
Pitting corrosion can be prevented through:
- Proper selection of materials with known resistance to the service environment.
- Control pH, chloride concentration and temperature.
- Cathodic protection and/or Anodic Protection.
- Use higher alloys (ASTM G48) for increased resistance to pitting corrosion.
- Proper selection of materials with known resistance to the service environment.
- Control pH, chloride concentration and temperature.
- Cathodic protection and/or Anodic Protection.
- Use higher alloys (ASTM G48) for increased resistance to pitting corrosion.
How do you prevent corrosion on stainless steel?
In addition, providing a corrosion-resistant coating or cathodic protection may be necessary in some cases. In the case of austenitic stainless steel, the addition of at least 2% molybdenum can minimize the pitting corrosion rate in a NaCl solution.
How do you prevent pitting in stainless steel?
Normally stainless steels with a high percentage of Molybdenum such as SS 317 is more resistant to pitting. Additionally resistant coatings or polishes can also be applied on the surface of the metal to prevent pitting and cathodic protection can also be used.
How do you prevent corrosion on aluminum?
aluminum and other alloy metals where corrosive chemicals have attacked the surface. Pitting corrosion can be prevented by choosing metals with appropriate pitting corrosion resistance and by protecting the surfaces with cathodic protection and protective coatings.
How do you stop corrosion from pitting?
The addition of a passivation agent such as nitrate to the corrosive medium, wherever feasible, can also reduce the risk of pitting. Increasing the pH value of the corrosive medium can also reduce pitting damage. In the case of aluminum, pitting corrosion is often seen as an aesthetic problem.

How do you protect stainless steel from pitting?
The best way to prevent pitting is to wait to add the salt to your pasta water until it has already come to a boil. That way, the salt dissolves in the hot water and does not sink down to the Pan's surface, thus preventing the reaction from occurring.
How can pitting corrosion be prevented?
Pitting corrosion can be controlled by:Use of a coating that will prevent pitting on metal surfaces.Using more corrosion resistant materials.Ensuring that the fluids in contact with the material is washed away regularly.Use of cathodic protection.Avoiding stagnant zones.Inhibitor use / fluid chemistry control.More items...•
Why are stainless steel prone to pitting?
Localized corrosion such as pitting and crevice corrosion of stainless steels generally occurs in the presence of halide ions, typically chloride (e.g. coastal and deicing chloride salts – sodium, calcium or magnesium chlorides; hydrochloric acid; bleach – sodium or calcium hypochlorite; and other chloride compounds).
Is stainless steel prone to pitting corrosion?
Pitting corrosion is a form of localized corrosion, which produces attacks in the form of spots or pits. Pitting corrosion may occur in stainless steels in neutral or acid solutions containing halides*, primarily chlorides (Cl-), such as seawater.
Can pitting corrosion be stopped?
Pitting corrosion can be prevented through: Proper selection of materials with known resistance to the service environment. Control pH, chloride concentration and temperature. Cathodic protection and/or Anodic Protection.
What are the major factors that influence the pitting corrosion?
Environmental factors, pitting potential, metallic composition, temperature and the surface conditions, among others are the diverse parameters influencing pitting corrosion. Among these factors, environmental parameter is the most critical factor.
Can pitted stainless steel Be Fixed?
The chromium combines with oxygen to form a layer of chromium oxide, a type of rust that prevents more damaging iron oxide rust from forming. Chlorine can damage that layer and cause a condition called pitting, and pitted stainless steel can't be repaired.
What is the most corrosion resistant stainless steel?
grade 304Austenitic stainless steels generally provide the most corrosion resistance because of their high amounts of chromium. This makes grade 304 an excellent choice when corrosion resistance is important.
What makes stainless steel not rust?
Stainless steel is a steel alloy that contains a minimum chromium content of 10.5%. The chromium reacts with the oxygen in the air and forms a protective layer that makes stainless steel highly resistant to corrosion and rust.
