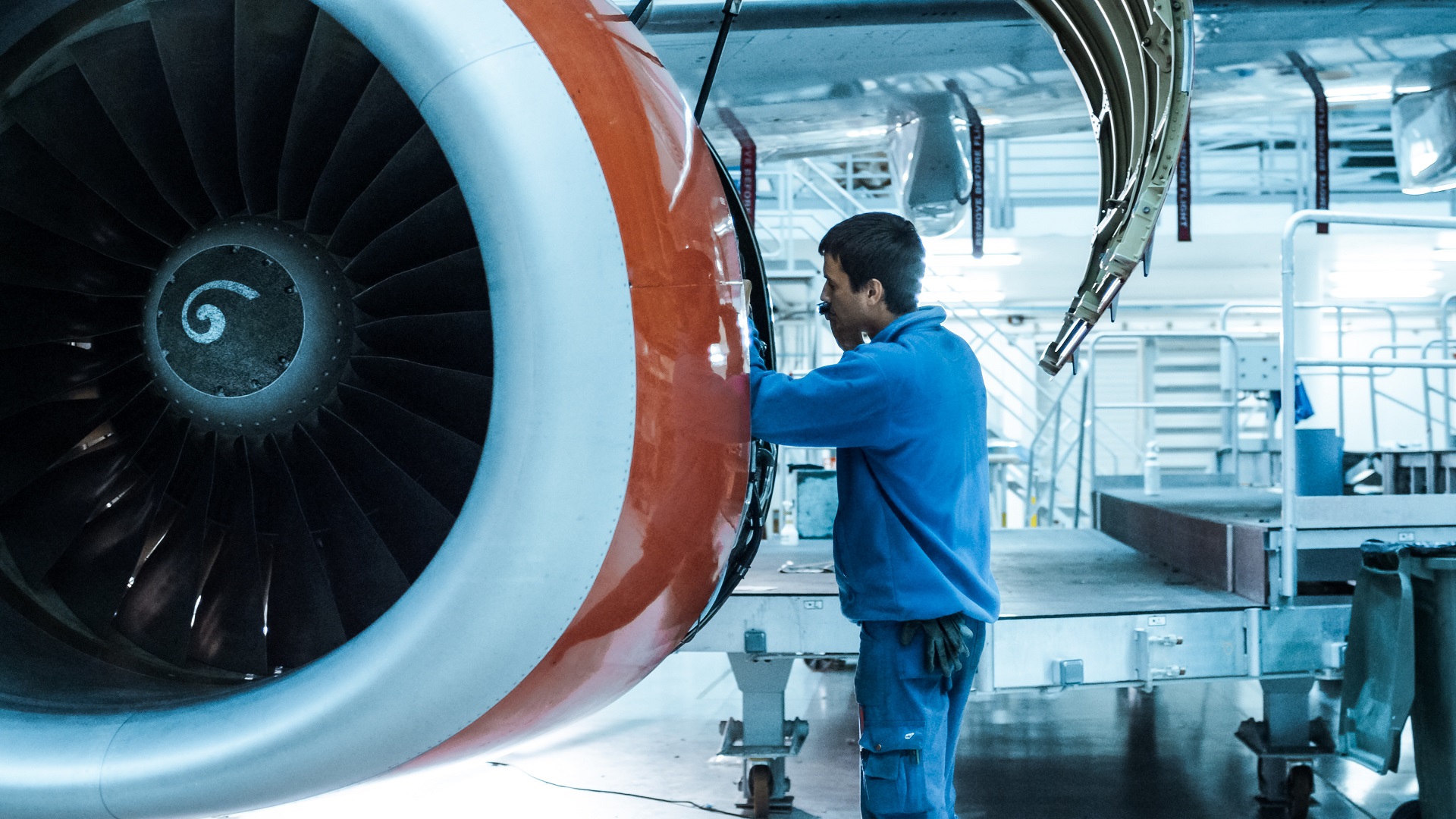
What is preventive maintenance?
