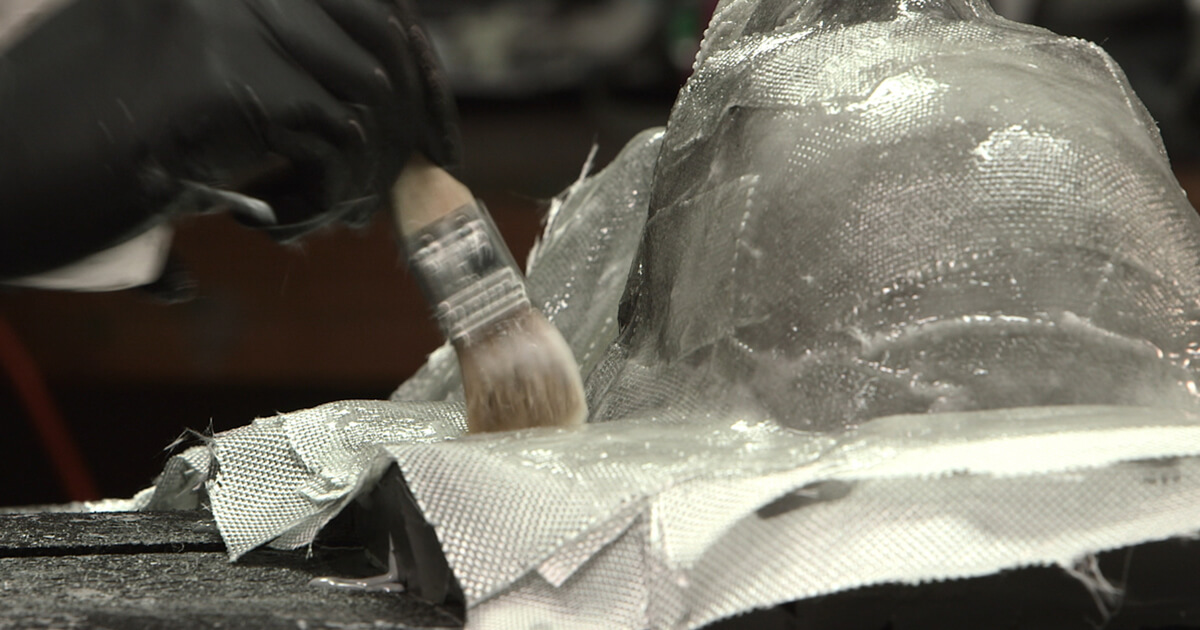
Preparation
- 1 Purchase a "fiberglass kit." A kit should contain the poly (polyester) resin, hardener (catalyst), and cloth for structural strength. ...
- 2 Think of a mold for your fiberglass. ...
- 3 Use foam or pliable materials for molds with organic shapes. ...
- 4 Use cardboard, plywood, MDF, or other stiff materials for molds with linear or geometric shapes. ...
Full Answer
How to separate molds from a mold?
How to increase strength of mold?
How to lay up a G3733 mold?
How to seal fuselage pattern?
How to make a fuselage hatch mold?
What is 105 resin?
What is 406 silica used for?
See 2 more
What can I use for fiberglass molds?
Materials used to make the Mold:West System 105A Epoxy Resin.West System 205A Epoxy Fast Hardener.West Systems 300 Epoxy Metering Pumps.West Systems 406 Colloial Silica Filler.West Systems A423 Graphite Powder.CST Style G3733 5.8 oz Fiberglass Cloth.Chavant Y2 Clay.Coremat Flexible Core.More items...
How do you make a Fibreglass mold?
The first step is to cut a pattern from blue insulation foam and wrap it with clear packing tape. Next, cover the taped pattern with a mold release wax. Now cover the pattern with woven fiberglass cloth and wet out the resin. Make sure to leave a section uncovered- this is where the foam will be melted.
What kind of wax do you use for fiberglass molds?
