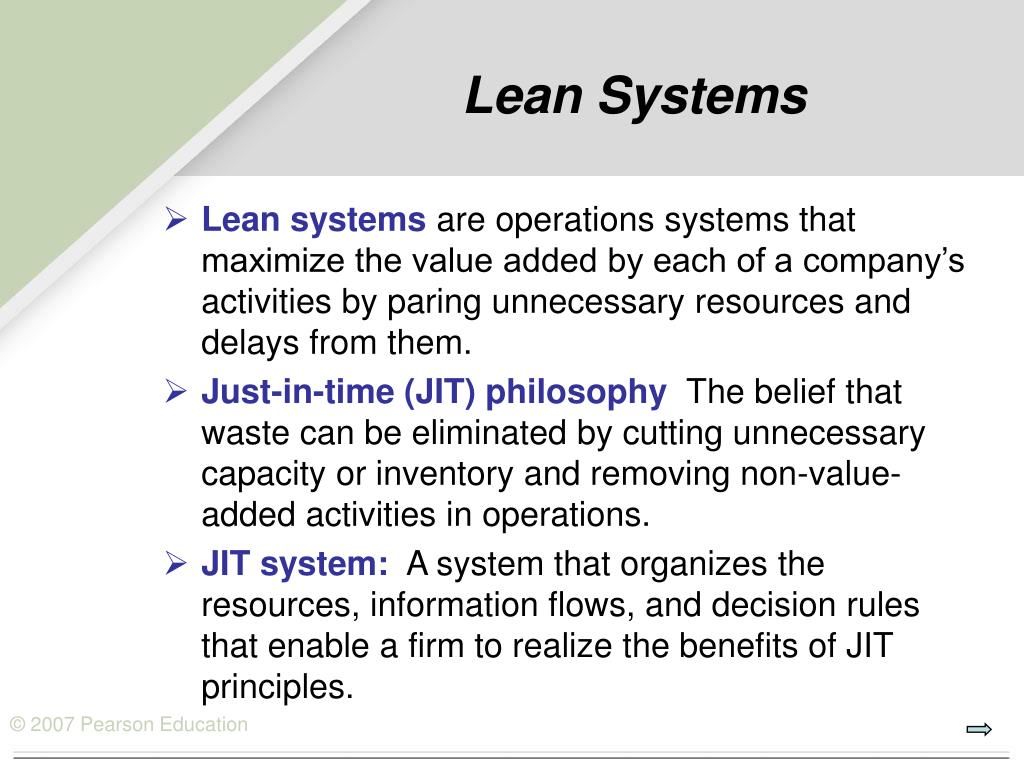
Essential Principles for a Lean System
- Lean System: Definition. A Lean system describes a business or business unit that holistically applies Lean principles to the way it plans, prioritizes, manages, and measures work.
- Guiding Principles of a Lean System. ...
- Benefits of a Lean System. ...
Full Answer
What is the ultimate goal of a lean system?
what are the goals of lean systems? -The ultimate goal is a balanced system, that is, one that achieves a smooth, rapid flow of materials and/or work through the system. The idea is to make the process time as short as possible by using resources in the best possible way.
What are the main benefits of a lean system?
The main benefits of Lean systems are:
- Reduced inventory: Lean system aims at holding minimum or no inventory. This in turn, leads to reduced space requirements and carrying/ holding cost.
- High quality: Problem solving techniques used in lean systems ensure that quality of the products/ goods are maintained.
- Reduced lead times: Delays are reduced which will lead to quicker response time. ...
What is lean and how dangerous is it?
Sleep Apnea overwhelmingly affects African Americans. This dangerous disease along with any type of drug, especially Lean, is a dangerous combination. The drink is called Lean because of the loss of control over your body. People affected by Lean tend to lean or slump over.
What are the basic concepts of lean?
The Seven Lean Principles
- Optimize the whole. Every business represents a value stream, the sequence of activities required to design, produce, and deliver a product or service to customers.
- Eliminate waste. ...
- Build quality in. ...
- Deliver fast. ...
- Create knowledge. ...
- Defer commitment. ...
- Respect people. ...

What do we mean by lean system?
Lean System: Definition A Lean system describes a business or business unit that holistically applies Lean principles to the way it plans, prioritizes, manages, and measures work. The goal for any Lean system is to maximize customer value.
What is a lean management system?
Lean management is an approach to managing an organization that supports the concept of continuous improvement, a long-term approach to work that systematically seeks to achieve small, incremental changes in processes in order to improve efficiency and quality.
What are the 5 principles of lean?
According to Womack and Jones, there are five key lean principles: value, value stream, flow, pull, and perfection.