How effective? Preventive maintenance is that activity performed in some routine or regularly scheduled fashion designed to keep equipment in an existing state, prevent deterioration or failure and identify work of a corrective nature to keep equipment from causing non-productive time in any capacity.
What is corrective maintenance in a power plant?
Corrective maintenance, also known as crisis management, is needed for power plant equipment issues that occur when there are noticeable concerns regarding the functionality or condition of the equipment. While preventive maintenance is scheduled to help prevent equipment from breaking down during production, these things happen.
How much should you spend on corrective maintenance?
The recommended balance for maintenance is 80% preventive to 20% corrective. While you want to lean toward preventive maintenance whenever possible, corrective maintenance is still important and will never be eliminated completely. A cost-benefits analysis on all of your assets may help to support the case for scheduled corrective maintenance.
What are the different types of corrective maintenance?
Corrective maintenance can fall into two categories: scheduled and unscheduled. Scheduled corrective maintenance is a repair that needs to be made, but doesn’t have to be performed immediately. Unscheduled corrective maintenance occurs when a repair is required immediately due to the failure of an asset critical to production.

What is the difference between preventive and corrective?
In simple terms, corrective action prevents recurrence, while preventive action prevents occurrence. Corrective action is carried out after a nonconformity has already occurred, whereas preventive action is planned with the goal of preventing a nonconformity in its entirety.
What is the similarities between preventive and predictive maintenance?
Preventive maintenance and predictive maintenance focus on increasing asset reliability and reduce the possibility of failures. They are in two forms: one is to schedule the maintenance, and the other helps to schedule work in advance, rather than when they are performed.
Why corrective maintenance is preferred to preventive maintenance?
These advantages include: Reduced Planning: Corrective maintenance requires less planning than preventive maintenance, even when scheduling repairs. Simple Process: Corrective maintenance is a simple process that is need-based, allowing maintenance teams to focus on other areas until required.
What is the difference between preventive and preventative maintenance?
Is it preventive or preventative? Preventive and preventative usually mean the same thing—they're both commonly used as adjectives to describe things intended to prevent something (negative) from happening. Historically, preventive has been more common.
What is the difference between preventive and perfective maintenance?
Perfective maintenance is concerned with the change in the software that occurs while adding new functionalities in the software. Preventive maintenance involves implementing changes to prevent the occurrence of errors.
What is the difference between scheduled maintenance and preventive maintenance?
Planned maintenance refers to any strategy where you plan and perform maintenance tasks before a fault occurs. Preventive maintenance is more specific. It refers to maintenance tasks that you schedule and perform while an asset is still working to prevent it from failing unexpectedly.
What are the 2 types of maintenance?
Most types of maintenance fall under two main categories: preventive and corrective.
What is the difference between corrective maintenance and reactive maintenance?
There's an important distinction in that corrective maintenance can be planned, whilst reactive maintenance is typically enacted after a failure has occurred or the machine is showing signs of damage.
What is the basic difference between preventive and corrective methods of fertility control?
Answer: Corrective maintenance is done after problem while preventive is before problem. Corrective maintenance is done randomly while preventive is done frequently. Preventive maintenance will minize the need of corrective, while corrective will maximize the preventive actions.
What's the difference between preventive and proactive maintenance?
Preventive repairs work well on equipment and parts with a low chance of causing downtime ― smaller components and consumables with finite life, usually available at a low cost. Proactive repairs work well for major components where decision-making data is available.
What is the difference between reactive and preventive maintenance?
Reactive maintenance takes place after a problem has occurred, costing companies hundreds or thousands of dollars in repair. Planned/preventive maintenance occurs before a problem presents itself, which increases the longevity of equipment and a company's bottom line.
What are the examples of preventive maintenance?
