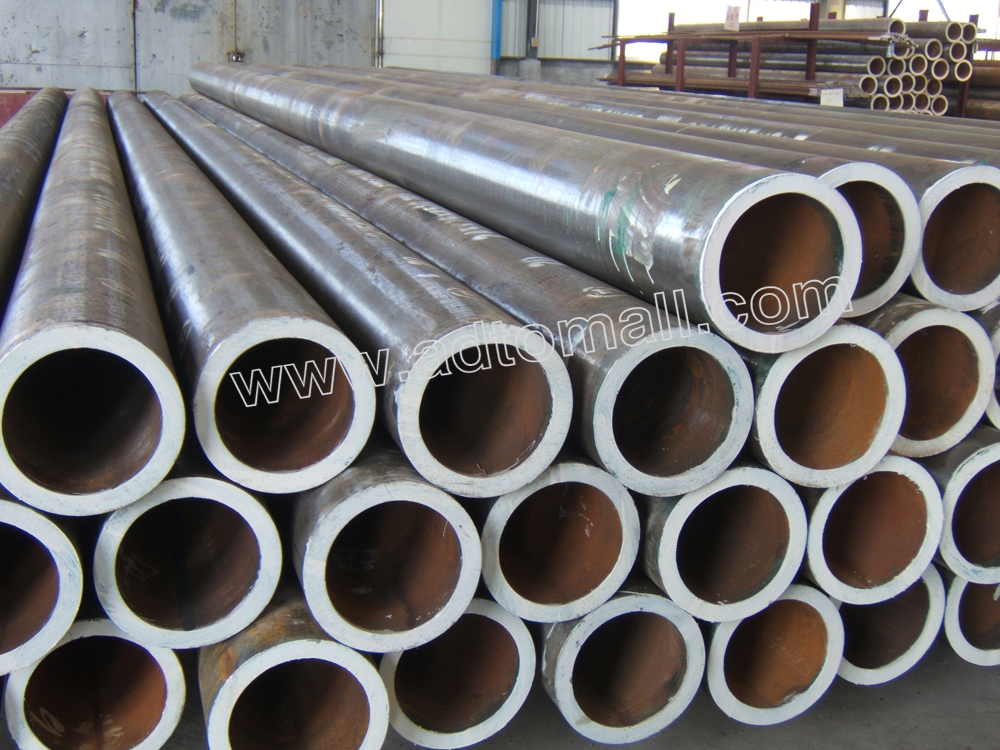
Which one is more ductile, aluminium or copper?
Which is more ductile Aluminium or copper? Additionally, copper is naturally harder, stronger and more ductile than aluminium. Cu also expands less and does not flow at terminations. Which is the most ductile metal Aluminium or copper? All Answers (3) Therefore, the Aluminum much ductile than Copper without cold working or alloying elements.
How does copper react with aluminum?
reaction of aluminum and copper(II) chloride is very vigorous—the reaction mixture gets very hot as heat is released, the blue color due to the Cu(II) ions fades, the aluminum foil disintegrates, a reddish brown solid appears, and gas bubbles are given off.
Does aluminum have lower resistance than copper?
Copper has a significantly lower specific electrical resistivity than aluminium: 100, compared to 160. To attribute to an aluminium conductor the same resistance as a copper conductor, the cross-sectional area of the aluminium conductor must become larger to compensate for aluminium's higher electrical resistivity.
What are the uses of copper alloys?
Within these devices, copper is vital to the production of:
- Electronic connectors
- Circuitry wiring and contacts
- Printed circuit boards
- Micro-chips
- Semi-conductors
- Magnetrons in microwaves
- Electromagnets
- Vacuum tubes
- Commutators
- Welding electrodes
What is aluminum copper?
What is the melting point of aluminum?
Can copper alloys be treated?
