
What is life cycle costing technique in construction industry?
This method is also known as life cycle costing technique in construction industry. The life cycle costing technique helps to reduce the overall cost of a project by selecting best alternative designs and components to minimize the cost not only at the time of construction, but also the over the full life of the project.
What is whole life costing?
Whole life costing is the process of systematic economic consideration of all whole life costs and benefits over a period of analysis, as defined in the agreed scope. The above definitions are extracted from BS ISO 15686-5. 1. Construction Cost B. Other Construction-Related Costs 2. Maintenance Costs 3. Operation Costs 4. Occupancy Costs 5.
What is life cycle cost analysis (LCCA)?
LCCA considers all the costs associated with obtaining, owning, and disposing of an investment. Life cycle cost analysis is especially useful where a project comes with multiple alternatives and all of them meet performance necessities, but they differ with regards to the initial, as well as the operating, cost.
What is the lifespan of a building?
The “life cycle” part means that LCC assesses all costs that occur over the building’s lifetime including construction costs, maintaining, operating, and end-of-life related costs. To be more specific, the lifespan of a building consists of five main stages: concept planning, design, construction, operations, and replacement or disposal.
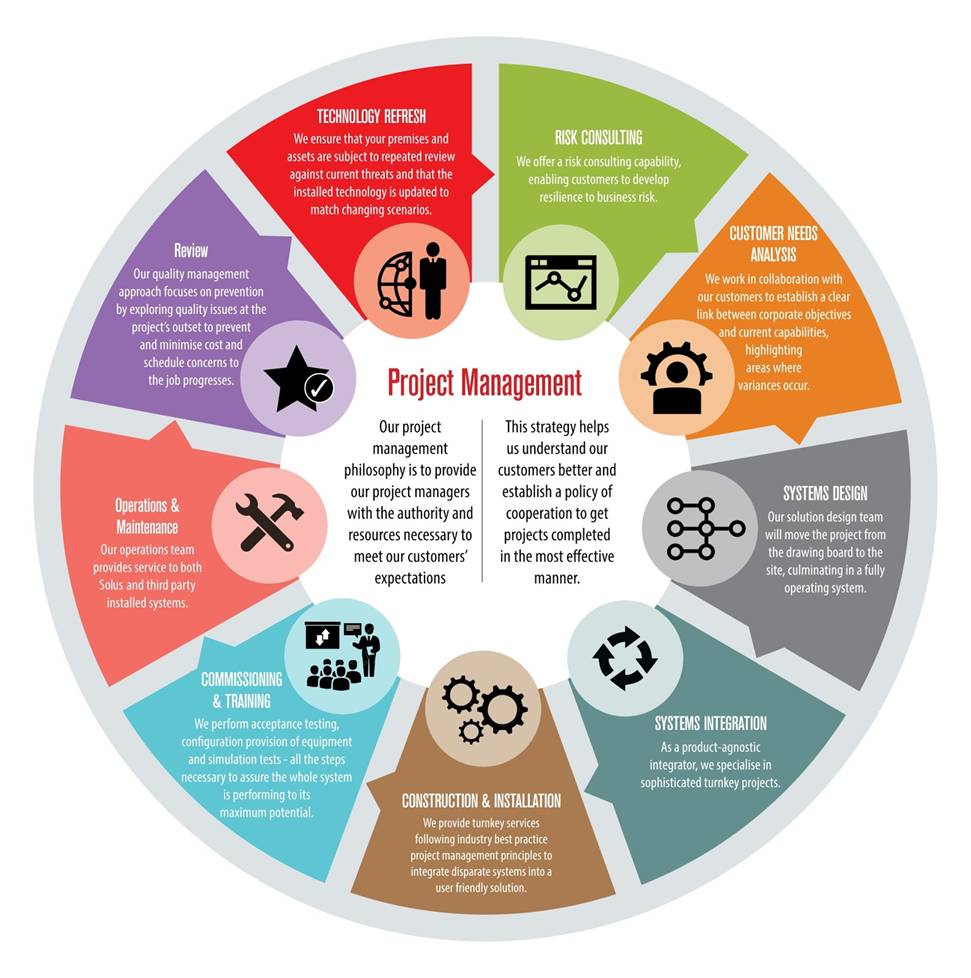
What is an example of life cycle cost?
For example, think of a car. The car's price tag is only part of the car's overall life cycle cost. You also need to consider expenses for car insurance, interest, gas, oil changes, and any other necessary maintenance to keep the car running. Not planning for these additional costs can set you back.
How do you calculate the cost of life cycle?