How do you fix pitting in metal?
How to Fix Pitting in Metal Before PaintingWrap a sheet of 80-grit sandpaper around a sanding block and sand the pitted area aggressively. ... Wipe the sanding dust off the metal with a rag.Scrub the metal with a wire brush to remove rust particles from inside the pits and wipe off the particles with a dry rag.More items...
How do you make steel corrosion resistant?
Galvanize: Galvanizing coats iron or steel in zinc to protect from rust. Zinc corrodes at a much slower rate than iron or steel, so it's highly effective for slowing rust. Blueing: This process creates a layer of magnetite over the metal to prevent rust.
What is stainless steel passivation?
What is passivation of stainless steel? Passivation is a widely-used metal finishing process to prevent corrosion. In stainless steel, the passivation process uses nitric acid or citric acid to remove free iron from the surface.
How do you prevent pitting corrosion in aluminum?
Painting, anodizing or any surface treatment that forms a coating on the aluminium surface will protect the surface from pitting attack. In applications when you want to preserve the aluminium look and still have a surface resistant to pitting, a clear coat or thin anodic coating would be suitable surface treatments.
How do you fix pitting in metal?
How to Fix Pitting in Metal Before PaintingWrap a sheet of 80-grit sandpaper around a sanding block and sand the pitted area aggressively. ... Wipe the sanding dust off the metal with a rag.Scrub the metal with a wire brush to remove rust particles from inside the pits and wipe off the particles with a dry rag.More items...
What is pitting corrosion?
Pitting corrosion is a localized form of corrosion by which cavities or "holes" are produced in the material. Pitting is considered to be more dangerous than uniform corrosion damage because it is more difficult to detect, predict and design against. Corrosion products often cover the pits.
How do you treat pitted rust?
0:273:45Car Rust Repair -How to Fix Rust Pits in a Fender with Glazing ... - YouTubeYouTubeStart of suggested clipEnd of suggested clipThe fast stitch will dissolve the rust leaving with nice clean metal then spray some rustMoreThe fast stitch will dissolve the rust leaving with nice clean metal then spray some rust encapsulator on the area and sand it off the rust encapsulator will remain in the pits.
What is the most troublesome form of corrosion that can affect and damage Stainless steel parts?
Pitting is one of the most troublesome form of corrosion that can affect and damage Stainless steel parts. Material Grades. Helping Manufacturers Selecting Right Material. About Us.
How to prevent pitting?
To prevent pitting the first factor that needs to be considered is the use of the proper metal grade according to the service environment conditions. The environment should be controlled in order to ensure a safe pH and reduced chloride levels. The surface of the metal part should be kept clean and fluid should not be allowed to accumulate on it. If the environment cannot be controlled then a resistant ally should be used.
Why is pitting dangerous?
Although pitting is localized, it is a very destructive process. Pitting is specially dangerous because it can be difficult to detect because of the small size of the cavities and because the holes may be covered by the products of corrosion. Even though the holes may appear to be small on surface, there may be a significant amount of undercut below the surface making corrosion seem lower than it actually is.
What is pitting in metal?
What is Pitting? Corrosion is the primary phenomena which can cause damage to metallic parts. Of the many forms of corrosion, pitting is one of the most troublesome processes. Pitting corrosion is very localized corrosion which normally occurs in metals which are covered by a passive oxide film such as Aluminium and Stainless Steel.
What happens when a cavity is pitted?
Role of Pitting Cavities: As the cavities spread, the amount of metal in the cross section of the region decreases leading to an increase in stress which can cause sudden failure at that point. This is the biggest danger of Pitting that it can cause failure with only a small percent of material loss from the entire structure. Additionally it can be difficult to predict pitting with laboratory tests or to measure quantitatively because of the large degree of variance in the size and depth of the cavities.
Why is it so hard to predict pitting?
Additionally it can be difficult to predict pitting with laboratory tests or to measure quantitatively because of the large degree of variance in the size and depth of the cavities. Pitting Prevention and Control: To avoid any adverse effects, prevention is the first of defense.