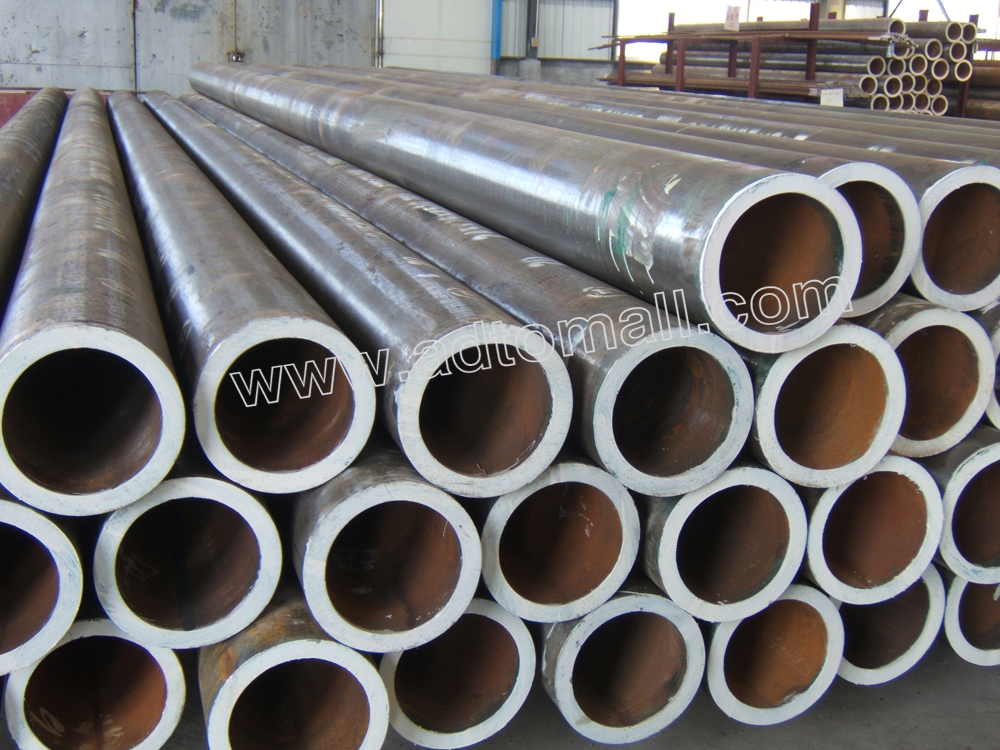
About Aluminum Copper Alloy
Aluminum Copper is one of numerous metal alloys sold by American Elements under the trade name AE Alloys™. Generally immediately available in most volumes, AE Alloys™ are available as bar, ingot, ribbon, wire, shot, sheet, and foil.
Packaging Specifications
Typical bulk packaging includes palletized plastic 5 gallon/25 kg. pails, fiber and steel drums to 1 ton super sacks in full container (FCL) or truck load (T/L) quantities. Research and sample quantities and hygroscopic, oxidizing or other air sensitive materials may be packaged under argon or vacuum.
Recent Research
Microstructural Change during the Interrupted Quenching of the AlZnMg (Cu) Alloy AA7050.
What is the use of copper in metals?
The major applications of copper are electrical wire (60%), roofing and plumbing (20%), and industrial machinery (15%). Copper is used mostly as a pure metal, but when greater hardness is required, it is put into such alloys as brass and bronze (5% of total use). Copper and copper-based alloys including brasses (Cu-Zn) and bronzes (Cu-Sn) are widely used in different industrial and societal applications. Some of the common uses for brass alloys include costume jewelry, locks, hinges, gears, bearings, ammunition casings, automotive radiators, musical instruments, electronic packaging, and coins. Bronze, or bronze-like alloys and mixtures, were used for coins over a longer period. is still widely used today for springs, bearings, bushings, automobile transmission pilot bearings, and similar fittings, and is particularly common in the bearings of small electric motors. Brass and bronze are common engineering materials in modern architecture and primarily used for roofing and facade cladding due to their visual appearance.
What is copper used for?
A freshly exposed surface of pure copper has a reddish-orange color. Copper is used as a conductor of heat and electricity, as a building material, and as a constituent of various metal alloys, such as sterling silver used in jewelry, ...
