
What is the maximum width of a precast concrete panel?
I have a steel framed tower that will be clad with precast concrete panels. The floor to floor height is 11'-8" on the tower. The maximum width of the panel is about 17' per the architectural elevations. I'm planning to use 5" panels with 3/4" reveals. The panel design is delegated to the contractor.
How thick should a concrete wall be in an apartment?
Four to twelve inches is a good thickness range for precast concrete walls when built solidly. Insulation should be incorporated into a thin-shell wall’s thickness of between 5 and 12 inches. Sandwich precast concrete walls, with the 1-4-inch insulation, should be 5-12 inches thick as well. How thick are concrete walls in apartment buildings?
What are precast concrete wall panels and veneer?
Precast concrete wall panels and veneer are typically lightweight and easy to install, with products ranging from thin brick veneer to cladding inspired by limestone, travertine and other stone products.
How thick should insulation be on a precast concrete wall?
Insulation should be incorporated into a thin-shell wall’s thickness of between 5 and 12 inches. Sandwich precast concrete walls, with the 1-4-inch insulation, should be 5-12 inches thick as well.
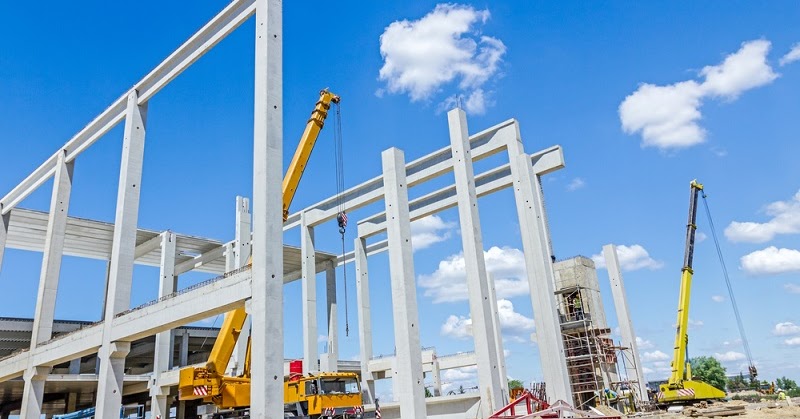
How thick are cast-in-place concrete walls?
For single-family residential construction, wall thicknesses can range from four to 24 inches. Uninsulated walls are typically six or eight inches thick.
Do precast concrete walls crack?
Here, we will discuss how cracks in precast concrete wall panels form, providing tips on how to fix concrete cracking. Concrete wall panels are one of the most common types of concrete to crack. That's because they are being tilted from horizontal to vertical while they are being created.
Are precast concrete walls cheaper?
A recent research project directly compared the costs of precast concrete to on-site pouring and found precast concrete slabs save 23 percent over cast-in-place concrete. Columns yielded a similar result, with savings at 21 percent less cost than on-site pouring.
How long does a precast concrete wall last?
The biggest of these is temperature. Precast concrete structures have a lot to live up to; they must endure all manner of environmental conditions. Ideally, such products should last 50 to 100 years or more. Curing the concrete in a controlled environment is key to its longevity.
How do you fix a crack in precast concrete?
Mix enough ready-mix concrete with water to fill the hole or crack and apply it rapidly. Press the concrete mixture into holes and cracks with the handle of your trowel and smooth it on the surface evenly. Cure the fixed spot as explained in Step 3, including sealing it with a silane-based water-repelling sealer.
What causes new concrete walls to crack?
When concrete expands, it pushes against anything in its way (a brick wall or adjacent slab for example). When neither has the ability to flex, the expanding force can be enough to cause concrete to crack. Expansion joints are used as a point of separation (or isolation), between other static surfaces.
What is the disadvantage of precast concrete?
Usually, precast members are heavy and large which makes it difficult to handle without damage. Generally, portable or tower cranes are used to handle precast members. Modification: Limitation In case of precast structures, it is difficult to modify the structure.
Are precast walls strong?
Precast compound walls are made from concrete and steel materials which are heavy and durable compared to traditional brick walls.
