hours.
Predetermined Overhead Rate Calculation (Step by Step)
The predetermined overhead rate equation can be calculated using the below steps:
Examples
Suppose that X limited produces a product X and uses labor hours to assign the manufacturing overhead cost. The estimated manufacturing overhead was $155,000, and the estimated labor hours involved were 1,200 hours. You are required to compute a predetermined overhead rate.
Relevance and Uses
Commonly, in the manufacturing industry, the manufacturing overhead cost for machine hours can be ascertained from the predetermined overhead rate.
Recommended Articles
This article has been a guide to the Predetermined Overhead Rate Formula. Here we discuss the calculation of predetermined overhead rate using its formula and downloadable excel template. You can learn more about accounting from the following articles –
How to calculate overhead rate?
To calculate the overhead rate, the cost accountant first adds together all the indirect costs estimated or budgeted for the period for the required production quantity, and calculates the total direct labor hours required to produce that quantity. For example, if the annual budget is based on a production quantity of 10,000 units and the direct labor required for each unit is three hours, the total direct labor is 10,000 x 3 or 30,000 hours. The total overhead expenditure is then divided by the total labor hours to arrive at the overhead rate. If, in the example, total overhead amounts to $120,000 a year, the overhead rate will be $120,000 divided by 30,000 hours, or $4 per hour. As each unit requires three hours of labor, the indirect cost of each unit is $4 x 3, or $12.
Why are direct costs called direct costs?
Direct Costs. Direct costs are so called because they can be directly attributed to manufacturing a single unit of the final product. For example, the wood used to manufacture a table is a direct cost, because the amount of wood required to make a single table is known, as are the number of hours taken to assemble it.
What are indirect costs?
Indirect Costs. To remain operational, a manufacturing unit also incurs indirect or overhead costs. Rent, utilities, maintenance, warehousing and supervision are examples of indirect costs that cannot be allocated to a single unit of production but must be included in total production costs.