Paste wax is an economical mould release formulated with hydrocarbon and microcrystalline waxes. Paste wax, or run in wax is designed as a general purpose mould release agent on fiberglass and metal molds and as a compatible prime coat for PVA coatings.
How do you make fiberglass resin molds?
How to Make Fiberglass and Resin Molds at HomeClean frozen dinner tray and johnson paste wax. ... Applying paste wax to mold cavity. ... Waxed mold. ... Applying a coating of pigmented fiberglass resin to mold. ... Applying precut fiberglass cloth to mold cavity. ... Addition of remaining resin to fully wet fiberglass cloth.More items...•
What does fiberglass not stick to?
Even though it's used a lot, you might wonder, “will fiberglass resin stick?”. Fiberglass Resin will bond to almost any surface be it plastic, metal, wood, or Styrofoam. But there's a twist to it here; fiberglass resins don't usually stick to treated wood.
What is the best material to make a mold of for resin?
One of the best materials to use for molds is silicone, resin doesn't stick easily to silicone and it is very flexible, meaning that it is relatively easy to get your resin out of after it is fully cured. You can make your own silicone molds and there are lots of YouTube videos which show you how to do this.
Do I need special wax for fiberglass?
Over time, fiberglass/gelcoat finishes require regular cleaning and waxing because they become hazy, chalky, and uneven without it. What is this? The good thing about this type of finish is that you can use any form of RV, car, or marine wax on the bottom painted section of your RV.
What type of wax is best for molds?
Paraffin wax is one of the inexpensive and best candle wax for silicone molds. It is broadly used by candle-making brands due to its natural fragrance and unique color. It is also used in various candle-making types from container to pillar types due to its different melting point suitability.
Should you wax fiberglass?
Protect your Fiberglass RV from irreparable damage by washing it once a month to prevent buildup. Choose a cleaner with a wax additive to help with a clean finish and makes dirt harder to settle. It is prudent to have your RV waxed, with liquid or paste wax, at least once a year to maintain the gloss.
How do you make a poor man's fiberglass?
0:2818:12Is just simple drop cloth got this from harbor freight tools and tight bond to glue essentially allMoreIs just simple drop cloth got this from harbor freight tools and tight bond to glue essentially all you do to make this fiberglass.
What can I use instead of resin for molds?
Resin Alternative NamesFimo.Clay.Slush Latex.Metal.Plastic.Concrete.Plaster.Alabaster.
What fabric can be used with fiberglass resin?
-Fiberglass cloth Fiberglass cloth, also known as fiberglass fabric, is low in weight and becomes strong when combined with resin. It works well for building composite parts, making molds and for fiberglass repairs.
How do you make a poor man's fiberglass?
0:2818:12Is just simple drop cloth got this from harbor freight tools and tight bond to glue essentially allMoreIs just simple drop cloth got this from harbor freight tools and tight bond to glue essentially all you do to make this fiberglass.
How thick should a fiberglass mold be?
In general, the mold should be slightly thicker than the product, say 1.25 to 1.5%. Second, it must be stiff.
What are fibreglass Moulds made of?
Traditionally, fibreglass products are produced by coating an open mould with gel coat. Layers of glass fibre are then built up with plastic resin being manually applied. The result is left to cure (i.e. for the resin to harden) before the mould can be reused.
What are fiberglass molds made of?
Fiberglass molding is a process in which fiberglass reinforced resin plastics are formed into useful shapes.
How to separate molds from a mold?
Carefully separate the mold halves, you may need to use a model knife into one corner working the blade between the molds and gently twisting. When a crack appears, slip a wedge (a mixing stick works great) into the space and run it around the mold to separate the halves.
How to increase strength of mold?
Now we will increase the strength of the mold by building up the thickness. An easy way to accomplish this is with a core material such as Coremat, Aeromat or chopped strand mat as oppose to many layers of fiberglass cloth. Cut the mat material into sizes and shapes to fit the mold. Apply this layer with epoxy as you did the fiberglass cloth and apply another layer of fiberglass cloth over the top of the core material creating a sandwich. As you can see, the core material is needed most around the edges of the mold and any large flat areas.
