
What is continuous review system in construction?
continuous review system. an arrangement whereby a specified quantity of materials is reordered at variable intervals. In determining the interval between orders, account must be taken of the usage rate of STOCK during the interval between placing the order and delivery of the ordered material.
What is the difference between continuous review and Periodic Review?
The periodic review system check the concrete stock pile at a distinct intermission of time. This system will be economical to use compare to the continuous review system, however this system will require an above normal limit of safety stock to avoid ambiguity with demand during an extended schedule perspective.
What is the difference between continuous review and physical inventory?
The continuous review system requires knowing physical inventory all the times, like using a barcode scanner every time cashier scans product purchased by the customer to update inventory. This method is more expensive to administer because inventory needs to update each time something goes out of shelf or comes into the shelf.
What are the disadvantages of the continuous system of inventory management?
The disadvantage of the continuous system: The periodic review system, evaluate inventory at specific times like counting inventory at the end of each month. It is inexpensive to administer since counting takes place at a particular time, but a higher level of safety is required to buffer against uncertainty in demand over longer planning horizon.
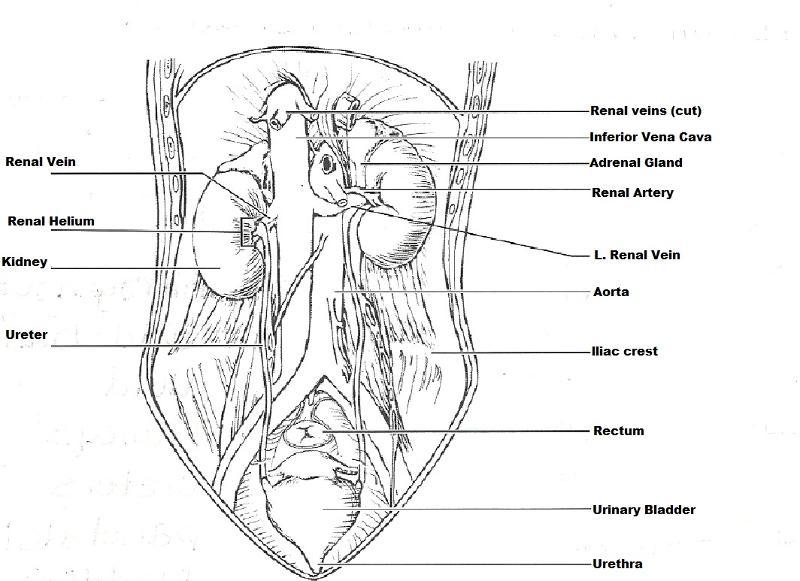
What is continuous and periodic review system?
The two review methods are periodic and continuous, or perpetual, inventory. Periodic inventory takes stock every week or month. Continuous inventory constantly tracks inventory quantities so you always know your stock levels.
What is advantage of continuous review system?
The advantage of the continuous review system: Provide real-time updates of inventory counts. Make easier to know when to order. Provide accurate accounting.
What is a periodic review system explain with an example?
This system also makes sense when you order several different items from a supplier. For example, if your company buys 10 different items from the same supplier, you can place one order for all 10 items rather than 10 individual orders, one for each item.
What is meant by period review system?
1. A classic inventory system where the inventory level is reviewed at a regular time intervals (e.g., once a week), whereupon the decision is made as to how much to order to bring the inventory level up to a given amount.
What are types of inventory?
There are four main types of inventory: raw materials/components, WIP, finished goods and MRO.
What is continuous review inventory policy?
This chapter deals with continuous review policies. This means that the inventory levels are followed continuously and that replenishments may be ordered at any time. If the demand is Poisson (or compound Poisson) it is easy to realize that it is sufficient to consider those moments of time when demands occur.
What is difference between perpetual and periodic inventory system?
The periodic inventory system uses an occasional physical count to measure the level of inventory and the cost of goods sold. The perpetual system keeps track of inventory balances continuously, with updates made automatically whenever a product is received or sold.
Is FIFO perpetual or periodic?
With perpetual FIFO, the first (or oldest) costs are the first removed from the Inventory account and debited to the Cost of Goods Sold account. Therefore, the perpetual FIFO cost flows and the periodic FIFO cost flows will result in the same cost of goods sold and the same cost of the ending inventory.
What is an example of periodic inventory system?
Example of Periodic Systems. Periodic system examples include accounting for beginning inventory and all purchases made during the period as credits. Companies do not record their unique sales during the period to debit but rather perform a physical count at the end and from this reconcile their accounts.
How is review period calculated?
9:4913:59Understanding Periodic Review System - YouTubeYouTubeStart of suggested clipEnd of suggested clipSo the first step is to select the time between the reviews whether it is once a week or you knowMoreSo the first step is to select the time between the reviews whether it is once a week or you know once in two weeks or three weeks in what month potentially one can use economic. Or in quantity.
