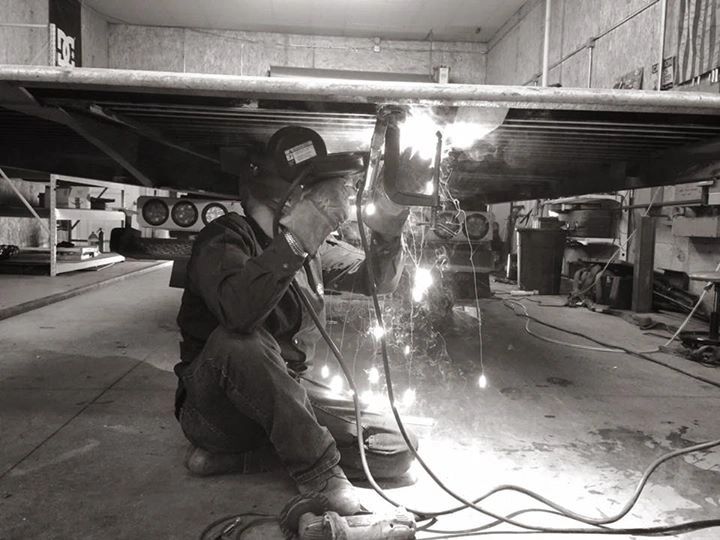
The followings are the applications of FCAW:
- This arc welding process is find important in shipbuilding industry as it save huge labour cost.
- It is also used in many construction industries in welding aspect.
- It is widely applicable in mechanical industries.
- FCAW can be used on plain carbon, alloy, stainless and duplex steels.
- It is used for hard facing and surfacing.
What is the difference between FCAW and GMAW?
GMAW applications are more forgiving. It is the easiest type of welding to learn, and the process is more forgiving for the robot, even if there is an erratic movement. FCAW tasks may have to be performed in a more precise nature, but the set-up is easier than GMAW because there is no external shielding gas or additional equipment to set up.
What are the 5 different types of welding?
What are the Different Welding Types and What are They Used for?
- Arc. This category includes a number of common manual, semi-automatic and automatic processes. ...
- Friction. Friction welding techniques join materials using mechanical friction. ...
- Electron Beam. This fusion joining process uses a beam of high velocity electrons to join materials. ...
- Laser. ...
- Resistance. ...
What is the difference between GMAW and MCAW welding?
MCAW is a variant of the MIG/MAG welding process. What is the difference between GMAW and MCAW welding?, DC – direct current, only GMAW generally uses DCEP – reverse polarity, electrode positive, heat is greater at the metal, deeper penetration. FCAW applications generally use DCEN – straight polarity.
What does FCAW stand for in Science category?
Flux-cored arc welding (FCAW or FCA) is a semi-automatic or automatic arc welding process. FCAW requires a continuously-fed consumable tubular electrode containing a flux and a constant-voltage or, less commonly, a constant-current welding power supply.
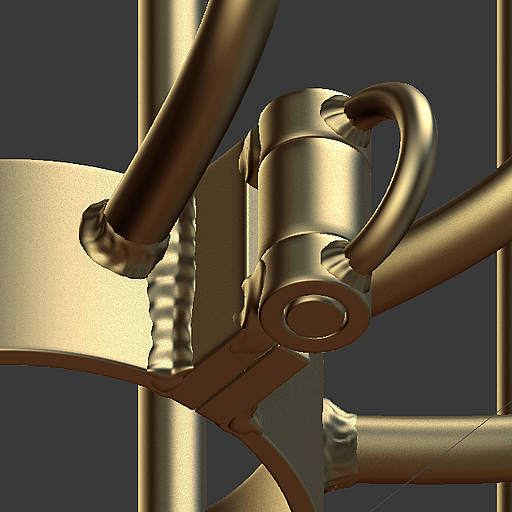
What is a flux core welder used for?
Flux core welding is used to weld thicker metals. It differs from flux core soldering and is ideal for heavy-duty or industrial applications since the finished bond is much more secure. This is essential when working on things like machine parts.
What can FCAW weld?