How to lay up a G3733 mold?
While the tooling gel coat is setting to a solid state, about 30 minutes, cut your fiberglass cloth. Use a coarse weave fiberglass cloth to lay up the mold. CST style G3733 wets out easily and builds up thickness more quickly than lighter materials. If the mold has a complex shape cut the fiberglass cloth on the bias so the fibers run on a diagonal. Strips 2 to 3 inches wide work well for complex shapes as the cloth will stretch and distort as needed to follow the surface.
How to seal fuselage pattern?
The small opening around the edges of the fuselage pattern must be sealed. This can be done by first mold releasing the pattern. Then place the fuselage pattern into the parting surface with half the pattern exposed. Fill the opening around the edge with a mixture of West Systems Epoxy and 406 filler. After the epoxy has cured remove the pattern from the parting surface and block sand the parting surface flat along the edges. After you have the edge gaps filled build up the areas where openings in the mold are needed with clay. These openings give you access to the inside of the mold so you can join the half's of the molded part together. I have built up the areas of the hatch opening and tail boom connection opening. It is important to apply both Partall mold release wax and Coverall liquid mold release to the fuselage pattern and the parting surface as you did in step 1.
How to make a fuselage hatch mold?
To make the mold for the fuselage hatch, apply a tooling coat layer of epoxy to the pattern in the area where the hatch will be located . Tooling coat is made by mixing a batch of West Systems 105/205 Epoxy add a teaspoon of graphite powder to the mixture then stir in 406 filler to thicken the mixture to the viscosity of ketchup. Make the mold a little larger than the intended hatch size. Allow the tooling coat to cure to a soft solid; this should take about 30 minutes. Apply two layers of fiberglass cloth and epoxy over the tooling coat layer. On this small mold for the hatch, this lay up should be sufficiently strong.
What is 105 resin?
105 Resin is a low viscosity resin that easily wets out the cloth and allows for minimal air bubbles between the cloth layers.
What is 406 silica used for?
406 Colloidal Silica is used to thicken the epoxy system to aid in applying epoxy to vertical surfaces, filling corners and details in the mold.
How to avoid warping in fiberglass mold?
In laying up a fiberglass mold, warping can be avoided by allowing each layer to “kick” or gel before proceeding with the next layer. For a large mold, it is good to apply just one layer per day. After the “skin coat,” you can use 1½ oz. fiberglass mat for a faster build-up. Generally, woven roving is not used in molds because the pattern transfers through the mold to the gelcoat. If it is necessary to use woven roving fiberglass for strength in a large mold, it is applied after a thickness of 3 or 4 layers of mat has cured hard. The thickness required in a mold depends upon size and shape and the number of parts to be taken off. For a dinghy mold to be used only a few times, four layers of mat might be adequate.
How to prevent mold from sticking to plug?
To prevent your mold from sticking to the plug, the plug must be coated with plastic film known as “ PVA. ” This is a plastic dissolved in alcohol and has a green color. It can be brushed or sprayed on, but the best system is to spray on three thin coats, the first being a “mist coat.” The appearance will then be green. Each coat must dry half an hour or so and there must be no pools or drips to blemish your mold surface. For the easiest possible parting, before applying the PVA, apply a soft wax ( TR Mold Release) formulated for use with PVA. After the third coat of PVA has dried, a coating of this wax can be gently applied over it for easy parting.
How long does it take for a gelcoat to cure?
When the gelcoat has cured so that it cannot be scratched off with the fingernail at the edge of the mold, which takes from 2 to 4 hours to overnight in cool or humid weather, you are ready for the “skin coat.”.
How to remove mold from a plug?
The first step is to trim the excess laminate back to the molded edge. This is easily done with a saber saw and a metal-cutting blade. The edges are sanded carefully until the line between the mold and plug is exposed.
What is the first step in applying a gelcoat?
