
How They Work
- Air Expulsion – The oil-less compressor runs through a set of steps during it’s “on-time”. The compressor first draws in...
- Filtration – The purpose of the filter is to eliminate any contamination to the air and ensure that no damage comes to...
- Pressurization – The air is then pressurized within the compressor. Once the compressor completes the...
Full Answer
Could I have too much oil in the compressor?
If you were to overfill your air compressor with too much oil it can cause detrimental effects. Filling the sump to the top can likely result in serious and significant internal damage to your air compressor unit which you should aim to avoid! What can happen if you under-fill an air compressor with oil?
Is an oil-free compressor really better?
When it comes down to it, oil-based compressors are better for heavy duty applications and they generally have a long service life. Oil free compressors, on the other hand, are lower in cost but are known to be less reliable and less powerful than an equally sized oiled air compressor.
Is compressor oil the same as hydraulic oil?
Though hydraulic oil is a good air compressor oil substitute, they are not the same. Hydraulic oil has more additives than air compressor oil. For example, hydraulic oil has the AW (anti-wear) additive which air compressor oil doesn’t have.
What type of oil should I put in my compressor?
Types of Compressor Oil: Based on Compressor Mechanism
- Oil-free (no oil is needed)
- Lubricant oil for air compressor pump
- Oil for rotary screw model
- Diesel or gasoline engine oil

How does an oil-free air compressor work?
An “oil-free” air compressor does not use any lubrication in the compression chamber. Instead, these compressors use alternate materials that protect the pump, such as water or a Teflon coating, and allow the mechanism to move smoothly without the need for any oil-based or synthetic lubrication.
Are oil less compressors any good?
While oil-free air compressors are cheaper, lighter and require less maintenance, oil air compressors are more durable. As the oil-free compressors are pre-lubricated, there is no constant maintenance and the unit tends to get dry when the Teflon starts wearing out. They don't last as long as oil air compressors.
What is an oil less compressor?
Oilless compressors do not use oil for lubricating. Instead, their wearable parts are coated in special friction-reducing chemicals and are designed to be self-lubricating for the life of the compressor.
How long does a oil less air compressor last?
Oil-free piston air compressors typically last around 10-15 years, while oil-free rotary screw compressors tend to last around 20-30 years. You can generally expect anywhere from 2,000 to 8,000 hours of service.
What is the advantage of an oil-free air compressor?
Switching from an oil-flooded to an oil-free air compressor provides operators with significantly lower maintenance requirements, including: Fewer ancillary air system components to maintain. Longer timeframes between oil changes. Elimination of expensive oil filters to clean the compressed air.
How quiet is the oil-less compressor?
Air compressors can get up to 70-90 decibels loud – the average conversation is about 60 decibels, so bring in 2-3 oil-less air compressors running at full capacity and you'll definitely have a noise problem.
What is the difference between oil-free and oil compressor?
Oil air compressors makes use of oil for the lubrication. On the other hand, oil-free air compressors does not need to be lubricated with oil. You don't have to change any oil once you start using it. To get around this, the pump mechanism like the piston and housing are coated with materials such as Teflon.
Do you have to put oil in an air compressor?
Air compressors require constant oil lubrication to prevent friction on the pistons or screws and other moving parts. To make sure your air compressor is running efficiently, it is important to check your oil level regularly and to know how much oil your compressor needs.
How is an oil-less compressor on recovery units lubricated?
Oil-less compressors do use oil. A chamber houses the oil keeping it separate from the compression chamber. Other materials lubricate the piston so it moves freely within the compressor cylinder. On the other hand, an oil-lubricated compressor uses oil to lubricate the piston for air pressurization.
Do you need to break in an oilless air compressor?
I know from experience that break-in is required and a good idea for oilless compressors. I was unaware of that instruction once with a new one and sure enough it failed to reach its rated maximum psi after a single first success. From then on, it consistently came 10 pounds short.
Can you lay an oil less air compressor on its side?
Air compressors are configured to be either oil-lubricated or oil-free. Oil-lubricated compressors require users to manually add oil to the sump after purchasing. However, this feature comes with a caveat – you should not lay the oil-lubricated compressor on its side after adding oil to the sump.
How often should you change air compressor oil?