LCC = C+PV Recurring – PV Residual Value C is the 0-year construction cost. PV recurring is the present value of all recurring cost. PV residual value is the present value of residual value. It represents the amount of value the owner will obtain or expect to get eventually when the asset is disposed.
What is life cycle costing in engineering?
Life-cycle cost analysis is the process during which the project team assesses the cost of a building, building material, or piece of equipment throughout its entire useful life. It not only focuses on the more obvious acquisition and construction costs, but also on how much it will cost to operate and maintain.
What are the benefits of life cycle costing?
Primary benefits of life cycle cost analysis It provides a mechanism for identifying and addressing issues with the original design. An LCC's lifetime perspective results in better durability, less maintenance, fewer risks, and lower operational spending and can even lead to an increased building lifespan.
What is the purpose of life cycle cost analysis?
Life-Cycle Cost Analysis (LCCA) Method. The purpose of an LCCA is to estimate the overall costs of project alternatives and to select the design that ensures the facility will provide the lowest overall cost of ownership consistent with its quality and function.
How do you calculate life cycle cost in Excel?
1:0724:41Life Cycle Costing (LCC) in Excel 1 - YouTubeYouTubeStart of suggested clipEnd of suggested clipSo we can do it a number of different ways um in excel we can use the calculation that we looked atMoreSo we can do it a number of different ways um in excel we can use the calculation that we looked at in class which is one over the power of one plus.
What is meant by Kaizen costing?
Kaizen costing is a cost reduction system used after a product's design has been completed and it is in production. Business professor Yasuhiro Monden defines kaizen costing as. The maintenance of present cost levels for products currently being manufactured via systematic efforts to achieve the desired cost level.
How do you calculate the life cycle cost of equipment?
Life Cycle Cost for the system and equipment to be evaluated equals the sum of the following cost elements: • Capital Cost. Operating Cost. Cost of Deferred Production. = The total standard deviation.
How do you calculate the life cycle cost of equipment?
Life Cycle Cost for the system and equipment to be evaluated equals the sum of the following cost elements: • Capital Cost. Operating Cost. Cost of Deferred Production. = The total standard deviation.
How do you calculate life cycle cost in Excel?
1:0724:41Life Cycle Costing (LCC) in Excel 1 - YouTubeYouTubeStart of suggested clipEnd of suggested clipSo we can do it a number of different ways um in excel we can use the calculation that we looked atMoreSo we can do it a number of different ways um in excel we can use the calculation that we looked at in class which is one over the power of one plus.
How do you calculate your life cycle in numerology?
Basically, take your date of birth's numerical value, add all those digits together by category (year, month, day), and keep adding each of those digits together until you finally end up with a single digit. For example: Say your birthday is July 3, 1995, or 7/3/1995.
What is LCC in building?
2. Green building certification credits . LCC credits are included in many green building certification schemes and in some LCC is a mandatory credit.
What is LCCA in construction?
Life cycle cost analysis (LCCA or LCC for short) is an objective method for measuring and managing the lifetime costs of any project or asset. In construction, it enables design options to be compared from a lifetime perspective to reduce overall costs.
Why do you need to combine LCC and LCA?
Combine LCC with LCA to ensure that you are making the best cost-and carbon-saving decisions for your project.
How effective is LCC?
The LCC is most effective when implemented in the early project phases before major decisions have been made. Engage the whole team. Particularly when creating alternatives to ensure the full potential of the project is captured. Repeat the LCC throughout the project.
How long is the One Click LCA trial?
Get access to 14-day free trial of One Click LCA for Building & Infrastructure projects.
What is life cycle cost?
Life cycle cost in construction projects is a process of economic decision analysis, which helps taking decisions on investments in new construction. These decisions on investments are analyzed for the payback over the life of the investment.
How does life cycle costing work?
The life cycle costing technique helps to reduce the overall cost of a project by selecting best alternative designs and components to minimize the cost not only at the time of construction, but also the over the full life of the project.
What is Time Value of Money in Construction Projects?
Time value of money is defined as the purchasing power of money now to the purchasing power of the same money in future. It is a method of assessment of market for the value of money with time. For example, you can purchase a component at a price $5000 now, but will you be able to purchase same component at the same price 5 years later? What if you would like to purchase it now, then will you be able to gain advantage over the purchase after 5 years from now? Or to gain advantage, you would like to invest it somewhere else and purchase same after 5 years. It is a method of assessment of cash flow from present time to future with the analysis of profit or loss, or the benefits one would get with the amount.
What is life cycle cost analysis in construction?