The Mold. The first step is to apply a gelcoat which will be the mold surface. The gelcoat must be “exterior gelcoat ” (wax free). If many parts are to be taken off the mold, it is desirable to use a “tooling gelcoat” which is designed to give longer life in mold use. The gelcoat should be in contrasting color to the surface ...
How many coats of gelcoat do you need to apply?
This facilitates spraying up a uniform thickness of light colored gelcoat since the black will show through thin spots. If the gelcoat is to be brushed on, two coats must be applied, and the first coat must cure several hours before the second coat is applied.
What is the best way to seal a plug?
If the plug contains soft materials on its surface such as plaster, wood, or putty, then it will have to be sealed with lacquer or resin to fill the pores. If plaster is used, it must be oven dried and then sealed.
How to make a mold out of plastic?
Step 1: Preparing the Mold. You have your clean plastic tray and some paste wax. Take a bit of wax with a rag and apply liberally to the cavity you wish to use. Allow to dry a few minutes while gathering other supplies or preparing a pigmented fiberglass resin.
How to make mold cloth white?
With a paint brush, you just tamp the cloth into place until all the surface of mold is covered. Once in place, take the remaining portion of catalyzed resin and liberally apply to the cloth to saturate it. The cloth will appear “white” where is has not been thoroughly saturated.
What to do after catalyzed resin is laid down?
After the first coating of catalyzed resin is laid down, it is time to lay down a precut piece of oversized fiberglass cloth.
Why is fiberglass laminating not recommended for thick section casting?
For this reason, fiberglass laminating resin is not recommended for thick section casting. The excess heat buildup in a thicker portion of resin liable to crack or cause other issues.
Can you get attached to improvised molds?
Also, it should be noted the life of these improvised molds will be limited so don’t get to attached to any of them.
Can you make resin molds at home?
How to Make Resin Molds at Home. Fiberglass and casting resins are a rewarding creative medium, but they can be costly to use. This is especially true when you purchase specialized mold-making materials like silicone resin. Often these cost at least twice or more than the resin being used—not to mention that silicone is liable to tear ...
How to apply epoxy to fiberglass?
Begin by applying a layer of fiberglass cloth, using 3M #77 spray before applying the epoxy. Apply the cloth in about 3” overlapping strips to ease the placement. You can mix your epoxy by using the manufacturer’s directions as a guide. Step 5: Apply the amount of layers of fibreglass cloth you need to get the desired rigidity and allow ...
How to make a mold out of foam?
Step 1: Carve out a big chunk of the foam to match the design, and then cut out the sides using a carpet or kitchen knife. Rough cut the sides with the knife to complete the shape according to your dimensions and sand or otherwise smooth out the foam to achieve the perfect shape. This step shouldn’t take you too long, especially if the mold you’re creating is for a straightforward shape.
How to remove foam from a fuselage?
Removal of foam. Step 1: Remove the foam after you’re done with the sanding as it provides a strong base to apply pressure. You can use acetone or any other suitable chemical to remove the solvent, which will pour out freely once you open an area of the fuselage.
What to do with lost foam?
Basically, with the lost foam technique, all you have to do is to dissolve a part of the foam to maintain rigidity, leaving you with the remaining part of the foam when the piece is done. To clarify, what you do is; carve the foam into the desired shape, cover the carved foam with layers of epoxy and fiberglass, and then discard the foam.
How to smooth out a cast iron?
Once the cast has been finished by sanding it, spray with Kylon primer or a similar product of your desired color. After painting or in between coats, be sure to continuously wet sand the surface until you achieve the desired smoothness.
How to increase accuracy of fiberglass?
Quick tip: In order to increase accuracy, you can make use of cardboard templates or a 3D printed to-scale miniature of your end part, and remember that fiberglass is a lot weaker on sharp corners. Therefore, consider adding more layers of fibreglass cloth to reinforce the corners and help you sand all the corners when you’re finishing the part without weakening it.
Can you make a hollow composite wing?
