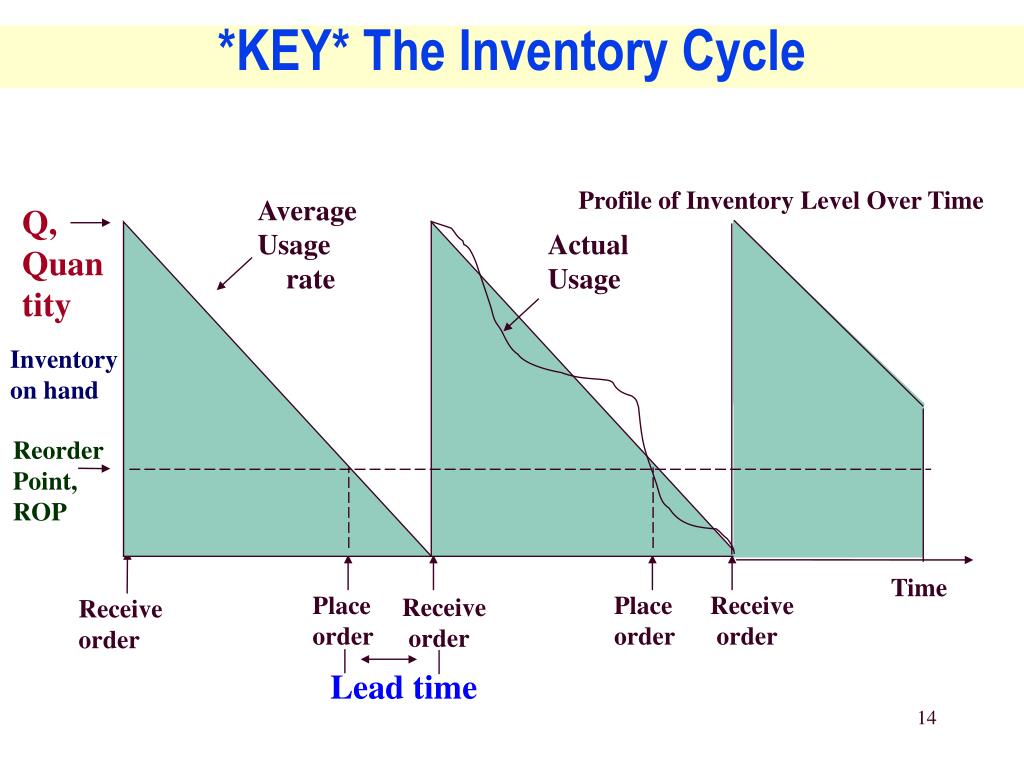
Stages Of Inventory
- Raw Materials "Raw materials" is the first stage of inventory. These are the materials that will make the final product and consist of the most basic goods such as wood, metal and water. ...
- Work-in-Process Once raw materials are pulled into the process of creating a final product, they enter the next stage of inventory, which is called "work-in-process." ...
- Finished Goods ...
- Cost of Goods Sold ...
What are the three types of inventory?
The three types of inventories are direct material inventory, work in progress inventory and the finished goods inventory where the direct material inventory includes the stock of raw material which the company has purchased for its use in production; work in progress inventory is the cost accumulated to the goods that are partially completed ...
What are the four stages of inventory in manufacturing?
Wholesale Vs. Inventory in manufacturing companies generally cycles through four distinct stages: raw materials, work-in-process, finished goods and the cost of goods sold.
What is inventory in business?
In other words, inventory represents finished goods or goods in different stages of production that a company keeps at its premises or at third-party locations with ownership interest retained until goods are sold. The three most important types of inventory are the raw materials, the work in progress (WIP) inventory, and the finished goods.
What is work in progress inventory?
Work in progress inventory can also be called semi-finished goods. They are the raw materials that have been taken out of the raw materials store and are now undergoing the process of their conversion into the final products. These are the partly processed raw materials lying on the production floor.

What are the 3 main components of inventory?
Inventory is the raw materials used to produce goods as well as the goods that are available for sale. It is classified as a current asset on a company's balance sheet. The three types of inventory include raw materials, work-in-progress, and finished goods.