What are the three basic principles of lean systems?
Lean Basics The Lean approach to business processes, originally derived from the enormously influential Toyota production system (TPS) , is based on three fundamental principles: delivering value as defined by the customer, eliminating waste, and continuous improvement.
What are 3 examples of lean manufacturing?
7 Examples of Lean Manufacturing in ActionCable Manufacturing. A cable manufacturing company wanted to reduce set-up times and shorten lead time to market. ... Truck Manufacturing. ... Printing Industry. ... Automotive Parts Manufacturing. ... Warehouse Management. ... Customer Service. ... Heating and Air-Conditioning Manufacturing.
What are the 7 wastes of lean?
The 7 Wastes of Lean ProductionOverproduction. Overproduction is the most obvious form of manufacturing waste. ... Inventory. This is the waste that is associated with unprocessed inventory. ... Defects. ... Motion. ... Over-processing. ... Waiting. ... Transportation. ... Additional forms of waste.More items...•
Why are lean systems important?
Lean manufacturing improves efficiency, reduces waste, and increases productivity. The benefits, therefore, are manifold: Increased product quality: Improved efficiency frees up employees and resources for innovation and quality control that would have previously been wasted.
What is the ultimate goal of a lean system?
the ultimate goal of a lean system is to achieve a balanced smooth flow of operations. supporting goals include eliminating disruptions to the system making the system flexible, and eliminating waste.
What are the characteristics of lean system?
Every Lean organization is unique, but there are some core qualities that they tend to have in common.Focused. Lean organizations are obsessed with customer value. ... Aligned. ... Humble. ... Collaborative. ... Tenacious. ... Engaged. ... Methodological. ... Proactive.More items...•
What are the benefits of the lean management system?
Lean manufacturing improves efficiency, reduces waste, and increases productivity. The benefits, therefore, are manifold: Increased product quality: Improved efficiency frees up employees and resources for innovation and quality control that would have previously been wasted.
What is the focus of lean management?
Used originally by manufacturing organizations, Lean is a performance-based, continuous-improvement strategy that focuses on eliminating waste and unnecessary steps in company processes.
What is the difference between lean and Agile?
The difference is that in Lean thinking, teams increase speed by managing flow (usually by limiting work-in-process), whereas in Agile, teams emphasize small batch sizes to deliver quickly (often in sprints).
What is lean enterprise?
A lean enterprise is organized to keep understanding the customer and their context, i.e., specifying value and looking for better ways to provide it:
What is lean thinking?
Lean thinking has a moral compass: respect for the humanity of customers, employees, suppliers, investors, and our communities with the belief that all can and will be better off through lean practices. Lean is not dogmatic. It’s not a rigid, unchanging set of beliefs and methods. Instead, it progresses in the context of specific situations. There is no endpoint as long as value is imperfectly created, and waste exists. Learn about the brief history of lean thinking and practice.
How can lean thinking help you?
From executive coaching in strategy development, deployment, and alignment to engaging employees to create a culture of problem-solving and everything in between , see how lean thinking and practice can elevate your organization’s performance.
What is lean manufacturing?
Lean manufacturing, or lean production, is a system of techniques and activities for running a manufacturing or service operation. The techniques and activities differ according to the application at hand but they have the same underlying principle: the elimination of all non-value-adding activities and waste from the business.
What is lean management?
Lean is defined as a set of management practices to improve efficiency and effectiveness by eliminating waste. The core principle of lean is to reduce and eliminate non-value adding activities and waste.
What are the Seven Types of Waste (Muda) in Lean Manufacturing?
Waste, or muda in Japanese, is defined as the performance of unnecessary work as a result of errors, poor organization, or communication.
How many wastes of lean are there?
Quality professionals often debate whether or not there are seven or eight wastes of lean. The eighth waste of lean is unique from the original seven because its elimination can directly benefit the employees, as well as the employer. The eight lean manufacturing mudas can be remembered using the acronym DOWNTIME. D efects.
What is lean towards green?
Leaning Toward Green ( Quality Progress) Lean practitioners have for many years called attention to the conventional seven deadly wastes in actions taken to transform raw material into a finished product. However, if they would use a broader perspective to include material and energy sources used to create the product, more waste and cost savings could be realized.
What is lean Six Sigma?
George, Sr., CEO of AI Technologies, using practical manufacturing examples and a case study, explains what artificial intelligence is , why it’s important for analyzing big data and shedding light on dark data, and how it can be applied to your lean Six Sigma and continuous improvement efforts to give you a substantial competitive advantage.
What is a lean initiative?