This method is commonly used for nacelles and fuse glass but you can also create a hollow composite wing with this technique. Below are the steps involved in making a foam mold for fibreglass.
How to make molds?
This white paper will describe the steps necessary to create accurate, high-quality, low-distortion molds for producing composite parts, including: 1 Plug Preparation 2 Types of Molds 3 Materials 4 Mold Construction Steps 5 Releasing the Mold 6 Prepping the Mold for Use
What is a fiberglass plug?
The fiberglass mold-making process begins with an object known as the plug. The plug is an exact representation of the object to be fabricated. One of the primary keys to success in mold construction is proper preparation of the plug. Any imperfections in the plug surface will be transferred to the mold, and then to future parts made from that mold. The plug needs to have a finish AT LEAST as good as the parts you wish to produce.
Why are female molds better than male molds?
Female (or cavity) molds are generally more costly, but they offer numerous advantages for medium to large production runs and for applications that require a cosmetically perfect finish. Finishing time is significantly reduced because every part emerges with a smooth outer surface. Female molds also lend themselves to use with core materials because the outer skin is always smooth regardless of how inconsistently the core is used inside the part. Either type of mold can be used for vacuum bagging, but female molds are usually easier to seal while achieving good surface characteristics. If more than 5-10 parts which need a smooth finish are being produced, female molds are worth the extra effort.
How are compression molds made?
Compression molds are sometimes made by using both a male and a female form . These "matched" molds are excellent for producing precision parts. The molds are loaded with reinforcement and resin before they are closed and tightened. Excess resin is squeezed out, voids are reduced, and parts emerge smooth and finished on both sides. Compression molds can also be modified for use with resin infusion or injection. The key is to think about the intended use of the finished part and what type of mold will be necessary to build it. If this is considered in advance, there is no limit to the type of parts that can be produced.
What are the advantages of composite molds?
Another advantage of composite molds is cost. It's far less expensive to fabricate and maintain a composite mold than to purchase a mold made of aluminum or steel.
How to apply parting wax to mold?
Use a clean dry cloth or applicator pad to apply a thin even coat of Parting Wax to mold surface.
How thick should a mold be before you start building?
Before beginning the construction of any mold, take the time to consider the desired end results. Plan to fabricate your mold at least 5 times thicker than the parts you wish to pull from it. This will prevent warping and possible damage to your mold during the de-molding process.
What type of foil do they use for fiberglass molds?
They used Aluminum Foil, like we use for cooking, as the facing for a fiberglass mold they needed. The piece they needed to duplicate was smoothed and sanded very well. Then they laid the foil in strips overlapping about 2 inches and sealed the seam with 2 inch masking tape.
What is used to separate gelcoat?
There are a number of Parting Agents or Mold Release materials that are painted onto the master, then the mat and resin applied over it. Often an air hose is used to separate the two pieces. This in particular goes for a gelcoat finish in almost all cases.
What Can I Use As A Mold Release
A mixture of 2 parts isopropyl alcohol and 1 part dish soap can be used in some cases to release silicone from silicone. Petroleum jelly can be used to release silicone from silicone, but it should be thinned with mineral spirits so that it can be applied in a thin layer with minimal visible brush strokes.
Recommendation: Partall Pva Release Agent
The PVA release lacquer from Partall is the ideal epoxy resin release agent for wood, silicone and other materials. It offers the user a whole range of advantages:
Recommendation: Orca Shimmer Mold Release Wax
The Orca Shimmer Release Wax can also be used for all types of resin. It offers the user many advantages:
Tips And Tricks For Easy Demolding Of Castings
There is no royal road to release a casting from the mold. The method of release depends strongly on the size of the mold used and the design of the component.
Internal Mold Release Agent
IMR is a product that is dissolved in the resin mix, which is highly soluble in the carrier solvent such as styrene. During cure the product drops out of solution and migrates to the surface due to volumetric shrinkage, pressure and temperature. When selecting an IMR agent the following criteria should be considered:
Advantages And Disadvantages Of Additive Use
Mold-release agent contained in polymethylmethacrylate molding-compound granules can separate as fine droplets at the rims of mold parts of the mold apparatus, for example, after several hours of continuous operation of the equipment. When the mold is opened, the droplets can then get onto either the female die or the blank itself.