What are the stages of inventory?
There are four stages of inventory: raw material, work in progress, finished goods, and goods for resale.
What are the 3 types of inventory management?
Financial Management.Order Management.Warehouse Management.Supply Chain Management.
What are the three types of inventory and why is each needed?
The three types of inventories are direct material inventory, work in progress inventory and the finished goods inventory where the direct material inventory includes the stock of raw material which the company has purchased for its use in production; work in progress inventory is the cost accumulated to the goods that ...
What is the first step of inventory management?
The first step in effective inventory management is to create an organised yet easy-to-implement system for inputting and tracking your stock as it is purchased, received, prepped and sold.
What are the 3 types of inventory and examples?
The three types of inventory most commonly used are: Raw Materials (raw material for making finished goods) Work-In-Progress (items in the process of making finished goods for sales) Finished Goods (available for selling to customers)
What is the inventory management process?
Inventory management is a technique of controlling, storing, and keeping track of your inventory items. Inventory management is an essential component of supply chain management, as it regulates all the operations that are involved from the moment an item enters your store until it has been dispatched.
What is inventory classification?
What is Inventory Classification? Inventory Classification, as the name says, is classifying the products in an inventory as per their demands, value, the revenue they bring in, carrying costs, etc.
What are the 5 types of inventory?
Depending on the business, inventory can include raw materials, component parts, work in progress, finished goods, or any packaging.Raw materials inventory. ... Maintenance, Repair, and Operating (MRO) inventory. ... Decoupling inventory. ... Work In Progress (WIP) inventory. ... Finished goods inventory.More items...•
What are the 5 steps to effective inventory system?
5 Steps to Successful Inventory ManagementCreate a System to Get Accurate and Accessible Information on Your Inventory. ... Create a Unique Process Customized for Your Business Type. ... Keep an eye on Contemporary trends in the industry. ... Be prepared for fluctuations in supply and demand.More items...•
What is inventory procedure?
Inventory control or management refers to the process or procedures of ordering, storing, and utilizing a company's inventory. These include the storage and processing of raw materials, components, and completed products, as well as the administration of raw materials, components, and finished products.
What is inventory process flow?
Inventory flow is the system of unique control methods that businesses use to regulate product activity within their operations. This process spans from manufacturers sourcing raw materials to retailers stocking finished goods.
What are the first three stages of inventory?
The first three stages of the inventory process are part of the balance sheet and are valued as company assets . Once the final product is sold, it is transferred from the balance sheet to the income statement and included in the cost of goods sold account.
What are the stages of inventory in manufacturing?
Inventory in manufacturing companies generally cycles through four distinct stages: raw materials, work-in-process, finished goods and the cost of goods sold. Unlike wholesale and retail companies, manufacturing companies must account for inventory before it is ready for sale along with all the costs associated with getting ...
What is the next stage of inventory?
Once raw materials are pulled into the process of creating a final product, they enter the next stage of inventory, which is called "work-in-process.". Work-in-process includes all products that are yet to be finalized. The costs associated with work-in-process inventory are the cost of raw materials, the cost of the labor used in production ...
What is finished goods?
At the completion of the manufacturing process, all costs associated with production, including raw materials and work-in-process costs, are transferred to the next stage of inventory: finished goods. Goods sit in the finished goods stage until they are sold.
What are the different types of inventory?
3 Types of Inventory are explained below: 1. Raw Materials Invent ory. Raw materials are the basic components that are used by the manufacturer to process or convert them into finished goods or subassemblies. These may be products or extracted minerals that the company or its sister concern has manufactured or extracted.
What are the three basic classifications of inventories?
Three basic classifications of inventories are as follows: Raw Material: This is basic goods procured which will be converted into finished goods; Work-In-Progress Type of inventory on which the production process is applied partially but is not wholly converted into finished goods at any particular point of time.
What is finished goods inventory?
Either organization itself has processed it into finished goods or it has procured from another company. Finished goods inventory also applies to traders who procure inventories from another organization and sale it further. Such person may does not need to classify its inventory as raw material, work in progress and finished goods as his products are itself finished goods only.
