
TESTING AND INSPECTION METHODS:
- Brinell, Rockwell, Vickers and Knoop hardness tests can be applicable to welds.
- Hardness testing of welds is performed on ground, polished, or polished and etched cross-section of the joint area.
- Indentations are made in the specific areas of interests, including the weld center line, face or root regions of the deposit, the HAZ, and the base metal.
What are the two type of testing of welds?
Weld Testing can broadly be broken down into two different types; non-destructive testing (NDT) and destructive testing.
How do you test weld quality?
The basic method of checking the quality of a weld is to inspect it for any flaws visually. Look for any cracks, beads, bends, craters, excessive reinforcements, or other flaws and inform any concerned authorities about it.
Which tool is used to check welding joint?
A pit gauge or a bridge cam is handy for measuring pits in the wall of base material, undercut, or the amount of reinforcement of a weld, whether it's convex or concave.
How do you test cracks for welding?
This testing method consists of establishing a magnetic field in the part to be tested, applying magnetic particles to the surface of the part, and examining the surface for accumulations of particles that indicate discontinuities. A magnet will attract magnetic particles to its ends or poles, as they are called.
What is standard testing in welding?
Non-Destructive Weld Testing Standards cover multiple possible methods of testing welds or metallic materials. Non-destructive testing analysis techniques are used for QA, evaluations, research, in cases where the product is expensive or unique, failure analysis, and so on.
What is the most commonly used method of weld inspection?
What is the most common weld test? The two most common types of weld tests include Radiographic and Ultrasonic testing. These NDT methods are commonly used because they can detect internal flaws and irregularities. In addition, they can do so without destroying or affecting the integrity of the weld.
What are the three stages of welding inspection?
The 3 Stages of Weld Inspection As noted above, proper weld inspection techniques should be present in all three stages of the welding process: before the weld, during the weld and after the weld.
What are 3 basic types of destructive testing?
The most common types of destructive testing methods are: Aggressive environment testing. Corrosion testing. Fracture and mechanical testing.
What are the major 5 NDT methods?
The 8 Most Common NDT MethodsVisual NDT (VT)Ultrasonic NDT (UT)Radiography NDT (RT)Eddy Current NDT (ET)Magnetic Particle NDT (MT)Acoustic Emission NDT (AE)Dye Penetrant NDT (PT)Leak Testing (LT)
How do you test for metal cracks?
Currently, conventional nondestructive testing techniques used for crack detection on metal surfaces include magnetic testing, penetration testing, and eddy current testing.
What is crack detection?
Crack detection is the process of detecting the crack in the structures using any of the processing techniques. The crack detection can be made in two ways. They are Destructive Testing and Non-Destructive testing.
What is used to inspect welded joints for faults?
Fluorescent-Penetrant Examination: A fluorescent penetrant is applied to one side of the joint and a portable ultraviolet light is then used on the reverse side of the joint to examine the weld for leaks. Inspect the root pass of highly critical pipe welds.
What is meant by weld quality?
The weld quality of a joint is highly dependent on factors like material properties, spatial distribution, e.g., location of heat sinks along the weld path and geometry of joint, temporal history of the material temperature of the welding process and cooling rate [329].
What are 3 basic types of destructive testing?
The most common types of destructive testing methods are: Aggressive environment testing. Corrosion testing. Fracture and mechanical testing.
What are the major 5 NDT methods?
The 8 Most Common NDT MethodsVisual NDT (VT)Ultrasonic NDT (UT)Radiography NDT (RT)Eddy Current NDT (ET)Magnetic Particle NDT (MT)Acoustic Emission NDT (AE)Dye Penetrant NDT (PT)Leak Testing (LT)
What is welding inspection and testing?
Testing and Inspection Methods Inspection usually involves the examination of completed welds to establish their quality and their confirmation to specifications. Thus, testing and inspection determines whether or not the quality standards of materials and workmanship are being met.
What tests are applicable to welds?
Brinell, Rockwell, Vickers and Knoop hardness tests can be applicable to welds.
How to do echo on a welded component?
In welded components this is usually done by moving a small probe, containing both transmitter and receiver, over the item to be examined and displaying the echo on an oscilloscope screen.
How is tensile strength determined?
Tensile strength of the welded joint is obtained by pulling specimens to failure. Tensile strength is determined by dividing the maximum load required ...
What is the purpose of a tensile test?
This is used to find tensile strength and ductility properties of the weld. Two end of specimen is held in a tensile testing machine and load is applied on it. During the test elongation of gauge length marked initially are measure by load dial.
What is liquid penetrated examination?
Liquid-penetrated examination is a highly sensitive, nondestructive method for detecting minute discontinuities (flaws) such as cracks, and porosity, which are open to the surface of the material being inspected..
Can surface cracks be determined?
It is also possible for the depth of surface cracks to be determined. It is of limited use for interrogating welds, however, being most commonly used in the examination of continuously welded tube.
Why do welders do bend tests?