5 Examples of Preventive Maintenance in ActionPreventive Maintenance Equipment Inspections. ... Clean Equipment Regularly to Minimize Dirt and Dust. ... Lubricate Rotating Parts to Prevent Premature Wear. ... Check Machinery Power to Optimize Energy Efficiency. ... Repair or Replace Equipment Before it Fails.
What is the difference between prescriptive and predictive maintenance?
Predictive maintenance (PdM) relies on IoT sensor devices and data to predict when assets will require maintenance to prevent equipment failure. Prescriptive maintenance collects and analyzes data on an equipment's condition and makes specialized recommendations to reduce operational risks.
What are some of the most common different types of preventive maintenance?
There are 4 major types of preventive maintenance. ... Usage-based preventive maintenance. ... Calendar/time-based preventive maintenance. ... Predictive maintenance. ... Prescriptive maintenance.
What is the difference between predictive and proactive maintenance?
While proactive maintenance endeavors to get to the root cause of a potential problem, predictive maintenance collects relevant data to appropriately schedule routine fixes to ensure equipment is operating effectively.
What are the different types of maintenance and how do they differ?
Preventive maintenance – includes regular and periodic (time-based) schedules. Corrective maintenance – occurs when an issue is noticed. Predetermined maintenance – follows a factory schedule. Condition-based maintenance – occurs when a situation or condition indicates maintenance is needed.
When implementing a proactive preventive maintenance program, should you establish frequency of PMs with a conservative view?
When first implementing a proactive Preventive Maintenance program, you should establish frequency of PMs with a conservative view. Many sites implement the PM program using Manufacturer-suggested PM frequencies that, although usually on the conservative side, are a good starting point.
How much of maintenance time should PM be?
In a Proactive Maintenance environment, PM activities should account for approximately 30% of total maintenance resource time.
How often should a maintenance program be performed?
When establishing an effective maintenance program, one must determine not only which Preventive Maintenance (PM) routines to accomplish, but how often should they be done. The answer to this question would seem on the surface to be quite simple and, in fact, one proven theory is that the PM to Corrective Maintenance (CM) work order ratio should be about 6 to 1. This theory assumes that the PM inspections should reveal some type of corrective work that should be completed on an asset on average every 6 times it is accomplished. The assumption is that, if the ratio is greater than 6:1 you are performing the PM too often; if the ratio is less then 6:1, you are not performing it often enough. (The “6 to 1 Rule”, proven by John Day, Jr., Manager of Engineering and Maintenance at Alumax of South Carolina, during the period when Alumax of South Carolina was certified as the first “World-Class” maintenance organization) You might accept this theory, put it in place in your maintenance program, and forget about reading the remainder of this article. Or, come along and we will attempt to prove or disprove this theory.
Why use corrective maintenance and preventive maintenance together?
This use of corrective and preventive maintenance together helps to provide additional benefits over either technique alone — reducing emergency maintenance orders, extending equipment lifespan and decreasing equipment-related downtime.
How does preventive maintenance help?
Research on the approach has demonstrated that preventive maintenance can significantly extend the lifespan of manufacturing equipment and decrease maintenance costs over time
What happens if a business adopts a solely corrective approach to maintenance?
Typically, if a business has adopted a solely corrective approach to maintenance, they won’t plan for regular repairs or maintenance checks as they would with preventive maintenance. They also won’t follow recommended maintenance schedules provided by original equipment manufacturers or developing their own.
What are the two most common maintenance strategies?
Two of the most common maintenance strategies are corrective and preventive maintenance. The two strategies differ significantly in terms of investment, time needed and potential results.
Why are reactive maintenance orders only placed once downtime is inevitable?
Reactive maintenance is not planned or scheduled, and reactive work orders are only placed once downtime is inevitable because the machine to be repaired is non-functional or cannot function safely.
What does it mean to reduce maintenance checks?
Reducing maintenance checks means less money spent on paying technicians and less scheduled downtime. The strategy could be effective for equipment that is not essential. However, it’s likely to be risky in any case — businesses that adopt a corrective maintenance strategy should accept that some problems will go undetected until they begin causing noticeable performance issues.