Establishing a Lean Initiative ( Journal for Quality and Participation) Organizations of all types have embraced lean practices and are developing their own programs for fostering education, training, and application of the associated concepts and methods.
What is a lean system?
Lean System: Definition. A Lean system describes a business or business unit that holistically applies Lean principles to the way it plans, prioritizes, manages, and measures work. The goal for any Lean system is to maximize customer value. While Lean thinking can greatly improve the productivity and function of a team or department, ...
What is the purpose of lean systems?
At its core, all successful Lean systems are rooted in one thing: Respect for people. Lean systems are designed to maximize customer value while minimizing waste, out of respect for the customer. Out of respect for employees, Lean systems encourage environments that allow everyone to do their best work.
What is Lean Thinking?
The new Lean is differentiated from other business methodologies in that it doesn’t prescribe a strict, rigid set of rules, tools, processes, or practices. Although transforming into a Lean system involves a great deal of effort, its lightweight, flexible nature makes it easy to scale than more structured, regimented methodologies.
What are the benefits of a lean system?
When an organization holistically applies these Lean principles, it is able to function in a healthier, smarter, more sustainable way. This directly results in business value. When the organization wins, the people within it win too.
What is lean mindset?
Lean is a mindset that helps you make smarter decisions about how to invest your time, energy, and money. The essential principles for a Lean system can provide businesses with the discipline and focus they need to satisfy their customers’ needs. Without the structure and guidance of Lean principles, it’s quite difficult to respond ...
What are the principles of lean management?
In order to maintain a competitive edge, businesses need the agility and focus to sustainably deliver value to their customers. A Lean system can provide businesses with the discipline and focus they need to satisfy their customers’ needs. Planview’s Portfolio Resource Management Solution.
How does lean organization work?
Lean organizations set themselves up for sustainable growth by building quality into processes and documentation. They automate and standardize any tedious, repeatable process or any process prone to human error , which allows them to error-proof significant portions of their value streams.
What is a system?
A system is officially a set of interacting or interdependent components forming an integrated whole through the relationships between the elements. What are the elements? What are the parts? A system is also an organized or established procedure to do something, such as a system to beat the roulette, or your system to handle your e-mails.
What is Toyota's production system?
A production system which is steeped in the philosophy of “the complete elimination of all waste ” imbuing all aspects of production in pursuit of the most efficient methods. Toyota Motor Corporation’s vehicle production system is a way of “making things” that is sometimes referred to as a “lean manufacturing system” or a “just-in-time ( JIT) system,” and has come to be well known and studied worldwide. This production control system has been established based on many years of continuous improvements, with the objective of “making the vehicles ordered by customers in the quickest and most efficient way, in order to deliver the vehicles as quickly as possible.”
What are the seven classic labor wastes?
As he describes in his books he hit upon the labor saving potential of working at takt time and producing according to kanban, hence the seven classic labor “wastes”, which are useless operations created by NOT being just in time: overproduction, inventory, overprocessing, motion, transportation, waiting, defects.
Why is confusion about systems understandable?
The confusion about systems is understandable because it is a case of emphasis more than nature. In both the Taylor/Ford and the Toyota systems we find a set of typical problems and typical solutions. The Taylor/Ford approach emphasizes the typical solutions – one should identify the best solutions and then standardize them across operations by using the “system” to teach these best practices to everybody.
What is Toyota's emphasis on?
Conversely, Toyota’s emphasis in on the typical problems – the system’s point is to teach everybody to recognize typical problems and to work out their own solutions to the problem, and so, develop a greater understanding of their work, with a side benefit of capturing more creativity and engagement.
Is lean a yin or yang?
It’s a yin and yang thing – none of the above are mutually exclusive and, indeed, an ideal lean system would have some aspects of the three. However, beware of taking any one of these meanings to extremes, dismissing the other two – that is a well known way of getting into trouble.
Is there one single answer to "lean concepts"?
Good question and not easy to answer as, as with many lean concepts, there is not one single answer and much depends of the perspective of the person answering. For instance, an executive vice president of Ford describes the Ford Production System as how Ford operates within all of its manufacturing facilities throughout the world:
What is the first step in lean systems thinking?
The first step in the lean systems thinking is driving out waste so that all work adds value and serves the customers' needs. There is a need to evaluate value-added and non-value-added steps in every process as to achieve this purpose.
How does lean thinking help in healthcare?
In healthcare, lean thinking is applied in providing value to a patient and by eliminating delays, overcrowding, and the frustration associated with the healthcare delivery system. It creates an avenue where what's supposed to be done is done. Clinicians who apply lean thinking reduce wasted time and spend more time delivering quality patient care. With lean thinking, a patient's journey can be planned to be safer by eliminating all kinds of waste and treating more patients with existing resources.