0:005:07What is Flux Cored Arc Welding? (FCAW) - YouTubeYouTubeStart of suggested clipEnd of suggested clipThis process flux cored arc welding or FC aw all flux core welding is done on equipment that isMoreThis process flux cored arc welding or FC aw all flux core welding is done on equipment that is similar to and sometimes identical to the equipment used in MIG or gas metal arc welding.
What type of welding is FCAW?
This is known informally as "dual shield" welding. This type of FCAW was developed primarily for welding structural steels. In fact, since it uses both a flux-cored electrode and an external shielding gas, one might say that it is a combination of gas metal (GMAW) and flux-cored arc welding (FCAW).
What is the main advantage of FCAW?
The Advantages of FCAW Yields high quality, consistent welds with fewer defects. A high deposition rate, which is the speed that the filler metal is applied. Can be used in all positions with the right filler metal. Suitable for outdoor welding or shop welding.
What is the difference between MIG and FCAW?
Just as the name states, a "Flux Core". The main difference between MIG welding and flux core arc welding is, FCAW gets its shielding from the flux core, and this allows the operator to weld outdoors where it is windy. It's like a SMAW welding electrode turned inside out!
Which is better FCAW or SMAW?
Unlike SMAW short-length electrode, FCAW employs very long electrode that is wound or wrapped in the form of a spool. Thus same electrode can be fed continuously into the welding zone for a longer duration without interrupting the process. This not only enhances productivity, but also discourages various defects.
What is difference between FCAW and GMAW?
GMAW (especially MIG) can be used for joining a wide variety of metals and alloys. FCAW is predominantly used for joining ferrous metals. It offers relatively lower penetration of the weld metal. It offers higher depth of penetration.
What are the two types of FCAW?
The FCAW process can be divided into two types depending on the shielding method; one that uses an external shielding gas and one that solely relies on the flux core itself for protecting the weld area.
Is flux-core welding strong?
While a MIG welder can deposit up to 8 pounds of wire per hour, a flux-core welder can deliver up to 25 pounds per hour.
What gas do you use for flux-core welding?
1:387:24Flux Cored Welding with Gas vs without Gas (FCAW-G vs FCAW-S)YouTubeStart of suggested clipEnd of suggested clipSo it because there's not much stuff in there to shield the weld hence. You need the de gasMoreSo it because there's not much stuff in there to shield the weld hence. You need the de gas shielding just like you do with me. Well what we're going to do is we're going to make a weld. Pay attention
Can you flux core weld brass?
You will need to use flux to promote the fusion of metals better when working with Brass. To do so, you will mix the flux with water to create a paste. Then you need to coat the brass surfaces that you are welding with the flux paste.
Can you convert a flux core welder to MIG?
0:0111:31Converting a Flux Core Welder to a Mig Gas Welder! - YouTubeYouTubeStart of suggested clipEnd of suggested clipAnd today I'll be showing you how I took this wire plus core welder and converted it into a gas MIGMoreAnd today I'll be showing you how I took this wire plus core welder and converted it into a gas MIG welder. Let's check it out ok. So click back story to this welder.
How Does Flux Core Arc Welding Work?
Flux cored arc welding uses heat generated by an electric arc to fuse metal in the weld joint area. This arc is struck between the metallic workpie...
Which Metals Can Be Welded with FCAW?
Flux cored arc welding works well with most carbon steels, cast iron, stainless steel and hard facing / surfacing alloys.However, nonferrous exotic...
What are the Advantages?
The flux core welding technique provides several advantages over other methods. FCAW is preferable to MAG welding for outdoor use as well as for jo...
What are the Disadvantages/Limitations?
There are few disadvantages of the process compared to other welding techniques, including production of noxious smoke that can make it difficult t...
What is FCAW Used For?
It is a flexible welding process suitable for all position welding, given the correct filler material and flux composition. Being highly productive...
What Is the Difference Between Flux-Cored Welding and Stick Welding?
Stick welding and flux-cored welding are extremely similar. Both use flux to protect the weld pool from contaminants. The difference is that with F...
What Is the Difference Between Flux-Cored Welding and MIG Welding?