What is the use of copper in ancient civilizations?
An ancient civilization is defined to be in the Bronze Age either by producing bronze by smelting its own copper and alloying with tin, arsenic, or other metals. The major applications of copper are electrical wire (60%), roofing and plumbing (20%), and industrial machinery (15%).
What is the most common material used in aerospace?
Aluminium. Aluminium and its alloys are used widely in aerospace, automotive, architectural, lithographic, packaging, electrical and electronic applications. It is the prime material of construction for the aircraft industry throughout most of its history.
Is copper a pure metal?
Copper is used mostly as a pure metal, but when greater hardness is required, it is put into such alloys as brass and bronze (5% of total use). Copper and copper-based alloys including brasses (Cu-Zn) and bronzes (Cu-Sn) are widely used in different industrial and societal applications.
What is copper alloy?
Copper has been the most common alloying element almost since the beginning of the aluminum industry, and a variety of alloys in which copper is the major addition were developed .#N#In the cast alloys the basic structure consists of cored dendrites of aluminum solid solution, with a variety of constituents at the grain boundaries or interdendritic spaces, forming a brittle, more or less continuous network of eutectics. Wrought products consist of a matrix of aluminum solid solution with the other solible and insoluble constituents dispersed within it.
What is the composition of copper alloys?
Copper alloys containing nickel, which can be subdivided in two groups: the Y alloy type, whose basic composition is 4% Cu, 2% Ni, 1.5% Mg; and the Hyduminiums, which usually have lower copper contents and in which iron replaces 30me of the nickel. In most of the alloys in this group aluminum is the primary constituent and in the cast alloys ...
What is wrought aluminum?
Wrought products consist of a matrix of aluminum solid solution with the other solible and insoluble constituents dispersed within it. Copper has been the most common alloying element almost since the beginning of the aluminum industry, and a variety of alloys in which copper is the major addition were developed.
What is the amount of Cu in a cast alloy?
Cast alloys with 10-14% Cu. These alloys may contain small amounts of magnesium (0.10-0.30% Mg ), iron up to 1.5%, up to 5% Si and smaller amounts of nickel, manganese, chromium.
What is the basic structure of aluminum?
In most of the alloys in this group aluminum is the primary constituent and in the cast alloys the basic structure consists of cored dendrites of aluminum solid solution, with a variety of constituents at the grain boundaries or interdendritic spaces, forming a brittle, more or less continuous network of eutectics.
What is the expansion coefficient of aluminum?
Expansion coefficients are of the order of 21-24 x 10 -6 1/K for the 300-4000 K range and 23-26 x 10 -6 1/K for the 300-700 K range , with the higher values for the high-magnesium, low-copper and low-silicon alloys, the lower ones for the higher silicon and higher copper contents. At subzero temperatures the coefficient decreases practically in the same way as that of pure aluminum. However, release of casting stresses or precipitation and solution of copper and magnesium produce changes in length of up to 0.2%, which may affect the dimensional accuracy of parts exposed to high temperature. Subzero treatment of castings to reduce warpage has been recommended.
What are the constituents of an alloy?
Constituents formed in the alloys can be divided in two groups: in the soluble ones are the constituents containing only one or more of copper, lithium, magnesium, silicon, zinc; in the insoluble ones are the constituents containing at least one of the more or less insoluble iron, manganese, nickel, etc. The type of soluble constituents formed ...
What is copper alloy?
Copper alloys are metal alloys that have copper as their principal component. They have high resistance against corrosion. The best known traditional types are bronze, where tin is a significant addition, and brass, using zinc instead. Both of these are imprecise terms, having both been commonly referred to as lattens in the past. Today the term copper alloy tends to be substituted, especially by museums.
What is a metal alloy with copper as its principal component?
Example of a copper alloy object: a Neo- Sumerian "Foundation Nail" of Gudea, circa 2100 BC, made in the lost-wax cast method, overall: 17.5 x 4.5 x 7.3 cm, probably from modern-day Iraq, now in the Cleveland Museum of Art ( Cleveland, Ohio, USA) Copper alloys are metal alloys ...