What is learning organization?
According to him, the learning organizations are the ones where people nurture their thinking ability to create outstanding results. Such organizations adapt quickly to customer needs and are able to excel in their fields. According to Senge, systems thinking focuses on how an individual interacts with the system.
What is the next step after removing waste from the value stream?
After removing the waste from the value stream, the next step is to smoothen the process flow towards the customer. This will ensure the flow is free from any delays or interruptions. It improves the time to market to the customer.
Why do public companies undergo routine restructuring?
Large public companies undergo routine restructuring on a regular basis with the primary goal of achieving better economic output and demonstrating superiority in the industry. However, this restructuring doesn't stabilize the working environment as the employees try to meet up with new goals. Different sectors of the company often pursue the achievement of goals individually, creating a gap between the sectors. With lean system thinking, an effective bridge is built between the various sectors to create an atmosphere of employee alignment and commitment to challenging business conditions; the result is increased output.
What is systems thinking?
According to Senge, systems thinking focuses on how an individual interacts with the system. It does not focus on the individual in an organization, but rather it focuses on the individual's interaction within the organization. Having different points of view from different people about a system allows new ideas to remove waste from the system. He insisted on having a collective intelligence approach to work differently.
Who said systems thinking should be focused on individual's interaction within the organization?
Peter Senge , an American scientist, says that systems thinking should be focused on individual's interaction within the organization, rather than concentrating on just an individual. Lean systems thinking can help in achieving goals and actions by following key principles, which include the following:
What is a Lean Daily Management System?
Defined, Lean Daily Management is a system that allows us to know on a daily basis whether we are on track or off track to meeting our goals, to take corrective action, and to check that past actions and improvements are being sustained.
What Are the Essential Components of a Lean Daily Management System?
There are four essential routines in a Lean Daily Management System. The four routines are Daily Accountability Process, Leader Standard Work, Gemba Walks, and Process Confirmation.
Why is lean management important?
The Lean Daily Management System gives us the structure and routine to practice and get better at this each day.
What are the prerequisites for a system?
They include team size and span of control for team leaders, KPIs (Key Performance Indicators), standard work, visual controls, an escalation system, competence with practical problem solving, and coaching.
What is leader standard work?
Leader Standard Work is the routine for leaders at all levels to check on their teams, the status of progress on the day’s work, confirm that process standards are being followed, and find opportunities to coach and develop people.
Do you need to be perfect to start Lean Daily Management?
The effort needed to establish these routines and prerequisites will be different for each organization. We don’t need to be perfect at all of them before starting with Lean Daily Management. However, ignoring the need for one or more of these enablers is a sure way to weaken or even sabotage our efforts.
What is lean methodology?
From a business point of view, Lean's is to shorten product development cycles and rapidly discover if a given business concept is viable. This methodology is also employed by government structures, marketing professionals, and others.
What is Lean Management, and How Did It Start?
Before you start with the basic Lean principles, you need to realize that the Lean methodology is about continuously improving work processes, purposes, and people.
What is the book Lean Software Development?
The book describes how you can apply the initial principles of the Lean methodology to software development. At the end of the day, Lean software development comes down to 7 principles.
What are the benefits of lean management?
Benefits of Lean Management 1 Focus. By applying the Lean methodology, you will be able to reduce waste activities. Therefore, your workforce will be focused on activities that bring value. 2 Improving productivity & efficiency. When employees are focused on delivering value, they will be more productive and efficient because they won’t be distracted by unclear tasks. 3 Smarter process (pull system). By establishing a pull system, you will able to deliver work only if there is actual demand. This leads to the next one. 4 Better use of resources. When your production is based on actual demand, you will be able to use only as many resources as needed.
What is the Lean Principle of Value Stream Mapping?
Applying the Lean principle of value stream mapping will show you where value is being generated and in what proportion different parts of the process do or do not produce value.
Why is lean practice so popular?
The growing popularity of the Lean principles comes from the fact that they actually focus on improving every aspect of a work process and involve all levels of a company’s hierarchy.
How many principles does Lean Management have?
Thanks to this notable impact, Lean thinking has spread across many industries and evolved to 5 basic Lean management principles as described by the Lean Management Institute.
How to Practice Lean Manufacturing?
A prerequisite to successfully practicing the Lean manufacturing strategy is understanding its core principles. To practice Lean Manufacturing, you can follow the steps below.
What Are the Goals in Lean Manufacturing?
Among the most prominent objectives of the Lean manufacturing method is creating efficiency through continuously examining the current processes and improving. To achieve this, Lean has 4 different goals.
What Is the Toyota Production System (TPS)?