The main difference between MIG welding and flux-cored welding is how the electrode gets sheltered from the air. FCAW receives shielding from the f...
Is Flux-Cored Welding as Strong as MIG Welding?
Flux-cored welding and MIG welding are considered to deliver the same weld strength.
What is FCAW welding?
FCAW utilizes the heat created by an electric arc to fuse the base metal in the weld joint region. It uses a hollow or tubular electrode filled with a flux compound (also called a flux-cored wire) that protects the weld pool by forming a gas.
Why is FCAW welding not fully automated?
Since the FCAW [process is not fully automated, there can be a lack of precision due to manual or mechanical errors. Working near toxic fumes or smoke can be hazardous, and hence, this type of welding must occur in an area that is well ventilated.
What is shielded metal arc welding?
Shielded Metal Arc Welding SMAW, also referred to as “stick welding,” is a welding technique used on all ferrous materials. The electrode coating helps de-oxidize the weld area. This generates a shielding gas that protects the weld area from atmospheric contamination.
What is an electrode in arc welding?
Electrodes are what differentiate flux-cored arc welding from MIG welding. While the latter uses solid wires as the filler material or filler metal, the former involves using electrode wires with a hollow flux-filled center. The electrode wires fill with flux, shielding the weld joint from corroding or contaminating due to natural elements.
What is filler wire core?
The filler wire core consists of agents that create shielding gases when the welding arc heat burns them.
When was flux cored arc welding invented?
First introduced in the 1950’s as an alternative to manual metal arc welding or stick welding, flux-cored arc welding has since become the preferred welding mechanism for various applications across industry segments.
What is the source of power for welding?
Source of power: The power source or welding machine provides the voltage and amperage supply that helps maintain the welding arc. Welding gun: This type of welding utilized both air-cooled and water-cooled guns. Air-cooled guns are easier to maneuver, but water-cooled guns offer a higher degree of efficiency.
What is the least common welding technique?
For instance the whip of the weld, doing circles, and weave techniques used for wider welds. When it comes to doing wider weave welds , it is the least common. Most flux core electrodes are typically designed for stringer beads.
How does flux core welding work?
Just like MIG welding, flux core welding works by feeding an electrode continuously to the joint. First the welder squeezes the trigger, and then the wire feeder begins to feed the electrode to the joint, at the same time the electrode gets electrically charged.
What causes worm holes in flux cored arc welding wire?
What causes these defects is improper storage of the electrode. The electrode picks up moisture inside the wire and when the welder starts welding it creates wormholes, porosity and worm tracks.
What is the classification code for flux core welding?
A somewhat common flux cored welding electrode is the "E71T – 1".
What size is a flux cored welding electrode?
Flux cored electrodes come in standard sizes. Some are the same size as most MIG welding electrodes but others are comparable to the thickness of a stick welding electrode. Here are some of the more popular sizes for standard industrial applications: .035.
What is flux cored arc welding?
Flux cored arc welding comes in two types of shielding. The first difference is in the electrode itself, it is a tubular wire with a shielding powder in the center. In technical terms this is called "Self-Shielding" or sometimes branded "Inner Shield".
What is MIG welding?
MIG welding gets its shielding from a bottle of gas which has serious drawbacks, when welding outdoors, or in drafty conditions. MIG power supply that can be used to weld FCAW wire. This is a Miller wire feed system that is used for outdoor flux cored arc welding in windy and rainy conditions.
What are the issues with FCAW welding?
Of course, all of the usual issues that occur in welding can occur in FCAW such as incomplete fusion between base metals, slag inclusion ( non-metallic inclusions ), and cracks in the welds. But there are a few concerns that come up with FCAW that are worth taking special note of: 1 Melted contact tip – when the contact tip actually contacts the base metal, fusing the two and melting the hole on the end. 2 Irregular wire feed – typically a mechanical problem. 3 Porosity – the gases (specifically those from the flux-core) don’t escape the welded area before the metal hardens, leaving holes in the welded metal. 4 More costly filler material/wire as compared to GMAW. 5 The amount of smoke generated can far exceed that of SMAW, GMAW, or GTAW. 6 Changing filler metals requires changing an entire spool. This can be slow and difficult as compared to changing filler metal for SMAW or GTAW. 7 Creates more fumes than SMAW.