Does precast concrete have rebar?
Rebar is placed inside precast concrete forms in order to provide reinforcement, particularly when it comes to tensile strength.
Are precast concrete walls expensive?
Precast concrete is estimated to be 23% less expensive than poured concrete. Installing a precast concrete wall costs $4,800 on average. While precast materials cost from $20 to $30 per square foot, precast installation is much less labor-intensive than pouring concrete.
Is hollow blocks better than precast?
Precast Concrete is Stronger and More Durable After all, both are made from concrete, and both are typically reinforced with steel. However, hollow blocks end up being not as durable and strong in the real world thanks to the many mortared joints. Those types of joints are less strong than the concrete itself.
Are precast concrete walls good?
They are resistant to mold, fire, rot, and termites, among other natural hazards. They are sustainable over long periods of time without maintenance. They are an energy efficient option when used structurally. Precast Brick wall is cost effective because it requires little to no maintenance over time.
Why do concrete ceilings crack?
There are two main causes of ceiling cracks: Structural damage and the natural settling that happens as a building ages. Ceiling cracks can also be caused by poor workmanship.
How do you repair concrete walls?
0:382:05Concrete Repair Tips for Beginners - YouTubeYouTubeStart of suggested clipEnd of suggested clipAs anchors. If you want to speed up this process you can use an sds hammer drill. This is a greatMoreAs anchors. If you want to speed up this process you can use an sds hammer drill. This is a great tool for old concrete that is really strong you can drill through it no problem whatsoever.
What is precast concrete?
The precast concrete wall can be used as load-bearing structures and will save costs by eliminating the need for an additional structura l framing system. Precast concrete walls can be designed to be reused for future building expansions.
How are precast walls made?
Precast concrete walls are constructed by casting concrete in a reusable wall mold or form which is then cured in a controlled environment , transported to the construction site and lifted into place . The main function of the precast walls is to speed up the construction process.
What are the advantages of precast concrete?
Advantages of Precast Concrete Walls 1 Precast concrete walls act as thermal storage to delay and reduce peak thermal loads. 2 The precast concrete wall is used as an interior surface which saves time and money by eliminating the need for separate stud framing and drywall costs. 3 The precast concrete wall can be used as load-bearing structures and will save costs by eliminating the need for an additional structural framing system. 4 Precast concrete walls can be designed to be reused for future building expansions. 5 Precast concrete’s durability creates a low maintenance structure, which stands up to harsh climate conditions. 6 Precast concrete colors and finishes can be achieved through the use of various aggregates, cement, pigments and finishing techniques. 7 Precast concrete wall panels can utilize a thin brick veneer that can achieve a traditional appearing facade. 8 Precast concrete walls can be produced with textures including form liner shapes, artwork, and lettering to provide distinctive accent treatments. 9 Precast concrete wall panels can have electrical boxes and conduit cast into the panels, to provide flush electrical fixtures on walls that are not to be framed out.
What is a curtain wall?
The cladding or curtain walls are the most widely used precast wall for building envelopes. They are non-load bearing walls intended for the use to oppose the wind and encase the space. This type of precast wall incorporates divider boards, window divider units, spandrels, mullions, and section covers.
Why is it important to assess the plan, specifying and erection of precast walls?
It is critical to assess the plan, specifying and erection of precast walls to abstain from forcing undesirable burdens onto the walls. Loads such as erection, affect, and development related, and transportation of the precast walls are to be considered in the design phase.
What is shear wall?
Shear walls are utilized to give a parallel load opposing framework when joined with stomach activity of the floor development. The viability of precast shear dividers is generally needy upon the board-to-board associations.
What is load bearing wall unit?
Load-bearing wall units oppose and exchange loads from different components and cannot be removed or dismantled without influencing the quality or dependability of the building.
How thick should a concrete wall be?from askinglot.com
Hereof, how thick is a concrete wall? In general, poured concrete basement walls that are 8 feet tall or less and have no more than 7 feet of soil pressing against them from the outside function well at a thickness of 8 inches. When a taller wall or a higher level of soil or both come into play, the thickness should increase to 10 inches.