What is inventories in business?
Inventories can be defined as any asset or resource owned by an organization which is either purchased and hold for the purpose of selling or will be used in the production of finished goods which will be sold further or any raw material or consumable supplies which are used in manufacturing or providing services.
Why is inventory level important?
It is important for an organization to determine the level of finished goods it needs to hold and maintain based on its product’s demand. This inventory level determination helps an organization to further plan production level and related cost and funding part. EXAMPLE: – Manhattan Inc. a cloth manufacturing industry has incurred following cost in manufacturing 400 units of shirts. Shirts are completely worked upon and ready for sale.
What is work in progress?
Work in progress is inventory type which is described as partially finished goods or raw materials awaiting completion. Work in progress is a concept of production and supply chain management. Components included in this are labour, overhead cost, raw materials, a cost that are incurred during each stage of production. WIP is categorised under inventory asset account in the balance sheet. The cost of WIP are subsequently added together and then transferred to the finished goods account and thereafter to the cost of sales. It does not include further costs required for its completion.
What is finished goods?
Finished goods is the form of inventory on which complete manufacturing/ processing costs are incurred and the product is ready to be sold/ distributed. No further cost will be incurred in for converting this inventory. All direct indirect raw materials, labour cost, manufacturing, administration costs are applied on this. However, it may happen that organization needs to incur some selling cost like sales commission etc. Such cost does not forms part of inventory valuation.
What Are the Four Different Inventory Type?
There are four main types of inventory: raw materials/components, WIP, finished goods and MRO. However, some people recognize only three types of inventory, leaving out MRO.
What Is Inventory Process?
An inventory process tracks inventory as companies receive, store, manage, and withdraw or consume it as work in progress. Essentially, the inventory process is the lifecycle of goods and raw materials.
What Is Inventory?
Inventory is the accounting of items, component parts and raw materials a company uses in production, or sells. As a business leader, you practice inventory management in order to ensure that you have enough stock on-hand and to identify when there’s a shortage.
Why does accounting divide manufacturing stock into raw materials, WIP and finished goods?
Accounting divides manufacturing stock into raw materials, WIP and finished goods because each type of inventory bears a different cost. Raw materials typically cost less per unit than do finished items.
Why is inventory analysis important?
Improves Cash Flow: Inventory analysis helps you identify and reorder items you sell often, so you don’t spend money on inventory that moves slowly.
What is accounting for inventory?
Accounting for inventory is the system that counts and records changes in the value of stock. Raw materials, WIP and finished goods are all assets. Financial accounting for inventory provides an accurate valuation of those stock assets.
What is transit inventory?
Transit Inventory: An art store orders and pays for 40 tins of a popular pencil set. The tins are en route from the supplier and, therefore, in transit.
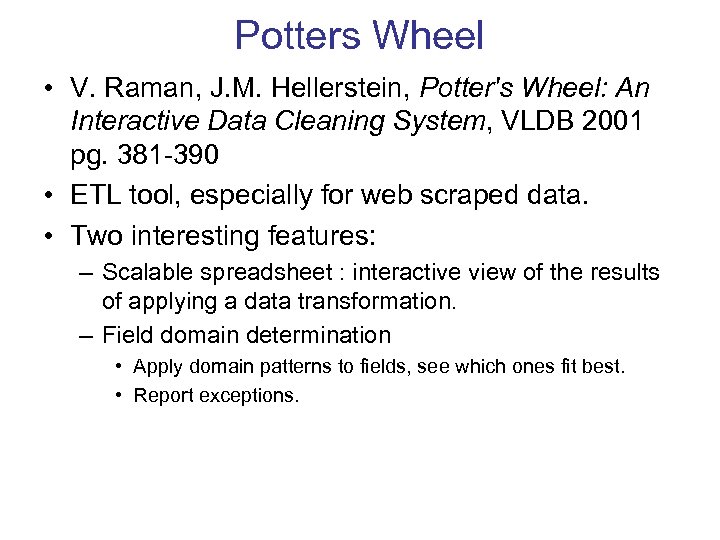