When was FCAW first used?
The process is widely used in construction because of its high welding speed and portability. FCAW was first developed in the early 1950s as an alternative to shielded metal arc welding.
What is dual shield welding?
This is known informally as "dual shield" welding. This type of FCAW was developed primarily for welding structural steels. In fact, since it uses both a flux-cored electrode and an external shielding gas, one might say that it is a combination of gas metal ( GMAW) and flux-cored arc welding (FCAW). The most often used shielding gases are either ...
Why is flux used in welding?
An externally supplied shielding gas is sometimes used, but often the flux itself is relied upon to generate the necessary protection from the atmosphere, producing both gaseous protection and liquid slag protecting the weld. The process is widely used in construction because of its high welding speed and portability.
What are the disadvantages of welding?
Also, windy conditions need not be considered. Some disadvantages are that this process can produce excessive, noxious smoke (making it difficult to see the weld pool). As with all welding processes, the proper electrode must be chosen to obtain the required mechanical properties.
What is irregular wire feed?
Irregular wire feed – typically a mechanical problem. Porosity – the gases (specifically those from the flux-core) don’t escape the welded area before the metal hardens, leaving holes in the welded metal. More costly filler material/wire as compared to GMAW.
Can GMAW be used in windy conditions?
However, like GMAW, it cannot be used in a windy environment as the loss of the shielding gas from air flow will produce porosity in the weld.
Why is FCAW welding used?
This is because a flux compound within the wire protects the weld pool by forming a gas as it reacts with the welding arc. This makes FCAW an ideal type of welding for dirty, rusty and contaminated materials. Keep reading if you would like to learn more about FCAW.
What is FCAW welding?
FCAW is one of the main components of the Welding Technology program at Universal Technical Institute (UTI). In the program, students are introduced to welding tools including hand grinders, pedestal grinders, plasma cutters, CNC pipe cutters and more.
What is the difference between stick welding and flux core welding?
The difference is that with FCAW flux is at the center of the electrode, whereas in stick welding flux coats the entire electrode.
What do welders need to account for when welding?
Welders need to account for time to remove slag to make the weld look clean. Flux-Cored Welding Techniques. There are a few different processes a welder can use when performing flux-cored welding. These variants include self-shielded FCAW and gas-shielded FCAW.
What is flux core welding?
Flux-cored welding, also known as flux-cored arc welding (FCAW), is a type of welding that is suitable for the outdoors, enabling welders to meld metals and other materials together by applying heat and pressure.
Why use self shielding FCAW?
Self-shielded FCAW is typically used outdoors because FCAW using a separate gas shield would have issues with wind potentially blowing it away. Flux agents used in gas-shielded processes are designed to help deliver deeper penetration and work with out-of-position welds.
What is the diameter of FCAW G wire?
FCAW-G wires tend to be less expensive than FCAW-S wires. Both wires are typically available in diameters ranging from .035 to 7/64 of an inch. Flux-Cored Welding Polarity. The polarity for flux-cored welding processes depends on whether they are self-shielded or gas-shielded.
What is FCAW wire?
The most common FCAW wires are geared toward welding mild steel. But others are high in nickel and are designed for welding special alloys. All of these wires come in a variety of sizes as well. In a fabrication setting, the selection will usually depend upon the WPS (Welding Procedure Specification).
Why is FCAW-G called dual shield welding?
FCAW-G is called Dual Shield welding because it has two complementary ways that the weld is ‘shielded’ during welding.
What type of wire is used for welding mobile?
Other Variables. These two wires that are listed are simply the two largest categories for Flux-Cored welding wire. The most common FCAW wires are geared toward welding mild steel.
Why is flux coated welding less expensive than 75/25?
The first is that it is less expensive than the 75/25 Argon-CO2 mix. Flux-Cored welding when used with CO2 tends to also dig more into the metal. This can be frustrating especially when you have to clean out the divots made before welding again.
Why use a self shielding welder?