How thick is a tilt up concrete panel?from askinglot.com
What is the Typical Thickness of a Tilt-Up Concrete Panel? The panel itself is usually between 5 ½ inches or 7 ¼ inches thick. However, keep in mind that these can be as little as a few inches thick.
What is a Versacore+Green Sandwich Panel?from fabconprecast.com
A Versacore+Green Sandwich panel is the only standard precast panel that has a 4-hour fire rating.
What is the exterior surface of precast concrete?
The exterior surface of precast concrete can vary from an exposed aggregate finish that is highly ornamental to a form face finish that is similar to cast-in-place. Some precast panels act as column covers while others extend over several floors in height and incorporate window openings.
What is precast shear wall?
Precast concrete shear wall panels are used to provide lateral load resisting system when combined with diaphragm action of the floor construction. The effectiveness of precast shear walls is largely dependent upon the panel-to-panel connections.
What is the ACI code for precast concrete?
The concrete panels are designed in accordance with PCI Design Handbook-Precast and Prestressed Concrete (MNL-120), Design Responsibility for Architectural Precast Concrete Projects (ACI 533.1R-02), and ACI 318 Structural Concrete Building Code. Steel elements of a wall system are designed in accordance with AISC specifications for steel construction. Precast concrete elements are designed in accordance with ACI and PCI specifications.
What are the different types of precast panels?
There are generally four types of precast panels used as part of building envelopes: Cladding or curtain walls. Load-bearing wall units. Shear walls. Formwork for cast-in-place concrete. Precast cladding or curtain walls are the most common use of precast concrete for building envelopes.
Why are joints important in a precast concrete envelope?
The joints between precast units or between precast and other building components must be maintained to prevent leakage through the precast wall system.
Why is my precast concrete wall cracking?
Most distress and deterioration encountered with precast concrete wall systems can be attributed to problems during erection, an chors used to attach panels to the structure, or corrosion of the embedded reinforcing steel. Panel cracking, displacements, or other distress conditions can occur at locations where anchors are inadequately or improperly connected. Poor construction is often the result of poor quality control and out of tolerance fabrication or erection of the panels. Also, damage from handling during construction can result in panel cracking, some of which may not become evident for several years.
How are precast panels supported?
Typically, each precast panel is independently supported to the building structure using an assemblage of metal components and anchors. Joints around each of the precast panels are usually filled with sealant.
What is precast concrete?
Precast concrete wall systems can be comprised of a variety of shapes, and wall types. Typically, precast concrete wall systems fall into three basic categories : solid, sandwich and thin-shell. These can be panelized and erected in either a horizontal or vertical position and used on all types of structures, from residential to commercial, institutional to industrial. Wall panels can be designed as non-loadbearing or loadbearing, carrying floor and roof loads, as well as lateral loads.
What is a solid wall panel?
Solid wall panel refers to walls being made of solid concrete as opposed to including integral insulation. These wall systems require some form of insulation and an interior wall/finishing system to complete the building enclosures.
What is a thin shell wall panel?
Thin-shell wall panels consist of a thin, outer-wythe of concrete typically ranging between 1.5 and 3 inches in thickness. This is connected to a back-up system, usually constructed of steel framing or studs, or sometimes concrete. The back-up system is what connects the wall panel to the structural system of the building and often provides the furring for interior finishes, such as drywall to be attached. Many of these systems can also incorporate a layer of rigid insulation between the exterior wythe of concrete and the back-up system.
What is sandwich wall insulation?
The difference between typical panels and insulated sandwich wall panels is that the latter are cast with rigid insulation "sandwiched" between two layers, or wythes, of concrete. The insulation thickness can vary to create the desired thermal insulating property (" R " value) for the wall.
What is a lite wall?
Light or "lite" walls are shear walls used in parking structures cast with an opening in their center to provide visual continuity and to allow daylight or artificial illumination to penetrate deeper into an interior. The components provide openness and a feeling of security.
Is sandwich wall insulation composite?