The Toyota Production System (TPS) or “The Toyota Way” is an operational model which emerged in the early 20th century in Japan as a management system for organizing manufacturing and logistics processes. The backbone of TPS is the just-in-time production (JIT) system, created by Mr. Taiichi Ohno (a Japanese industrial engineer and businessman).
What is the goal of lean management?
Another goal of this type of management is to maximize profits by increasing the value or products and processes. Lean management involves a lot of process examination, the addition of perspectives from various leaders in the organization, and mapping the processes that are adding to the company. It is essential that lean management processes are accompanied with structured plans that map out progress.
When did lean management start?
Henry Ford started on the path to efficiency and lean management with the Model T in the early 1920s. The assembly line and production processes were some of the first of their kind to implement continuous improvement.
How does lean management affect employees?
— Since lean management favors an approach where managers are in regular communication with employees about their work and their process, employees could feel they are empowered to make better decisions. — Workers know where they stand and where they can improve to create quality work. Part 3.
What is the most important group in lean management?
Vendors and suppliers are going to be one of the most critical groups in the implementation of lean management. Timely communication, deliveries, and responsiveness to unforeseen issues is key to this relationship. Therefore, there should be a staff member that is dedicated to supplier management and acts as a point of contact for this group.
What is considered waste in lean management?
Whatever is not included in the category of creating value for the company is considered waste. The goal is to develop processes that are working toward continued success. Those who believe in lean management also look at value and progress through the eye of the customer, who is respected as one of the most important stakeholders. ...
What is Six Sigma in management?
Six Sigma is a popular set of techniques and practices that address process improvements. Workers can benefit from learning these principles so they can further implement the methodology in the company. The more continuous improvement principles that employees are exposed to, the better.
Does Virginia Mason Medical Center use lean?
A National Institutes of Health study revealed results of the Virginia Mason Medical Center’s usage of comprehensive lean policies . The hospital noted increased profits, decreased deaths, an 85 percent decrease in the wait for lab results, and a 93 percent increase in productivity.
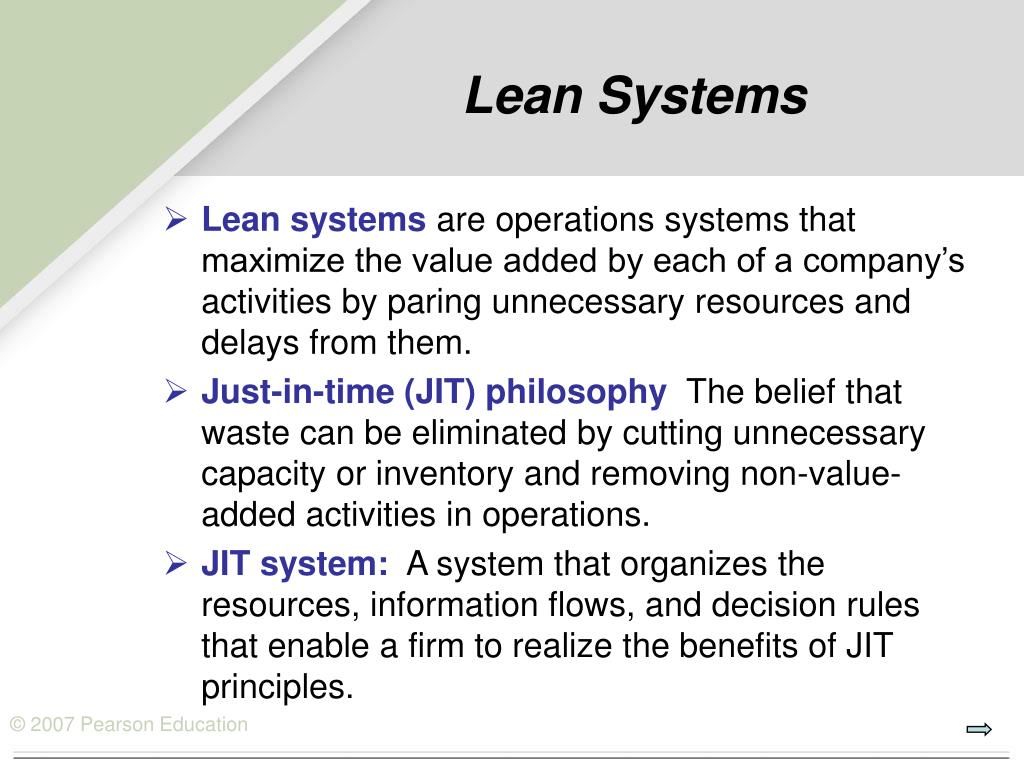