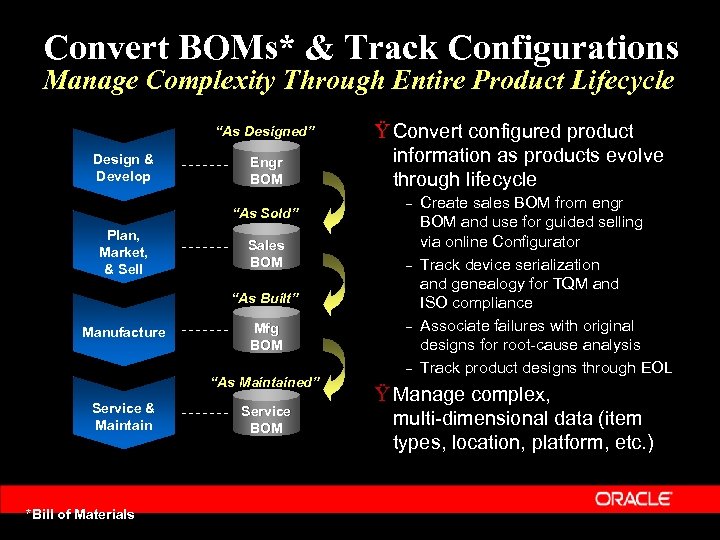
The formula for calculating ordering costs is very long as it contains many other cost factors. The order cost formula is as follows: Order cost = tax+ insurance premiums + Staff cost + inspection cost + payment fee + other incurred costs
Full Answer
How do I calculate my order expenses?
Then, you divide your order expenses by the total number of orders you received during the same timeframe. (Customer acquisition costs + packaging costs + fulfillment costs + shipping costs + COGS + storage costs in a time period) / # of orders in that same time period.
What is annual ordering cost?
Annual ordering cost is the total of these during the year. It is more accurate to calculate it annually as it is hard to separate the staff cost (salary) and allocate to each order made. We can get the staff cost per year and divided by the total number of orders to get the average cost per order. Examples of Ordering Costs
What is the ordering cost formula?
The ordering cost formula is useful for calculating the economic order quantity and gives businesses insight into how much of an item is necessary to meet customer demand and fulfill sales goals.
How much does it cost to place an order?
The cost of tracking the order and following up if the order is not delivered, etc.. For this reason, once all the total ordering cost is considered, that is the cost of the initial order. An order cost of between $60 to $75 seems reasonable for many items.

How do you find total order cost?
Ordering cost formula example Since the annual demand is 10,000 units, the business needs to place 10 orders throughout the year. With this information, business executives determine the total order cost for the year is $10,000, since 1,000 x $10 in the formula results in $10,000.
How do you calculate total ordering cost per year?
What is the order quantity such that the total cost is minimized?Total cost = holding cost + ordering cost = (order quantity/2) x holding cost per unit per year + (annual demand/order quantity) x cost per order.Optimal order quantity (Q*) is found when annual holding cost = ordering cost.More items...
What is the formula for ordering cost of inventory?
The total cost of inventory is the sum of the purchase, ordering and holding costs. As a formula: TC = PC + OC + HC, where TC is the Total Cost; PC is Purchase Cost; OC is Ordering Cost; and HC is Holding Cost.
How do you calculate EOQ and ordering cost?
To calculate the economic order quantity, you will need the following variables: demand rate, setup costs, and holding costs. The formula is: EOQ = square root of: [2(setup costs)(demand rate)] / holding costs.
What is the example of ordering cost?
Examples of order costs include the costs of preparing a requisition, a purchase order, and a receiving ticket, stocking the items when they arrive, processing the supplier's invoice, and remitting the payment to the supplier.
What is order cost?
Ordering Cost means costs associated with requisitioning, ordering, receiving, inspecting, and paying for needed goods or services. Acquisition transaction cost. It is used in calculating economic order quantities.
What is the definition of ordering cost quizlet?
Ordering cost. salaries and expenses of processing an order, regardless of the order quantity.
How do you calculate EOQ without holding cost?
2:049:24Economic Order Quantity (EOQ) without Cost - YouTubeYouTubeStart of suggested clipEnd of suggested clipSo we change our formula to q equals x times the square root of d that's formula. One we do anotherMoreSo we change our formula to q equals x times the square root of d that's formula. One we do another mathematical trick to figure this out we know that n is d divided by q.
How do you calculate EOQ in Excel?