Life cycle cost analysis is the formal process of calculating the ROI you can expect from a particular investment in your facility, taking into account all factors of cost and payoff. The LCCA provides long-term cost projections for a particular building investment over its useful life cycle, not just up front costs.
How to treat life cycle cost analysis?
Treat life cycle cost analysis as an ongoing process to revisit through all phases of the construction process. As your design develops from early concepts to robust models and final drawings, a multi-disciplined team should continuously reassess it to ensure its accuracy and help you get the best possible value. It’s key not to reject investments based on early life cycle cost analysis, but rather use the LCCA to inform the ongoing process. Your team can’t fully determine the details of resource availability, design, and savings without conducting detailed analysis in the later stages of design.
How does tilt up concrete wall system reduce construction costs?
Some may reduce energy or operating costs, while others, such as Tilt-Up concrete wall systems, may significantly reduce your construction schedule, in turn reducing opportunity costs and real project costs. For some renewable energy systems, the payoff can come in the form of state or utility rebates or grants.
What is LCCA in project management?
The LCCA is ultimately a tool for putting solid numbers behind your decision making. With it, you can evaluate where you should best spend your project dollars.
How to capture savings and value from a project?
Integrate a formal life cycle cost analysis into your project from the start. The best opportunity to capture savings and value from your project is before decisions have been made — before your project is locked into a set course. By having a multi-disciplined team of estimators, designers, construction professionals, sustainability experts and specialty contractors advise you early on, you’ll be assured of identifying and implementing the best-value solutions for your project. For this reason, we recommend using the Design-Build process.
What is BLCC in building?
The National Institute of Standards and Technology’s (NIST) Building Life Cycle Cost (BLCC) program provides owners several key measures to determine the value of an investment, including:
How to achieve a best value project?
The best place to start is by consulting a seasoned, expert project team that will work in open communication with you to deliver construct able solutions that match your objectives. One tool that provides a comprehensive analysis of a facility’s value is the life cycle cost analysis (LCCA).
What is life cycle cost analysis?
Life-cycle cost analysis (LCCA) is a method for assessing the total cost of facility ownership. It takes into account all costs of acquiring, owning, and disposing of a building or building system. LCCA is especially useful when project alternatives that fulfill the same performance requirements, but differ with respect to initial costs ...
How are construction costs estimated?
LCCA can be repeated throughout the design process if more detailed cost information becomes available. Initially, construction costs are estimated by reference to historical data from similar facilities. Alternately, they can be determined from government or private-sector cost estimating guides and databases. The Tri-Services Parametric Estimating System (TPES) developed models of different facility types by determining the critical cost parameters (i.e., number of floors, area and volume, perimeter length) and relating these values through algebraic formulas to predict costs of a wide range of building systems, subsystems, and assemblies.
How to make cash flows time equivalent?
To make cash flows time-equivalent, the LCC method converts them to present values by discounting them to a common point in time, usually the base date. The interest rate used for discounting is a rate that reflects an investor's opportunity cost of money over time, meaning that an investor wants to achieve a return at least as high as that of her next best investment. Hence, the discount rate represents the investor's minimum acceptable rate of return.
When are costs relevant?
Only those costs within each category that are relevant to the decision and significant in amount are needed to make a valid investment decision. Costs are relevant when they are different for one alternative compared with another; costs are significant when they are large enough to make a credible difference in the LCC of a project alternative. All costs are entered as base-year amounts in today's dollars; the LCCA method escalates all amounts to their future year of occurrence and discounts them back to the base date to convert them to present values.
How long is a service period?
This is the period over which operational costs and benefits are evaluated. In FEMP analyses, the service period is limited to 40 years.
When are recurring cash flows discounted?
In OMB and FEMP studies, all annually recurring cash flows (e.g., operational costs) are discounted from the end of the year in which they are incurred; in MILCON studies they are discounted from the middle of the year. All single amounts (e.g., replacement costs, residual values) are discounted from their dates of occurrence.
What is the first task of LCCA?
The first and most challenging task of an LCCA, or any economic evaluation method, is to determine the economic effects of alternative designs of buildings and building systems and to quantify these effects and express them in dollar amounts.
What is life cycle cost analysis?
Life cycle cost analysis offers a general framework that can be used to assess the need for additional costs during a project’s useful life. With such knowledge in mind, it is possible to regulate cash outflows by forecasting requirements of a project.
Why is life cycle cost analysis important?
Life cycle cost analysis is especially useful where a project comes with multiple alternatives and all of them meet performance necessities, but they differ with regards to the initial , as well as the operating , cost . In this case, the alternatives are compared to find one that can maximize savings.