Is stainless steel pitting resistant?
If the environment cannot be controlled then a resistant ally should be used. Normally stainless steels with a high percentage of Molybdenum such as SS 317 is more resistant to pitting.
How to prevent pitting corrosion?
Since corrosion is caused by reactions between a metal and the surrounding environment, another way to prevent pitting corrosion is to control the service environment, to the extent possible. Of course, for parts that are to be used outside, it’s nearly impossible to control all environmental factors. For parts used inside, however, controlling the environment can be as easy as keeping a part clean, limiting water exposure, or regulating temperature as to keep the environment below the critical pitting temperature (CPT) of the material. Additionally, humidity can be regulated to limit or prevent chemical reactions from occurring. In some cases, manufacturers must get more creative and regulate factors such as pH levels or chloride concentrations. Regulating environmental factors can go a long way towards preventing pitting on the parts.
What is Pitting Corrosion and How is it Caused?
Corrosion is the deterioration of a metal due to electrochemical oxidation-reduction reactions that occur between the atoms at the surface of a metallic part and the atoms in the service environment. Pitting is a localized type of corrosion characterized by tiny holes or “pits” on the surface of a part. Metals that naturally form thin, protective oxide coatings - like stainless steel, aluminum alloys, and others - are the ones most susceptible to pitting corrosion.
What is galvanizing metal?
Galvanizing is a type of passivation and metal plating process that provides cathodic protection. In this process, a metallic substrate, like cast iron or hot-rolled steel, is coated with molten zinc. It inhibits corrosion because zinc is more active (anodic) than ferrous substrates. Therefore, the coated layer of zinc acts as a sacrificial anode - meaning the electrochemical reactions associated with corrosion occur within the zinc, not within the ferrous substrate. As long as zinc is present on the surface near the localized corrosion, the substrate will be protected. Another passivation process similar to galvanizing is anodizing. Anodizing is more suited for aluminum and other non-ferrous metals.
How to tell if a pit is corroded?
Visual examination of a part is the primary way of identifying the presence of pitting corrosion. As corrosion proceeds, byproducts like rust or carbonate begin to form at the edges of pits, making them easily identifiable. The problem is that once these pits become noticeable, damage underneath the surface has more than likely occurred already. While the density of pits present on a part is concerning, the real danger lies in the depth and expansiveness of the pits - the deeper and more expansive the pit, the more material that is exposed to the atmosphere. Other methods can be used to test for the presence of pits and can help describe pits further (i.e. trough or sideway pits, shallow or deep, wide or narrow, etc.), including:
What is protective coating?
Protective coatings, like painting or powder coating, are an excellent way to inhibit corrosion since these coatings act as a physical barrier between the metallic substrate and the surrounding environment. For manufacturers, it’s important to properly prepare metallic surfaces so that paint and powder coatings can adhere to the part.
Can powder coatings cause corrosion?
Although paint and powder coating can both offer corrosion protection, their use is not a perfect solution. These coatings will eventually wear out - leading to corrosion to occur. Therefore, it’s important for manufacturers to consider the environment where the part will be used in.
Is pitting corrosion a problem?
On the surface, pitting corrosion may seem insignificant and may be deemed only an aesthetic issue. Underneath the surface, however, pitting on the part can quickly deteriorate the metal material. The strength of structural or load-bearing components - like in a bridge or building - can be compromised. Therefore, pitting presents an enormous risk to human life. Thankfully, there are steps manufacturers can take to prevent pitting corrosion from occurring - from selecting an appropriate material to applying protective coatings to parts.
What is the passive layer of corrosion?
Pitting corrosion: the passive layer is damaged locally due to highly activating substances (e.g. chlorides) Crevice corrosion: is triggered in areas that are poorly “oxygenated”, with the presence of aggressive substances.
What is intergranular corrosion?