Whether the panel is composite or non-composite depends on the configuration and material used for the ties. Insulated sandwich wall panels can be designed to be loadbearing and support floor and roof components. They make an ideal structural element for this purpose, normally by casting a thicker interior wythe to provide the necessary support. They can also be non-loadbearing to complete a façade.
How thick are precast concrete walls?
In order for a concrete room to effectively resist high winds and flying debris, most rooms built with precast concrete walls rely on 12- to 16-inch thick blocks. To keep the house and the room from being sucked into the air during a tornado, large footings that work like anchors are added to the walls to hold the room in place.
How thick is reinforced concrete for tornadoes?
According to Texas Tech University's Wind, Science & Engineering Research Center, rooms built with 6- to 8-inch thick reinforced concrete masonry provide resistance for F5 tornadoes, the most powerful storm possible. When concrete masonry is used, you must also add conventional reinforcing bars to give the structure more strength. In addition, cavities in the concrete block are filled with concrete to give the walls even more resistance.
What are concrete safe rooms?
In the event of a tornado, concrete rooms are designed to keep you and your family safe. Image Credit: Thinkstock Images/Comstock/Getty Images. About 1,000 tornadoes hit the United State each year, according to the NOAA National Severe Storms Laboratory. Sixty people, on average, die from tornadoes annually, making concrete safe rooms with ...
Why are concrete doors so heavy?
Because concrete doors would weigh too much for people to maneuver when they need to access the room , fabricated or store-bought missile-resistant steel doors work best, according to Texas Tech University's Wind, Science & Engineering Research Center.
How much does precast concrete cost?from thepricer.org
The precast concrete price is influenced by many factors, including the origin or location of the material, the quality of the materials, the size, shape, and structure of the piece, and also by the number of pieces that are going to be purchased.
What determines the cost of a poured concrete wall?from spendonhome.com
Several factors determine the cost of a poured concrete wall such as the dimensions of the wall (the thickness, its height, and its length), the number of reinforcements present, and the quality and type of concrete used.
Why do you need pour concrete walls?from americandry.com
When you build a new home, your main priority should be to create the strongest and safest foundation possible. Poured concrete walls have become the first choice of homeowners and builders. They are easy to construct and durable. They save you from issues like premature water leakage and frequent repairs.
How does a foundation need footings?from fixr.com
Every foundation needs footings to distribute the load. The footing type is directly tied to the kind of foundation. For example, stem wall and basement foundations have continuous footings dug and poured first, then the walls, and finally the slab. Slab-on-grade ones have a thicker edge than the center. This thicker edge is the footing that supports the load. The only case where the footing has a separate price from the foundation is in a crawl space, where the footing is priced at $10 to $15 per linear foot. Otherwise, the price is part of the foundation’s square footage price.
Why are my block walls bowing?from americandry.com
Buckling and bowing are a result of either poor construction or underground lateral water pressure. Thus, repairing them can be quite expensive, depending on the extent of the damage. Here is another downside for block walls; they are more prone to water leaks because of the number of joints between each block.
How wide is a footing?from fixr.com
In general, the footings are thicker than the walls above them. Most footings start at 12” wide, and many go as wide as 20”. This is true of all types - even monolithic ones have a deep and thick footing on the perimeter, with the slab in the center being thinner.
How long does it take for concrete to cure?from fixr.com
When pouring a monolithic slab, gravel is put down for drainage, and the entire slab is poured at once. The concrete needs anywhere from 1 to 14 days to cure, depending on the weather and conditions.
Why use precast concrete?from leesburgconcrete.com
Architects love architectural precast concrete wall panels because they add to a structure’s architectural appearance. With endless options for architectural design creativity, architectural precast wall panels can be used on both interior and exterior walls. They can be cast in any size, texture, shape, or color. When manufacturing architectural precast wall panels we adhere to PCI's strict standards with regard to dimensional tolerance, color consistency, and finish variations.