How does LCCA work?
All the costs involved are treated as base year values equivalent to present-day dollar amounts; LCCA transforms all dollar values into future year occurrence equivalents and then discounts all the values to their base dates. In such a way, it’s easy to find their present value.
What is rigorous modeling based on LCCA?
Rigorous modeling based on LCCA incorporates value engineering so that a project’s cost outline can lower expenditures by a huge margin. The procedures are done through a series of tests on the cost of operation.
What is the other thing that is important in infrastructural development?
The other thing that is important in infrastructural development is operating expense, which consists of a number of costs, including utility, manpower, insurance, equipment, health, and routine and planned repairs.
What is project related cost?
Project-related costs can be classified into initial costs, fuel costs, replacement costs, operation and maintenance costs, finance charges#N#Service Charge A service charge, also called a service fee, refers to a fee collected to pay for services that relate to a product or service that is being purchased .#N#, and residual values.
What is capital budgeting?
Capital Budgeting Best Practices Capital budgeting refers to the decision-making process that companies follow with regard to which capital-intensive projects they should pursue. Such capital-intensive projects could be anything from opening a new factory to a significant workforce expansion, entering a new market, or the research and development of new products.
What is life cycle cost analysis?
What is the Life Cycle Cost Analysis? Life Cycle Cost Analysis is used to examine and assess the total cost of resource ownership and takes into account expenses related to buying, maintaining, operating and disposing of a project or an object. It is used especially to select the best project when there are multiple projects ...
What does "longer project" mean?
Costly: The longer project means the long-time duration which makes it more costly than other methods.
What is PV recurring?
PV recurring is the present value of all recurring cost
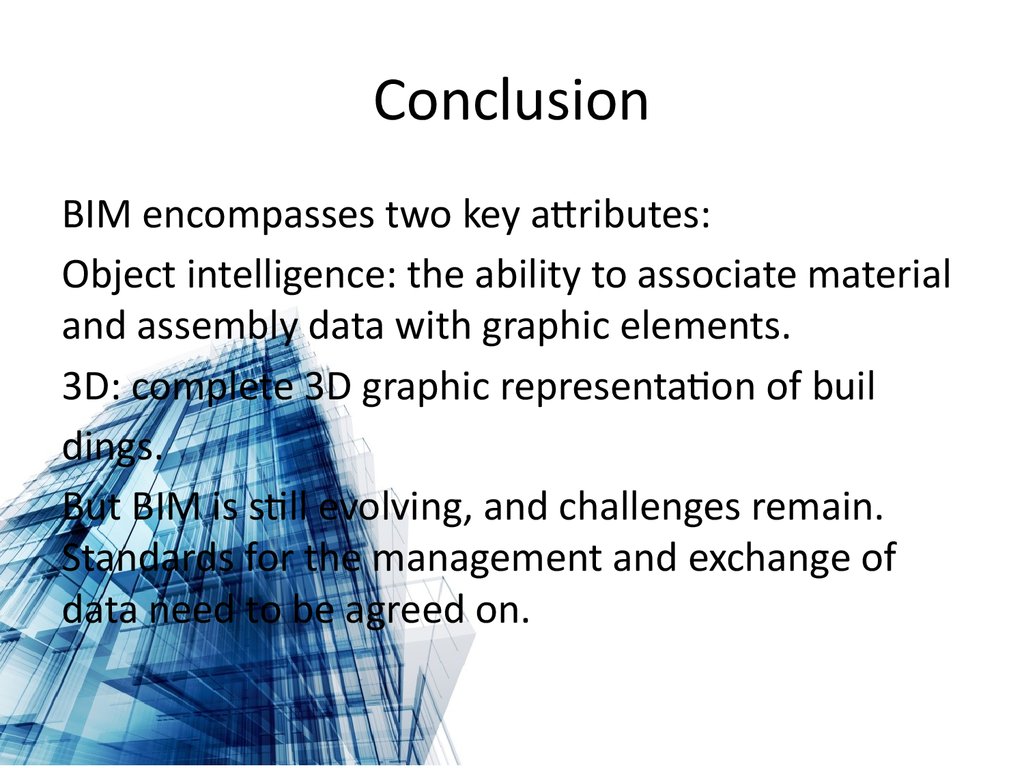
Life-Cycle Cost Analysis’S Role in Value Engineering
- Conducting a life-cycle cost analysis can be an extremely important exercise when it comes to value engineering. By looking at the project from a big-picture perspective, you’re able to determine what options offer the best value in the short term and long term. Value engineering i…
Initial Cost
- The initial costs include the purchasing price and installation or construction. These are the upfront costs associated with the building material or the equipment you choose. They’re also the costs that tend to have the most influence on purchasing decisions because they have the biggest impact on the project’s budget at the time of the decision. However, initial costs are just the tip o…
Operating Costs
- One of the first post-construction costs you’ll likely run into is the operating costs. These include everything from fuel to run the equipment to regular cleaning or upkeep. These costs are more of an estimate, as they tend to fluctuate from year to year or month to month. However, these estimates can provide valuable insight into your long-term costs. When it comes to equipment, …
Maintenance Costs
- Another aspect you need to consider is the maintenance factor associated with the item. How easy is it to find maintenance technicians that are qualified to diagnose and work on your equipment? If new parts are needed, will they be easy to find, or will they have to be purchased from abroad or custom-made? What are the warranties like? Will the manufacturer stand behind …
Replacement Costs
- Nothing lasts forever, and eventually, specific portions of the building or specific equipment will have to be replaced. All costs associated with replacing that item need to be factored into the life-cycle cost. This can include physically removing or uninstalling the item, the acquisition of a new item, and the installation of the new item. While one can’t predict with 100% accuracy what the …