Intergranular corrosion: thermal alteration (e.g during the welding phase) causes an impoverishment of chromium at the edges of the grains which, in the presence of a corrosive substance, can start the attack. Galvanic corrosion: by pairing stainless steel and other less noble materials that, in a given environment, undergo corrosion. ...
Why is it important to choose the right alloy?
In addition, it is important to follow certain precautions during the processing, welding and installation of the elements , so as to ensure optimal hold over time.
Is stainless steel indestructible?
Today we wanted to talk about corrosion, a theme that is often recurring in the questions that come to us on our blog. In fact, the word “stainless” makes us believe that components made of stainless steel are indestructible.
Can stainless steel withstand any environment?
This choice is often due to the belief that stainless steels can withstand any environment and any operating conditions. It must be thought, however, that there are different types of stainless steels that can react in different ways depending on the application and conditions.
How to prevent pitting of aluminum?
The addition of a passivation agent such as nitrate to the corrosive medium, where ver feasible, can also reduce the risk of pitting. Increasing the pH value of the corrosive medium can also reduce pitting damage. In the case of aluminum, pitting corrosion is often seen as an aesthetic problem.
What does pitting corrosion look like?
At first glance, pitting corrosion looks like a tiny localized type of electrochemical deterioration found on metallic surfaces that often goes unnoticed. However, it could be a dangerous form of deterioration from a material integrity point of view. On the surface it might appear to be confined to a tiny point or spot, ...
How to determine critical pitting temperature?
The critical pitting temperature (CPT) is determined (via ASTM 48 Method C and E) by immersing the sample metal in a 1% solution of ferric chloride. The lowest temperature at which pitting begins in this solution is recorded as the CPT for the given composition of steel. Researchers have found that a relationship exists between the critical crevice corrosion temperature CPT as well as the PREN for chromium-nickel alloys as well as stainless steels.
What are the main factors that cause pit formation?
Material defects such as inclusions, surface quality and corrosive chemicals such as chlor ide salts present in the environment are the main factors responsible for any initial pit formation. Metal oxide layers acting as passive films are easily attacked by the chlorides. Automatic healing or repassivation of the pit may begin only if a supply of oxygen is ensured through continuous aeration at the site of pit initiation. Repassivation is also facilitated by alloying elements such as molybdenum, vanadium and chromium present in the metal. (Learn more about passivation in Using Pickling and Passivation Chemical Treatments to Prevent Corrosion .)
Why is aluminum pitting bad?
However, in some instances it may affect the structural component performance, resulting in a premature failure. Chlorides and sulfates in the environment are the main culprits for this deterioration by pitting.
What is wall loss?
Loss of wall thickness (i.e., wall loss) of structural members and pipes has important implications for various mechanical capabilities such as flexibility, tensile strength and compressive strength. An innocuous pit can become a stress raiser, cause initiation of failure due to stress corrosion cracking (SCC) or fatigue cracks, and even result in the catastrophic collapse of structures or ruptured piping with disastrous consequences. (For an example of a corrosion-induced pipeline failure, see INFOGRAPHIC: The El Paso Natural Gas Company Pipeline Explosion .)
Where does pitting occur?
Pitting can occur on an exposed metal substrate, where anodic reactions (oxidation) are constricted inside the particular pits and the balancing cathodic reactions (reducer reactions) occur in the adjacent areas. The presence of strong stagnant electrolytes as well as surfaces with imperfections can also contribute to pitting activity.
What Causes Pitted Stainless Steel?
Chlorine and chloride salts are responsible for metal pitting on stainless steel. They cause a breakdown of the passive chromium oxide layer on the metal, and once the pitting starts, it can spread rapidly. The Stainless Steel Information Center advises that several substances that contain chlorides can cause pitting, which can form deep crevices and even spread all the way through the metal.
Why is my stainless steel pot whitish?