This is because Self-Shielding welding uses more equipment. If the work is to be done up high, though the deposition rate is much lower, it is oftentimes easier to throw a small Arc welder in the scissor lift. Carrying the MIG equipment can be a hassle in certain situations since it’s a more complicated setup.
Why is a wire feeder used?
The deposition rate can be 10 times higher than Stick welding. Since the filler metal runs off of a wire-feeder, this also means that you will not have to make as many stops and starts.
Is flux cored arc welding more efficient than SMAW?
When it comes to structural steel fabrication, few welding processes are more efficient than Flux-cored Arc Welding (FCAW). Using the same essential equipment as Metal Inert Gas Welding (MIG or GMAW), Flux-cored Arc welding deposits filler metal using a flux-cored wire. The result is a deposition rate that is about 10 times higher than Shielded Metal Arc Welding (SMAW or Stick). Developed in the early 1950s, Flux-cored welding has increased efficiency in production environments.
How does FCAW work?
FCAW process works on direct currents. It can be connected either by electrode positive ( reverse polarity) or electrode negative ( straight polarity ). In addition, the flux-cored wire is designed in the way that it can work with both DCEP or DCEN.
Why is FCA welding so hard?
FCA welding process is a bit difficult due to its internal shielding , not external like others. The shielding is very positive, and after welds, it produces some spatter. As the process goes on, it lays a slag that covers the weld. Normally, the slag is removed after some time when it became cool.
What is flux cored arc welding?
Flux Cored Arc Welding is an automatic or semi-automatic arc welding process using a wire that contains flux in its core. FCAW is mainly two types i.e. FCAW-S and FCAW-G. And after burning, it creates shielding gases and produces welds. Flux-cored arc welding is an internal shielding process and produces some spatter as well. After the welding, it leaves a slag and needs to be removed later.
What are the problems with FCA welding?
In the FCA process, there is a possibility of mechanical problems like irregular wire feed, melted contact tips, and porosity of the weld. Welders need to remove slag covering the weld frequently. The electrode wire of the FCAW process has a higher cost vis-a-vis a solid electrode wire.
What is FCA electrode?
gas-shielded, flux-cored electrodes (FCAW-G) and self-shielded, flux-cored electrodes (FCAW-S). They are steel tubes with flux inside them. Electrodes can be wrapped in a coil or spool. They are as follows:
Why is slag removed from a weld?
Normally, the slag is removed after some time when it became cool. As a result, slag protects the weld in molten form and imparts it some time for being cold . Most of the mild steel applications outdoor use the FCAW welding type.
When was FCAW-G developed?
The first-time FCAW-G process (gas-shielded flux-cored arc welding) was developed in the 1950s. Years after year, the manufacturing units made so many improvements in the shape of its equipment and products. During that time, the FCAW process was limited to the line of low alloy steel electrodes and carbon steel. So, it was offering this either for all-position welding or flat and horizontal only.