What is two bin system in inventory?
Two-bin inventory control is a system used to determine when items or materials used in production should be replenished. When items in the first bin have been depleted, an order is placed to refill or replace them. The second bin is then supposed to have enough items to last until the order for the first bin arrives.
What is continuous inventory counting?
Continuous inventory counting is a regular check of physical quantities against records (and vice versa) that requires the business to have perpetual inventory records – it is an internal control procedure.
What are the advantages of periodic inventory system?
The advantages of the periodic inventory system are relatively cheap cost and simplicity. The disadvantages of periodic inventory systems are the slow process and less fidelity in inventory updating. This system is better suited for small businesses with fewer goods or slow-moving goods with less variety.
What are the disadvantages of continuous stock taking?
6 Main Disadvantages of Perpetual Inventory Systems#1. Loss of items. Using the perpetual inventory systems ensure fast and easy record keeping of various items in stock in any organization. ... #2. Breakages. ... #3. Theft. ... #4. Scanning errors. ... #5. Improper inventory tracking. ... #6. Hacking.
What are the advantages of perpetual inventory system over the periodic inventory system?
What is the advantage of a perpetual inventory system? A perpetual inventory system is more accurate than the less advanced periodic inventory system. Having a more accurate count of inventory at all times prevents stockouts and overstock issues.
What is the ABC inventory system?
ABC analysis is an inventory management technique that determines the value of inventory items based on their importance to the business. ABC ranks items on demand, cost and risk data, and inventory mangers group items into classes based on those criteria.
Why is continuous review more expensive?
This method is more expensive to administer because inventory needs to update each time something goes out of shelf or comes into the shelf. It requires a lower level of safety since there is only uncertainty during the delivery period is the magnitude of demand. Therefore, during that time, the only safety stock required is for potential stockouts. (Wisner, Tan, Leong, Stanley, 2012, p.90).
What is periodic review system?
The periodic review system, evaluate inventory at specific times like counting inventory at the end of each month. It is inexpensive to administer since counting takes place at a particular time, but a higher level of safety is required to buffer against uncertainty in demand over longer planning horizon. (Wisner et al., 2012, p.90).
When does inventory count not provide an accurate count?
It may not provide an accurate inventory count when there is a high volume of sale
What is continuous review?
The continuous review system entail that real supply is acknowledged in real time, so it will be costlier to implement than the periodic review system, but it will let you know that your physical inventory will match what is on your screen. The only concern with this system is that we are not sure of how many demand we will get during the “delivery lead time” (Wisner-Tan-Leong-Stanley, 2012, p. 90) period of those goods in order.
Why is continuous review more expensive?
This method is more expensive to administer because inventory needs to update each time something goes out of shelf or comes into the shelf. It requires a lower level of safety since there is only uncertainty during the delivery period is the magnitude of demand. Therefore, during that time, the only safety stock required is for potential stockouts. (Wisner, Tan, Leong, Stanley, 2012, p.90).
What is periodic review system?
The periodic review system, evaluate inventory at specific times like counting inventory at the end of each month. It is inexpensive to administer since counting takes place at a particular time, but a higher level of safety is required to buffer against uncertainty in demand over longer planning horizon. (Wisner et al., 2012, p.90).
What are the advantages and disadvantages of periodic review?
The advantage of the periodic review system: Allows the business owner having more time to run another aspect of the business. The disadvantage of the periodic review system: It may not provide an accurate inventory count when there is a high volume of sale.
ELEMENT OVERVIEW
Routinely reviewing the organization’s process safety systems to spur continuous improvement is one of four elements in the RBPS pillar of learning from experience. This chapter describes the meaning of management review, the attributes of a good management review system, and the steps an organization might take to implement management reviews.
What Is It?
Management review is the routine evaluation of whether management systems are performing as intended and producing the desired results as efficiently as possible. It is the ongoing “due diligence” review by management that fills the gap between day-to-day work activities and periodic formal audits.
Why Is It Important?
Effective performance is a critical aspect of any process safety program; however, a breakdown or inefficiency in a safety management system may not be immediately obvious. For example, if a facility’s training coordinator unexpectedly departed, required training activities might be disrupted.
Who Does It?
Strictly speaking, every level of management – from the process supervisor to the facility manager to the board of directors – should conduct periodic management reviews.
What Is the Anticipated Work Product?
The output of a management review is generally an internal memorandum summarizing the review, any deficiencies or inefficiencies noted, and recommendations for improvement or corrective action. The recommendations should be given deadlines and then assigned to specific individuals.
How Is It Done?
Management reviews are conducted with the same underlying intent as an audit – to evaluate the effectiveness of the implementation of an entire RBPS element or a particular element task.