Generally speaking, a rotary screw air compressor's oil should be changed every 1,000 to 2,000 service hours, while a reciprocating air compressor's oil needs to be changed every three months. If you notice performance issues with your air compressor, check the oil first—it may be affecting the pressure and efficiency.
Are belt driven compressors better?
Many experts believe a belt drive compressor is better because a properly lubricated belt system will run in a more smooth manner, which can be both efficient and quiet. On the other hand, belts can wear down, causing you to repair or replace the belts to ensure the compressor is able to function again.
How are oil less compressors on recovery units lubricated?
Oil-less compressors do use oil. A chamber houses the oil keeping it separate from the compression chamber. Other materials lubricate the piston so it moves freely within the compressor cylinder. On the other hand, an oil-lubricated compressor uses oil to lubricate the piston for air pressurization.
Do electric air compressors need oil?
Air compressors require constant oil lubrication to prevent friction on the pistons or screws and other moving parts. To make sure your air compressor is running efficiently, it is important to check your oil level regularly and to know how much oil your compressor needs.
What is an Airend?
The assembly that includes the rotors and the housing they're in is called an “air end” or airend. This is the terminology for all rotary compressors, whether they be rotary vane, scroll, screw or lobe – the part that compresses the air is called the airend.
Why do oil free compressors use less energy?
Low energy use: Oil-free compressors use less energy because they don’t need to increase force for oil filtration.
How hot does a compressor get?
Compressor elements typically generate a lot of heat, causing the unit to operate at up to 180 degrees. This is much hotter than oil-lubricated compressors.
How to contact Wenniger Compressor Co?
Our team specializes in air compressors, high-pressure air compressors and more. Reach us today for professional input at 414-372-5320.
What is the maximum pressure of air compressor?
The high-pressure element will further compress the air, typically achieving a maximum pressure of 116 to 143 psi (pounds per square inch). This process generates even more heat, so cooling is again necessary.
What does a pressure switch do?
A pressure switch monitors how much air is left in the compressor. If the volume falls below a certain level, the compressor will turn on and rebuild more pressurized air for the tank. If the pressure switch fails, the compressor will not refill and will require air compressor repair.
Why do filters need less maintenance?
Low maintenance: Because no oil is used in the process, you do not have to collect or dispose of oily condensate. Additionally, because the filters are not handling oil, they require less frequent replacement.
Does an air compressor have oil?
If you have an oil-free compressor, it’s important to understand how it works in case you ever need air compressor repair. The first thing to understand is that the device actually does contain oil. However, the oil will not be in contact with the compressor—the oil is only in the gearbox.
Why is it important to lubricate air compressors?
For most applications, lubricated air compressors are perfectly acceptable – the oil reduces friction between moving parts, and this can improve efficiency, reduce maintenance demands, and may have safety implications in explosive environments where friction could raise heat levels by an unacceptable extent .
Do air compressor rotors touch?
Air compressor parts such as the rotors typically do not touch at all in oilless air compressors, instead passing very very close to one another without making contact.
Why is oil used in compressors?
Although oil is not used in the process of compressing air to come into contact with air, oil is still used to cool the compressor and lubricate the operating parts, so that the compressor can operate normally and stably.
How fast is a water lubricated air compressor?
6) The water-lubricated air compressor uses water to cool and lubricate the seal, the air quality is guaranteed, and the speed is about 3000 rpm. The temperature is around 55 degrees, and the maintenance cost is low.
What is a single screw air compressor?
1) The single-screw water-lubricated air compressor uses pure water for lubrication and cooling. The internal parts of the body are made of special materials, medical-grade stainless steel, and will never corrode.
What temperature should water be when lubricating?
That is, the ambient temperature cannot be lower than 0°C, otherwise the pure water used as a lubricating medium will freeze!
What is the temperature of an oil free machine?
The cooling oil of the dry-type oil-free machine is about 100 degrees, and the temperature of the compression chamber exceeds 200 degrees. The temperature difference is relatively large, so the energy consumption is relatively high.
Is water lubrication the same as air cooling?
Water cooling is a heat dissipation method, in addition to air cooling; and water lubrication also has air cooling and water cooling heat dissipation methods, its advantage is that ordinary air compressors need to add air compressor oil, while water lubrication air compressors Only pure water is needed to replace lubricating oil.