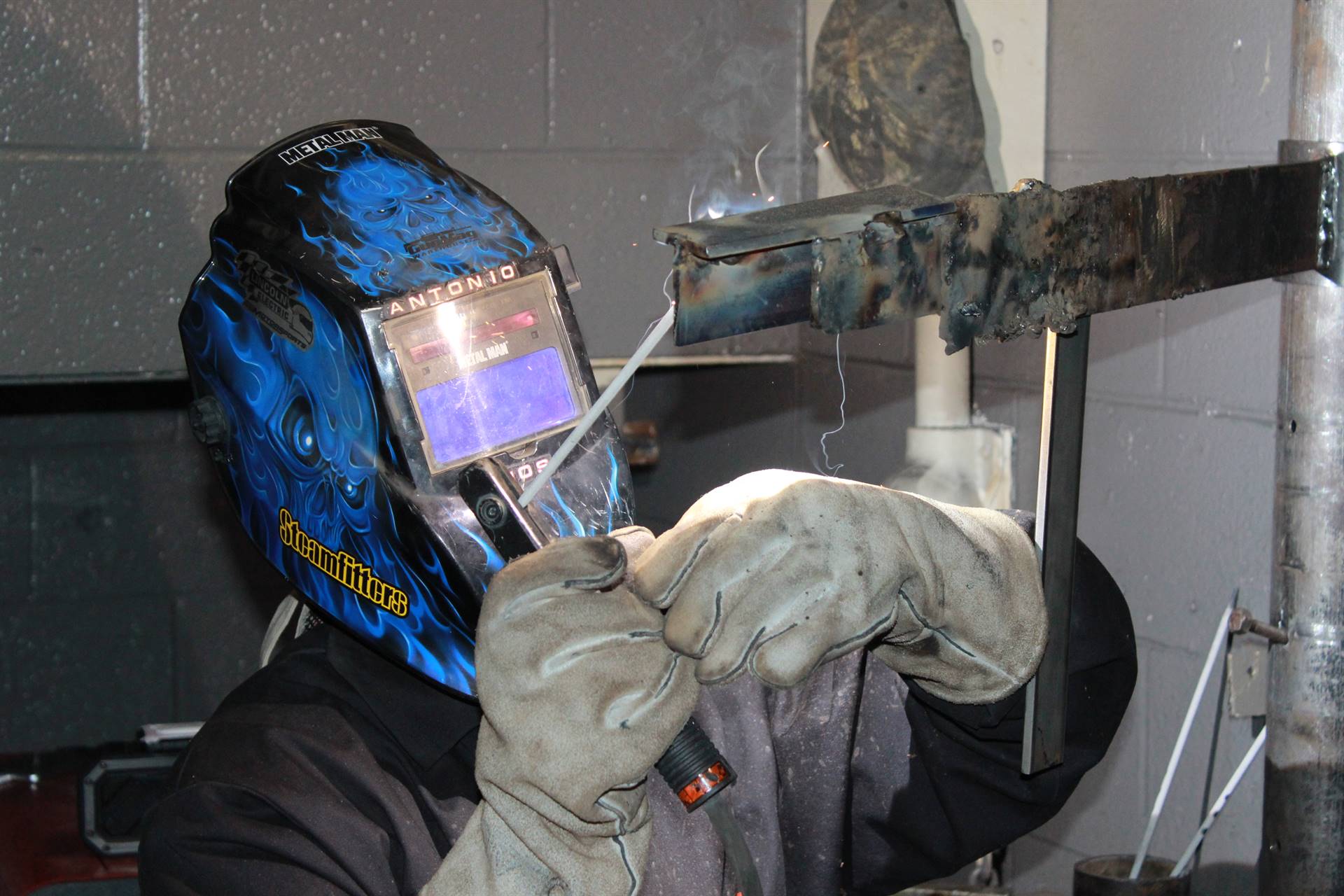
Overview
Flux-cored arc welding (FCAW or FCA) is a semi-automatic or automatic arc welding process. FCAW requires a continuously-fed consumable tubular electrode containing a flux and a constant-voltage or, less commonly, a constant-current welding power supply. An externally supplied shielding gas is sometimes used, but often the flux itself is relied upon to generate the necessary protection from the atmosphere, producing both gaseous protection and liquid slag protecting th…
Types
One type of FCAW requires no shielding gas. This is made possible by the flux core in the tubular consumable electrode. However, this core contains more than just flux. It also contains various ingredients that when exposed to the high temperatures of welding generate a shielding gas for protecting the arc. This type of FCAW is attractive because it is portable and generally has good penet…
Process variables
• Wire feed speed
• Arc voltage
• Electrode extension
• Travel speed and angle
• Electrode angles
Advantages and applications
• FCAW may be an "all-position" process with the right filler metals (the consumable electrode)
• No shielding gas needed with some wires making it suitable for outdoor welding and/or windy conditions
• A high-deposition rate process (speed at which the filler metal is applied) in the 1G/1F/2F
Disadvantages
Of course, all of the usual issues that occur in welding can occur in FCAW such as incomplete fusion between base metals, slag inclusion (non-metallic inclusions), and cracks in the welds. But there are a few concerns that come up with FCAW that are worth taking special note of:
• Melted contact tip – when the contact tip actually contacts the base metal, fusing the two and melting the hole on the end.