Disposal Fee
- Life-cycle cost analysis considers the cost of a product throughout its entire life. This includes when the product reaches the end of its useful life and needs to be disposed of. This can be an easy cost to overlook, as so much of what we dispose of on a day-to-day basis can be done relatively simply and for free. However, when it comes to certain building materials or equipment…
How to Maximize Your Project’S Value with Life-Cycle Cost Analysis
- Whether you’re renovating or building a new structure, a construction project can be a large investment. The choices you make during the planning process have the potential to impact the building and your budget for years to come. Taking a long-term look at your building materials and equipment with a life-cycle cost analysis can help ensure you’re making the best decisions for y…
A. Life-Cycle Cost Analysis (LCCA) Method
B. Costs
- There are numerous costs associated with acquiring, operating, maintaining, and disposing of a building or building system. Building-related costs usually fall into the following categories: 1. Initial Costs—Purchase, Acquisition, Construction Costs 2. Fuel Costs 3. Operation, Maintenance, and Repair Costs 4. Replacement Costs 5. Residual Values—Resale or Salvage Values or Dispos…
C. Parameters For Present-Value Analysis
- Discount Rate
In order to be able to add and compare cash flows that are incurred at different times during the life cycle of a project, they have to be made time-equivalent. To make cash flows time-equivalent, the LCC method converts them to present values by discounting them to a common point in tim… - Cost Period
Length of study period:The study period begins with the base date, the date to which all cash flows are discounted. The study period includes any planning/construction/implementation period and the service or occupancy period. The study period has to be the same for all alternatives co…
D. Life-Cycle Cost Calculation
- After identifying all costs by year and amount and discounting them to present value, they are added to arrive at total life-cycle costs for each alternative: LCC = I + Repl — Res + E + W + OM&R + O LCC = Total LCC in present-value (PV) dollars of a given alternative I = PV investment costs (if incurred at base date, they need not be discounted) Repl = PV capital replacement costs Res = P…
E. Supplementary Measures
- Supplementary measures of economic evaluation are Net Savings (NS), Savings-to-Investment Ratio (SIR), Adjusted Internal Rate of Return (AIRR), and Simple Payback (SPB) or Discounted Payback (DPB). They are sometimes needed to meet specific regulatory requirements. For example, the FEMP LCC rules (10 C.F.R. § 436, Subpart A) require the use of either the SIR or AI…
F. Evaluation Criteria
- Lowest LCC (for determining cost-effectiveness) NS > 0 (for determining cost-effectiveness) SIR > 1 (for ranking projects) AIRR > discount rate (for ranking projects) SPB, DPB < than study period (for screening projects)
G. Uncertainty Assessment in Life-Cycle Cost Analysis
- Decisions about building-related investments typically involve a great deal of uncertainty about their costs and potential savings. Performing an LCCA greatly increases the likelihood of choosing a project that saves money in the long run. Yet, there may still be some uncertainty associated with the LCC results. LCCAs are usually performed early in the design process when …
H. Design and Analysis Tools
- The use of computer programs can considerably reduce the time and effort spent on formulating the LCCA, performing the computations, and documenting the study. Listed below are several LCCA-related software programs: 1. Building Life-Cycle Cost (BLCC) Program—Economic analysis tool developed by the National Institute of Standards and Technology for the U.S. Department o…