Economic Order Quantity is Calculated as:Economic Order Quantity = √(2SD/H)EOQ = √2(10 million) (100 million)/10 million.EOQ = √200.EOQ = 14.142.
How do you calculate economic order quantity with examples?
Example of Economic Order Quantity The shop sells 1,000 shirts each year. It costs the company $5 per year to hold a single shirt in inventory, and the fixed cost to place an order is $2. The EOQ formula is the square root of (2 x 1,000 shirts x $2 order cost) / ($5 holding cost), or 28.3 with rounding.
How is EOQ holding cost calculated?
How to calculate holding costDetermine the value for each of your inventory cost components. ... Find your inventory holding sum. ... Determine your inventory's total value. ... Divide the inventory holding sum by the total value of inventory.
What is economic order quantity in cost accounting?
Economic order quantity (EOQ) is a calculation companies perform that represents their ideal order size, allowing them to meet demand without overspending. Inventory managers calculate EOQ to minimize holding costs and excess inventory.
Which is the correct formula for the total cost in the EPQ model?
The formula for EPQ or Q is Sqrt (2Ds/[h(1-d/p)]). In other words, calculate the EPQ by multiplying twice the annual demand by the setup cost per unit; dividing the product by the holding cost per unit multiplied by the inverse of daily demand divided by daily production; and taking the square root of the result.
How do you calculate annual demand?
The EOQ Method If you have a steady demand of, say, 2,400 units per year, you multiply that by two, then by the cost of ordering one unit. Then divide by the cost of holding one unit in inventory for a year. Take the square root of the total.
What is the order cost?
Ordering cost, or inventory ordering cost, is the cost company spends to acquire the inventory from supplier to warehouse. This cost does not include inventory purchase price, but refer to the cost spend to transport the material from supplier’s ware house to our warehouse.
What is staff cost?
Staff cost: refer to the purchasing department who work closely in finding suppliers, select suppliers, prepare purchase order and so on. Tax: include custom duty, import tax and other tax. Insurance for the material from oversea. Payment fee: the bank’s charge.
What is payment fee?
Payment fee: the bank’s charge and other fees.
Is factory rental part of ordering cost?
Factory rental is not part of ordering cost, it is the holding cost.
How to calculate lot size?
Standard methods of calculating the lot size are the following: 1 Lot for Lot: This is confusingly named because lot for lot is simply a lot size based upon the net requirements in a particular period. Therefore it is nearly no lot size. Using lot for lot sizing would be considered Lean as the company is only producing or procuring what it knows that it needs. 2 Economic Order Quantity: This bases the lot size on a financial calculation. 3 Periodic Order Quantity: This is simply the economic order quantity but stated in terms of a reorder frequency.
What is economic order quantity?
Economic order quantity (EOQ) is one of the oldest formulas in inventory management, and it preceded the development of ERP by many decades . Ford W. Harris first developed EOQ in 1913. Since its introduction, EOQ has been one of the most important and most durable formulas in inventory management. EOQ is a type of order batching.
What is the Reorder Point?
The reorder point tells the system when to reorder, while the economic order quantity tells the system how much to order ; as such, they are necessarily highly integrated values.
Why don't companies calculate EOQ?
For whatever reason, most companies don’t get around to calculating EOQ or, if they do calculate it, they do so very infrequently. The primary reason for this is a lack of resources to recalculate EOQ and a lack of tools to perform the calculation — even though the calculation is straightforward to calculate and there is an automated way to update lot sizes in inventory systems.
What is EOQ in purchasing?
A single product or no product interactions. Because of these assumptions, EOQ makes much more sense applied to purchasing environments than to the production environment for which Harris intended it. In a purchasing environment, setups (i.e. purchase orders) may adequately be characterized with constant costs.
Why do supply planning parameters have the highest value when the forecast is most accurate?
This is because they must adjust for a higher variability on the demand side.
Is lot for lot sizing lean?
Therefore it is nearly no lot size. Using lot for lot sizing would be considered Lean as the company is only producing or procuring what it knows that it needs .
How to find total variable cost?
To find the total variable cost you first need to identify all the variable costs associated with the specific production of the unit. This includes the cost of labor, material, and overhead costs. Add all of these costs together to get the total variable costs of a single unit. It is not difficult to get total variable costs.
What is total cost?