What is the operating temperature of a dry type oil free machine?
The operating temperature of dry-type oil-free machines is higher than 200 degrees, which directly affects the life of the cooling oil and bearings.
How does an air compressor work?
In order to compress air, the internal components of a compressor must move or change position to mechanically force the air through the chamber where it is compressed and stored until use.
Why are piston compressors louder?
Piston compressors are notorious for being louder because the internal components rub together and create friction. However, advancing technology is improving the way they operate by introducing dual and multi-piston, single-stage models that use up to 4 pistons inside the pump. By using multiple pistons, it's possible to extend the life of the unit by dividing up the work of a single-piston and achieve a supremely quiet air compressor.
How does a positive displacement air compressor work?
Air is drawn into the compressor where the internal components reduce the volume of the air by creating a vacuum, which drives the pressure of the air up as it is pushed into a holding tank. Once the maximum pressure is reached inside the tank, the duty cycle is complete, and the compressor shuts off until the pressure falls below a set threshold. Positive displacement air compressors do this in different ways: by using pistons, screws, and scrolls.
Why do spiral pieces rotate?
Two spiral-shaped circular pieces rotate around one another to compress incoming air. One scroll is fixed in place and doesn't move, and the other fits inside the stationary scroll and moves in a tight circular motion without rotating.
Why is direct drive used in compressors?
This is the more economical option and is widely used across all compressor types because the belts can be adjusted to change with air demands. In a direct-drive system, the motor attaches directly to the crankshaft of the compressor, allowing for smaller designs and fewer maintenance requirements.
What happens to air when it is compressed?
The concept of compressed air is simple: when atmospheric air is stored under pressure, it creates potential energy that can be held inside a tank until it's needed. Just like a balloon being released, when the pressurized air is released, the potential energy is converted into usable kinetic (motion) energy.
Do air compressors need lubrication?
Just like your car uses oil, air compressors need lubrication to continue running smoothly over time.
How does a natural gas compressor work?
Natural Gas Compressors work by mechanically increasing gas pressure in stages (or steps) until it reaches the desired delivery point . The starting pressure and the desired ending pressure will determine how many stages a compressor will have.
How does a reciprocating compressor work?
A natural gas reciprocating compressor uses pistons and positive displacement to compress the gas. Gas enters the manifold, flows into the compression cylinder, then discharges at a higher pressure.
Why Do We Compress Gas?
Compression is used in every sector of our industry when conditions do not normally exist for various processes to take place.
How does a screw compressor work?
A screw compressor uses two meshing helical screws or rotors to compress the gas. Gas enters the suction side and moves through the threads. As it does it is compressed and then exits at the discharge side at a higher pressure. Screw compressors are typically used for lower pressure and lower volume like a VRU.
What is the purpose of compression in a well?
Upstream—producers often use compression to inject gas back into the well to aid in lifting liquids to the surface. They also use it to compress low pressure gas off tanks, control devices and other equipment to help dispose of fugitive emissions ( VRU ).
Why do producers use compressors?
Many producers choose to compress air so they can use it for instrument supply while reducing their emissions and lower their environmental impact.
What is the pressure of the third stage of compression?
The third stage of compression gets the pressure up to 1200 psi and 240° F. Once again, the hot gas will go through the cooler and exit the at the discharge at 120°F. Some producers will run the gas through one last scrubber to give any remaining liquids a place to drop out.
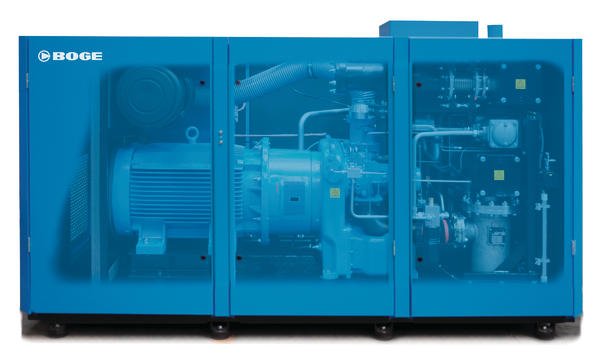