How to learn more about precast concrete?from leesburgconcrete.com
If you are interested in learning more about precast concrete wall panels for your construction project, all it takes is a phone call (or an email.) We recommend getting us involved early so we can lend our expertise to your project. Our in-house design team, engineers, and technical staff have extensive experience and can help provide the best and most cost-effective solution for the needs of your project. And, if you are in the area, we welcome you to take a tour of our plant, to see samples of our products and learn how we produce the high-quality precast concrete products that we do.
What is the phone number for Leesburg Concrete?from leesburgconcrete.com
Call us at 352.787.4177 or email us today to get started on your project.
Where are precast panels made?from leesburgconcrete.com
Manufactured in our Leesburg, Florida plant, our architectural precast panels and cladding provide a strong, durable facade. They stand up to the harshest weather, rain, and wind and continue to look good year after year.
How much does a slender wall panel weigh?from leesburgconcrete.com
It is designed to be lightweight (about 30 lbs. per square foot compared to approximately 85 lbs. for traditional heavy architectural precast), reducing foundation and superstructure requirements and reducing shipping and installation costs. Read More
Is precast concrete cheaper than site poured concrete?from leesburgconcrete.com
Precast concrete panels always cost less than site-poured concrete. An article in the Journal of Construction Engineering documented a 2016 research project that compared the cost of precast concrete to pouring concrete on-site. The results showed that precast concrete panels reduced construction costs by an average of 23%. The article further addressed the fact that precast concrete reduces on-site laborers, generates less waste, less volume of building materials, and increases environmental and construction site cleanliness.
Is there downtime for precast concrete?from leesburgconcrete.com
With precast concrete panels, there is no downtime waiting for concrete to dry. Precast concrete panels are poured off site and delivered at the exact time and in the sequence you request. This allows your project to continue moving and be completed faster.

Introduction
Description
- Precast Panel Types for Building Envelopes
There are generally four types of precast panels used as part of building envelopes: 1. Cladding or curtain walls 2. Load-bearing wall units 3. Shear walls 4. Formwork for cast-in-place concrete Precast cladding or curtain walls are the most common use of precast concrete for building env… - Support and Anchorage Systems
The connections for precast concrete panels are an important component of the envelope system. Precast manufacturers utilize numerous different types of anchors but they are often characterized as gravity and lateral types of connections. The primary purposes of the connecti…
Fundamentals
- Structural Aspects of Design
Precast concrete wall systems are most often constructed as a curtain wall or veneer, in which no building loads are transferred to the concrete panels. Most typically the precast concrete wall system must resist lateral loads directly imparted on it, such as from wind and earthquake; as w…
Applications
- Precast concrete wall systems allow a wide variety of colors, finishes and architectural shapes. Precast concrete can be used in environments that allow the use of conventional cast-in-place concrete. In addition, precast concrete may be made in a controlled environment and erected in an environment that would not allow site casting of concrete. The concrete used in precast pane…
Details
- The following details can be downloaded in DWG format or viewed online in DWF™ (Design Web Format™) or Adobe Acrobat PDF by clicking on the appropriate format to the right of the drawing title. Architectural Precast Window Jamb and Sill DWG | DWF | PDF Architectural Precast Round Penetration DWG | DWF | PDF Architectural Precast Square Penetration DWG | DWF | PDF Archit…
Emerging Issues
- The necessity to make building envelopes blast-resistantforces reconsideration of precast concrete joint and connection designs.
Relevant Codes and Standards
- American Concrete Institute ACI 318—Building Code Requirements for Structural Concrete
- American Concrete Institute ACI 301—Specifications for Structural Concrete
- Precast/Prestressed Concrete Institute PCI Design Handbook-Precast and Prestressed Concrete(MNL 120)
Additional Resources
- American Concrete Institute
1. ACI 318—Building Code Requirements for Structural Concrete 2. ACI 301—Specifications for Structural Concrete 3. ACI 201.2—Guide to Durable Concrete 4. ACI 533.1R—Design Responsibility for Architectural Precast Concrete Projects - ASTM International
1. ASTM C 33—Aggregates in Concrete 2. ASTM C 457—Air Void 3. AGGREGATE REACTIVITY 4. ASTM C 856—Petrographic Analysis of Hardened Concrete