The total cost is the combined fixed and variable costs for a batch of goods or services. The total cost is the cost of producing the specific level of output factoring in all the costs of production. It helps to determine business profitability. It helps you determine if you need to adjust pricing, reduce cost, and helps you identify diversifying opportunities. In this section, we discuss how to calculate total costs.
How to calculate the average variable cost?
Average variable cost will help you determine if you should temporarily stop your production. If the price received is greater than the average variable cost and fixed costs, production should continue. But you should shut down production when the price is lower than the sum of average variable costs and fixed costs. In this section, we discuss how to calculate average variable costs.
How to calculate the total fixed cost?
It is also called overhead costs or indirect costs. Calculating your fixed costs is simple. All you need to add up all the fixed costs. In this section, we elaborate on how to calculate total fixed costs.
How to find the cost function?
Saving money is a vital part of the business. A small saving can add up considerably in a period. To begin a realistic saving plan, business leaders need to study the company’s spending patterns. Businesses costs can be broadly classified into fixed and variable costs. The cost function formula calculator helps businesses track expenses.
What is average fixed cost?
Average fixed cost is the fixed cost of production divided by the number of goods produced. Fixed costs are the costs incurred regardless of the volume of goods produced.
What happens if you sell goods at a lower price than average variable cost?
If goods are sold at price lower than average variable costs, then you should shut down production, since the business is unable to meet the recovery costs. The average variable cost formula
What is cost per order?
Cost per order (CPO) is the total calculated cost that is incurred by a customer making a purchase and determines profit made from a single order.
How to reduce cost per order?
Reducing your cost per order can not only can help your ecommerce business be profitable, but it also results in better supply chain efficiency with opportunities to improve your warehouses, fulfillment operations, and overall ecommerce supply chain . 1. Map out your workflow.
Why is ecommerce storage so expensive?
Storage or warehousing costs. Storing ecommerce inventory can be expensive, especially if your inventory is not being sold very quickly. For every item you have, you need storage space. If you have too many items that are unsold, you’ll have to expand your storage space to account for these costs.
How to reduce costs in retail?
1. Map out your workflow. There are many unseen improvement opportunities in your retail order fulfillment processes. Work with your pickers and warehouse staff to see how you can reduce costs by improving routing, picking, inventory storage, and the other day-to-day processes throughout the order fulfillment process .
How much does packaging cost?
In general, packaging shouldn’t cost any more than 5% of your average order value.
Is custom packaging cost effective?
But if it’s not cost-effective, it can become an unnecessary expense if you’re selling a low- cost item.
Does shipping cost add up?
Shipping costs. Shipping costs can add up depending on where orders are being fulfilled. For instance, if you have one storage or warehouse location in Florida, the cost of shipping the order to the other side of the country in Oregon is going to be much more expensive than shipping to a neighboring state, Georgia.
Why is total cost of production important?
The concept of the total cost of production is very important to understand from the perspective of production managers because it helps in the assessment of overall profit margin at a different level of production. Principally, the total fixed cost is not expected to change over a shorter period of period and so the total cost of production is primarily driven by the change in average variable cost per unit. Nevertheless, the total fixed cost is also equally important because it is the sum of total fixed cost and total variable cost which when deducted from the revenue will give the company profit. As such, the formula for total cost is very useful for all business.
Why is total fixed cost important?
Nevertheless, the total fixed cost is also equally important because it is the sum of total fixed cost and total variable cost which when deducted from the revenue will give the company profit. As such, the formula for total cost is very useful for all business.
Is total cost of production proportional to level of production?
In this example, it can be seen that the total cost of production is directly proportional to the level of production.
Can total variable cost be expanded into a product of a number of units?
However, the total variable cost can be further expanded into a product of a number of units produced an average variable cost per unit as shown below.
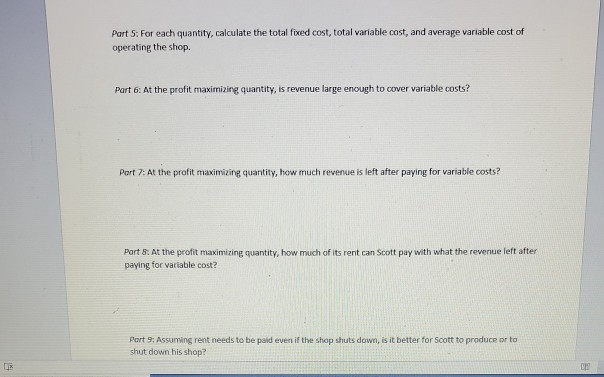