Why is effective maintenance important?
For any manufacturer, effective maintenance is essential. The right approach can significantly extend the lifespan of a machine while reducing downtime, preventing damage and cut down on the need for repairs.
What is corrective maintenance?
1. Corrective Maintenance (CM) :#N#CM is a type of maintenance task or action is usually performed after equipment failure. It’s simply considered as all activities that restore failed or broken-down assets to its normal working condition. It is reactive in nature. Whenever any assets fail, either it is replaced, repaired, or restored to its operability.
Why is PM performed at random intervals?
PM mainly aims to avoid expensive repairs and corrective actions. It is performed at random intervals as it is only performed when a failure occurs. It is performed at regular intervals as asset maintenance is important and should be checked regularly to avoid any failure occurrence.
What is a PM?
Whenever any assets fail, either it is replaced, repaired, or restored to its operability. 2. Preventive Maintenance (PM) : PM is a type of maintenance task or action that is usually performed before equipment failure. It’s simply considered as all activities that maintain assets and prevent them from failure or breakdown.
Why is PM more expensive than PM?
It can be more expensive than PM as some equipment failure causes greater damage to system. It can be expensive but it prevents assets from failure. It can affect overall system as some assets failure can cause greater loss in production. It prevents loss in production by reducing chances of failure occurrence.
What is PM in production?
PM overall increases life cycle of assets. This process results in loss of production, loss of product quality, loss of time. This process leads to increase in production, increase in product quality, no loss of production time.
Is downtime better in PM or CM?
It is better for safety of employees and working environment as it reduces risk of injury. Downtime of assets is more in CM. Downtime of assets is less in PM.
Is CM a preventive process?
It is preventive in nature. CM is performed after asset failure or after anything goes wrong. PM is performed before asset failure or before anything goes wrong. It is less complex and simple process because it does not involve any planning to prevent asset from failure.
What is preventive maintenance?
Preventive maintenance is regularly scheduled inspections, tests, repairs, and replacements of critical equipment. Conducting preventive maintenance increases equipment efficiency, reduces premature failures, and prolongs the life of the equipment.
What is corrective maintenance?
Corrective maintenance, also known as crisis management, is needed for power plant equipment issues that occur when there are noticeable concerns regarding the functionality or condition of the equipment. While preventive maintenance is scheduled to help prevent equipment from breaking down during production, these things happen.
What is the difference between the two?
Preventive maintenance is ultimately about reliability. If you keep your plants’ equipment in good shape, it’s less likely to break down, and you’ll have less downtime in the end.
What is the corrective maintenance ratio?
One proven theory is that the PM to corrective maintenance (CM) work order ratio should be about 6 to 1. This theory assumes that PM inspections reveal some type of corrective work that should be completed on an asset on average every six times it is performed. The assumption is that, if the ratio is greater than 6:1, you are performing the PM too often; if the ratio is less than 6:1, you are not performing it often enough. ( The “6 to 1 Rule” was proven by John Day, Jr., manager of Engineering and Maintenance at Alumax of South Carolina, during the period when Alumax of South Carolina was certified as the first “World-Class” maintenance organization.) You might accept this theory, put it in place in your Maintenance program and forget about reading the remainder of this article. Or, you might choose to continue reading, as we attempt to prove or disprove this theory.
What is predictive maintenance?
Predictive maintenance (PdM) technology uses some proven testing method, such as thermography, tribology or ultrasonics, to trend equipment performance and “predict” when certain preventive maintenance activity should be performed, thereby heading off a potential failure.
What are the types of maintenance?
Consider the types of maintenance actually being performed at your facility. There is preventive, predictive, condition monitoring, corrective and emergency work in your basket, with every type of facility and industry expending certain percentages of Maintenance resources on each type.
How much of maintenance time should PM be?