One of the most common stainless steel discoloration causes is hard water. It leaves calcium deposits on stainless steel that create a dull, whitish film that you can't remove with soap and water. The best way to get rid of hard water stains is to soak the pot in a 50/50 solution of water and household vinegar, ...
What is the hardest metal to repair?
It's an alloy of steel and chromium, which is one of the hardest metals. The chromium combines with oxygen to form a layer of chromium oxide, a type of rust that prevents more damaging iron oxide rust from forming. Chlorine can damage that layer and cause a condition called pitting, and pitted stainless steel can't be repaired.
Is stainless steel better than regular steel?
Image Credit: FabrikaCr/iStock/GettyImages. Stainless steel is easier to keep clean than regular steel, and it's more rust resistant. However, the metal can definitely get stained, no matter ...
Can you pit water with salt?
Besides chlorine, the pitting reaction requires oxygen, so you can avoid pitting by adding salt only after water has come to a boil. At that temperature, there isn't enough oxygen in the water for the reaction to occur. It's also important to avoid the use of bleach and other cleaners containing chlorine, including (and especially) muriatic acid, ...
Can stainless steel be scrubbing?
None of these are as serious as pitting, and you can usually remove them, but not by scrubbing with a steel wool or an abrasive cleaner.
Can you remove rust from stainless steel?
Abrasives create small scratches in the surface layer and expose the steel underneath, which can form iron oxide rust. You can remove iron rust by wiping the pan down with a nonabrasive cloth or sponge and a paste of baking soda and water, or you can use Bar Keepers Friend®.
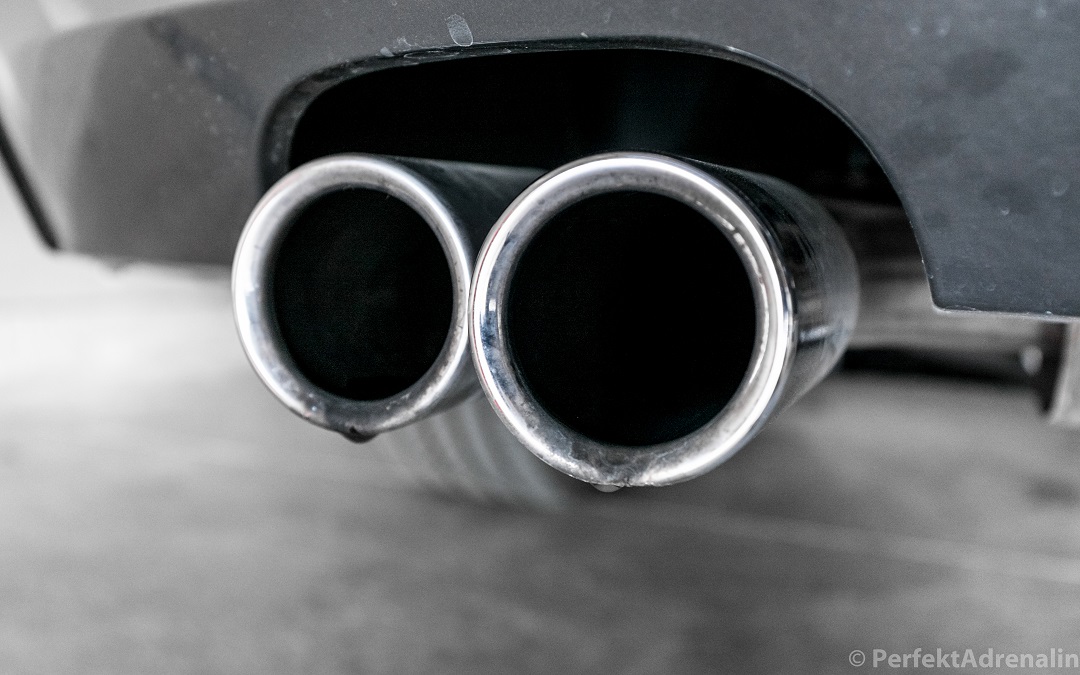