Ptfe Dry Film Mold Release Agent
Miller-Stephensons PTFE / Fluorpolymer mold release agent solutions utilize low-molecular weight and particle size fluoropolymers to achieve ultra-uniform dry, thin films that exhibit excellent surface adhesion and durability.
How to separate molds from a mold?
Carefully separate the mold halves, you may need to use a model knife into one corner working the blade between the molds and gently twisting. When a crack appears, slip a wedge (a mixing stick works great) into the space and run it around the mold to separate the halves.
How to increase strength of mold?
Now we will increase the strength of the mold by building up the thickness. An easy way to accomplish this is with a core material such as Coremat, Aeromat or chopped strand mat as oppose to many layers of fiberglass cloth. Cut the mat material into sizes and shapes to fit the mold. Apply this layer with epoxy as you did the fiberglass cloth and apply another layer of fiberglass cloth over the top of the core material creating a sandwich. As you can see, the core material is needed most around the edges of the mold and any large flat areas.
How to lay up a G3733 mold?
While the tooling gel coat is setting to a solid state, about 30 minutes, cut your fiberglass cloth. Use a coarse weave fiberglass cloth to lay up the mold. CST style G3733 wets out easily and builds up thickness more quickly than lighter materials. If the mold has a complex shape cut the fiberglass cloth on the bias so the fibers run on a diagonal. Strips 2 to 3 inches wide work well for complex shapes as the cloth will stretch and distort as needed to follow the surface.
How to seal fuselage pattern?
The small opening around the edges of the fuselage pattern must be sealed. This can be done by first mold releasing the pattern. Then place the fuselage pattern into the parting surface with half the pattern exposed. Fill the opening around the edge with a mixture of West Systems Epoxy and 406 filler. After the epoxy has cured remove the pattern from the parting surface and block sand the parting surface flat along the edges. After you have the edge gaps filled build up the areas where openings in the mold are needed with clay. These openings give you access to the inside of the mold so you can join the half's of the molded part together. I have built up the areas of the hatch opening and tail boom connection opening. It is important to apply both Partall mold release wax and Coverall liquid mold release to the fuselage pattern and the parting surface as you did in step 1.
How to make a fuselage hatch mold?
To make the mold for the fuselage hatch, apply a tooling coat layer of epoxy to the pattern in the area where the hatch will be located . Tooling coat is made by mixing a batch of West Systems 105/205 Epoxy add a teaspoon of graphite powder to the mixture then stir in 406 filler to thicken the mixture to the viscosity of ketchup. Make the mold a little larger than the intended hatch size. Allow the tooling coat to cure to a soft solid; this should take about 30 minutes. Apply two layers of fiberglass cloth and epoxy over the tooling coat layer. On this small mold for the hatch, this lay up should be sufficiently strong.
What is 105 resin?
105 Resin is a low viscosity resin that easily wets out the cloth and allows for minimal air bubbles between the cloth layers.
What is 406 silica used for?
406 Colloidal Silica is used to thicken the epoxy system to aid in applying epoxy to vertical surfaces, filling corners and details in the mold.
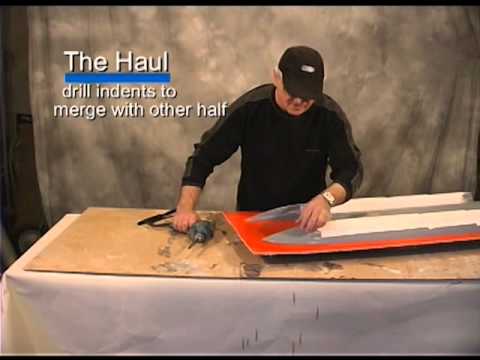