This is the most popular test and it’s used to test the skill and integrity of you, the welder. To tell you the truth, it’s common because it is quick and simple to do. No advanced tools are needed so basically any welder can perform a bend test.
What Are Welding Joints?
So, what actually are weld joints? Although it seems pretty obvious — and to tell you the truth, it is — we’re going to be diving into the specifics.
What Are The Strongest Welding Joint?
What are the strongest welding joints? professional welders will tell that tee joint or corner joints are the strongest because of a proper penetration while using an arc welder.
What Is The Hardest Metal To Weld?
Specially for beginners, aluminum is considered the hardest metal to weld.
What is a tee joint?
Fillet weld tee joints are used mainly in buildings and bridgework. Normally, they include plate girders, stiffener, endplates, and bracing connections. Since they’re the most common style (in arc-welding) used when performing a tee joint, you may have done his hundreds of times without even knowing.
How to weld a hole with a torch?
Point the torch straight into the hole. Start welding. Do not move the welder until the hole is almost completely full. Once you have reached this point, move the welder outwards in circular motions until it’s complete. While you don’t necessarily need a specific plug welding clamp, it’s incredibly useful.
What is plug welding?
Plug welding is a style used when spot welding can’t be done. Most of the time, rally car builders love to use this since a spot welder can’t fit into the crevices.
Type of Welding joints
A lap joint can be made when two plates need to be welded then they will be welded by overlapping one on another. the welding is done at the edges of the two plates.
Calculating Welding Joint Strength
For the following Welding joints, we are going to calculate the strength of the Welding Joint.
1. Strength of Transverse Fillet Welded Joints
The transverse Fillet joints are obtained by overlapping the two plates one on another and welding the edges of the plates. these Transverse fillers are capable of withstanding high tensile Load. Let us calculate the Welding Joint strength for the single and double transverse fillet welds as shown below figures.
2. Strength of Parallel Fillet Welded Joints
The Strength of Parallel Fillet Welded Joints is mainly capable of withstanding the shear load. Instead of the tensile strength as we considered in the transverse fillet joint, we have to consider the shear strength of the filler material for the parallel fillet welded joint.
3. Strength of Combination of Transverse and Parallel fillet welded joint
Now let us combine the transverse fillet welded joint with the parallel fillet welded joint.
4. Strength of Circular Fillet Weld Subjected to Torsion
In this case, a solid circular rod is going to be welded on the plate. then the welding is done around the circular edge of the rod as shown in the below figure. For this kind of welding joint, we need to calculate the weld joint strength of the solid rod is being twisted and produce torsional load.
5. Strength of Circular Fillet Weld Subjected to Bending moment
Similar to the above welding of a circular solid rod on a plate, when the rod is subjected to the bending moment as sown in the below figure then we need to consider the section modulus of the weld section instead of the polar moment of inertia.
What is welding joint?
A welding joint is referred to an arrangement or configuration of two metal plates that will be fit together. The purposes of welding are infinite, and different processes require different types of welds and joints.
How many welding joint types are there?
According to the American Welding Society (AWS), there are 5 basic additions that are commonly known and applied. These welding joint types are each stands for the needs and forces of different applications. So, let’s discuss them one by one.
How is a tee joint formed?
It is formed, when the two metal plates are intersected to an angle of 90° with one plate is lie on the center of the other plate like a “T” shape. It is known as tee joint welding. These types of welding joints are considered the use of fillet welds mounted on both sides.
What is lap welding?
It is basically a modification of butt welding, in which the two metal plates are placed in an overlapping position that is on top of each other, it is known as lap joint welding. The lap joint welding is applied for welding two metal plates that are different in their thickness.
Why is welding joints more economical?
Applying the welding joints in industries can be more economical and requires less labor and less material. And also the efficiency of the welded joint is higher than the riveted joint.
What is corner joint welding?
Corner joint welding. 1. Butt Joint Welding. These types of welding joints form when the two metal pieces are placed end to end together in the same plane surface, it is known as but t joint welding. In welding, this is the most common type of joint.
What is the difference between a tee joint and a corner joint?
As compared to the tee joint, plates are placed in the middle, whereas in the corner joint, both the plates meet in either an open or closed way to form a shape like “L”.
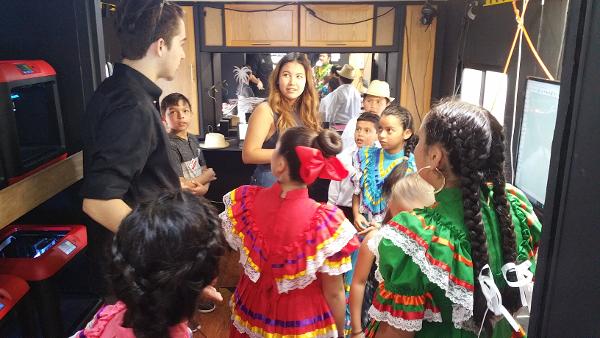