How many different types of copper are there?
There are as many as 400 different copper and copper alloy compositions loosely grouped into the categories: copper, high copper alloy, brasses, bronzes, copper nickels, copper–nickel–zinc (nickel silver), leaded copper, and special alloys. The following table lists the principal alloying element for four of the more common types used in modern industry, along with the name for each type. Historical types, such as those that characterize the Bronze Age, are vaguer as the mixtures were generally variable.
What is the content of aluminium?
The content of aluminium ranges mostly between 5% and 11%. Iron, nickel, manganese and silicon are sometimes added. They have higher strength and corrosion resistance than other bronzes, especially in marine environment, and have low reactivity to sulphur compounds.
What metals are used in copper?
Copper is often alloyed with precious metals like gold (Au) and silver (Ag).
What is brass made of?
A brass is an alloy of copper with zinc. Brasses are usually yellow in colour. The zinc content can vary between few % to about 40%; as long as it is kept under 15%, it does not markedly decrease corrosion resistance of copper.
What are the elements that make up an alloy?
The typical alloying elements are copper, magnesium, manganese, silicon, tin and zinc. There are two principal classifications, namely casting alloys and wrought alloys, both of which are further subdivided into the categories heat-treatable and non-heat-treatable. About 85% of aluminium is used for wrought products, for example rolled plate, ...
What is the most important cast aluminum alloy?
The most important cast aluminium alloy system is Al–Si, where the high levels of silicon (4.0–13%) contribute to give good casting characteristics. Aluminium alloys are widely used in engineering structures and components where light weight or corrosion resistance is required.
Why are aluminium cylinder heads used?
Aluminium alloys are widely used in automotive engines, particularly in cylinder blocks and crankcases due to the weight savings that are possible. Since aluminium alloys are susceptible to warping at elevated temperatures, the cooling system of such engines is critical. Manufacturing techniques and metallurgical advancements have also been instrumental for the successful application in automotive engines. In the 1960s, the aluminium cylinder heads of the Corvair earned a reputation for failure and stripping of threads, which is not seen in current aluminium cylinder heads.
What is an alloy bicycle frame?
Welded aluminium alloy bicycle frame, made in the 1990s. Aluminium alloys (or aluminum alloys; see spelling differences) are alloys in which aluminium (Al) is the predominant metal. The typical alloying elements are copper, magnesium, manganese, silicon, tin and zinc.
How many digits are in wrought aluminium?
Wrought aluminium is identified with a four digit number which identifies the alloying elements. Cast aluminium alloys use a four to five digit number with a decimal point. The digit in the hundreds place indicates the alloying elements, while the digit after the decimal point indicates the form (cast shape or ingot).
What is aluminum used for?
About 85% of aluminium is used for wrought products, for example rolled plate, foils and extrusions. Cast aluminium alloys yield cost-effective products due to the low melting point, although they generally have lower tensile strengths than wrought alloys.
Why are bicycle frames made of aluminum?
For this reason, bicycle frames made of aluminium alloys make use of larger tube diameters than steel or titanium in order to yield the desired stiffness and strength. In automotive engineering, cars made of aluminium alloys employ space frames made of extruded profiles to ensure rigidity.
What is aluminum copper?
Aluminum copper alloy is the earliest cast aluminum alloy used in the industry. Its main performance characteristics are high room temperature and high temperature mechanical properties, simple casting process, good cutting performance and excellent heat resistance. It is the basis for the development of high strength aluminum alloys ...
What is the melting point of aluminum?
The aluminum copper alloy is very hard and has a melting point of 640 ° C. It is generally composed of 97% aluminum and 3% copper. Similar to the chemical properties of aluminum metal. Light and tensile strength. It can replace expensive copper wire as wire.
Can copper alloys be treated?
There is severe intragranular segregation. Because of its low copper content, the alloy can be solution treated. After quenching and aging treatment, the mechanical properties can be greatly improved.