In a proactive Maintenance environment, PM activities should account for approximately 30% of total Maintenance resource time.
What is condition monitoring?
Condition monitoring is the practice of closely monitoring equipment on a continuous basis to provide early detection of symptoms that could cause problems or failure, then performing some corrective actions to preclude the problem or failure.
How effective is your PM program?
The obvious question is: “How effective is your PM program?” The short answer is: “If your PM program isn’t finding problems, it isn’t effective.”
When do most failures occur in equipment history?
Asset age —Equipment histories will prove that most failures occur during infancy (newly installed or overhauled) and old-age (self-explanatory).
Corrective Maintenance
Corrective Maintenance is any task that corrects a problem with an asset to a condition in it can perform its intended function. This type of maintenance occurs when an issue is detected through condition monitoring, when a routine inspection uncovers a potential fault or when a piece of equipment breaks down. It can be planned and unplanned.
Preventive Maintenance
Preventive maintenance is cyclical maintenance that is planned and performed on equipment to ensure that failures do not occur and to lessen the consequences of breakdowns. A preventive maintenance plan is ideal when the engineering team can plan, prevent or predict any malfunction of equipment so it has the least possible impact.
Predictive Maintenance
Predictive Maintenance is maintenance that monitors the performance and condition of equipment during normal operation. By performing it, businesses can predict when equipment failures might occur and therefore reduce the likelihood of failures.
What is corrective maintenance?
A corrective maintenance strategy, also known as a reactive or ‘run to failure’ strategy, works on the premise that an item is allowed to fail and is only then repaired or replaced. In order for this to work, the consequence of failure needs to be acceptable and have no significant impact on the environment or safety. The failure should also have no detrimental economic impact for the asset owner. Corrective maintenance is also necessary when failure occurs.
When is corrective maintenance necessary?
Corrective maintenance is also necessary when failure occurs. This type of maintenance needs to be performed once a malfunction occurs in order to restore an asset to the correct operating conditions so it can perform its intended action.
How does predictive maintenance differ from preventive maintenance?
Predictive maintenance differs slightly from preventive maintenance as it takes an even more robust approach to determining when maintenance is necessary. Rather than using a set time-scale or usage frequency to determine when maintenance is required, predictive maintenance uses analytics and continual monitoring of data to detect if equipment failure is likely to occur.
What is maintenance management?
Maintenance management for any type of asset needs to determine whether a corrective, preventive or predictive maintenance strategy is best suited to that particular product or asset. These different approaches to maintenance all have their own benefits and drawbacks, so choosing the correct maintenance activity requires an understanding of each approach and how they may impact your assets and work schedule.
What does it mean to understand the condition of your equipment?
Understanding the condition of your equipment means that you are in control of scheduling your maintenance. You can ensure the required experts and parts are on-site when you have time to make repairs rather than having to take a costly reactive approach, while also minimising disruptions to workflow to boost productivity and profits.
Why is it important to do regular checks on equipment?
By undertaking regular checks on your equipment, you reduce the chance of it breaking down unexpectedly. Depending on the equipment in question, this can create a safer working environment for your staff.
Is reactive maintenance a cost?
As a reactive maintenance procedure, there is little cost associated with monitoring and assessment either before or after failure.
What is preventive maintenance?
Preventive maintenance (PM) is an action carried out in a programmed manner to keep equipment in the desired functioning state. Another objective of PM is to detect corrective maintenance action to be taken to prevent an emergency or a non-productive situation.
Is PM based on manufacturer suggested interval good?
Implementing a PM program based on the manufacturer suggested interval is a good starting point but that cannot be the benchmark. This routine requires adjustment, based on the operation history of the equipment.
Is preventive maintenance reliable?
Working through all these factors, if the ratio of preventive maintenance to corrective is approximately 6:1 (for 6 PM there is 1CM) the preventive maintenance program can be called reliable . This is a proven theory and holds good for many facilities though it cannot be steadfastly held for all PM and for all processes.
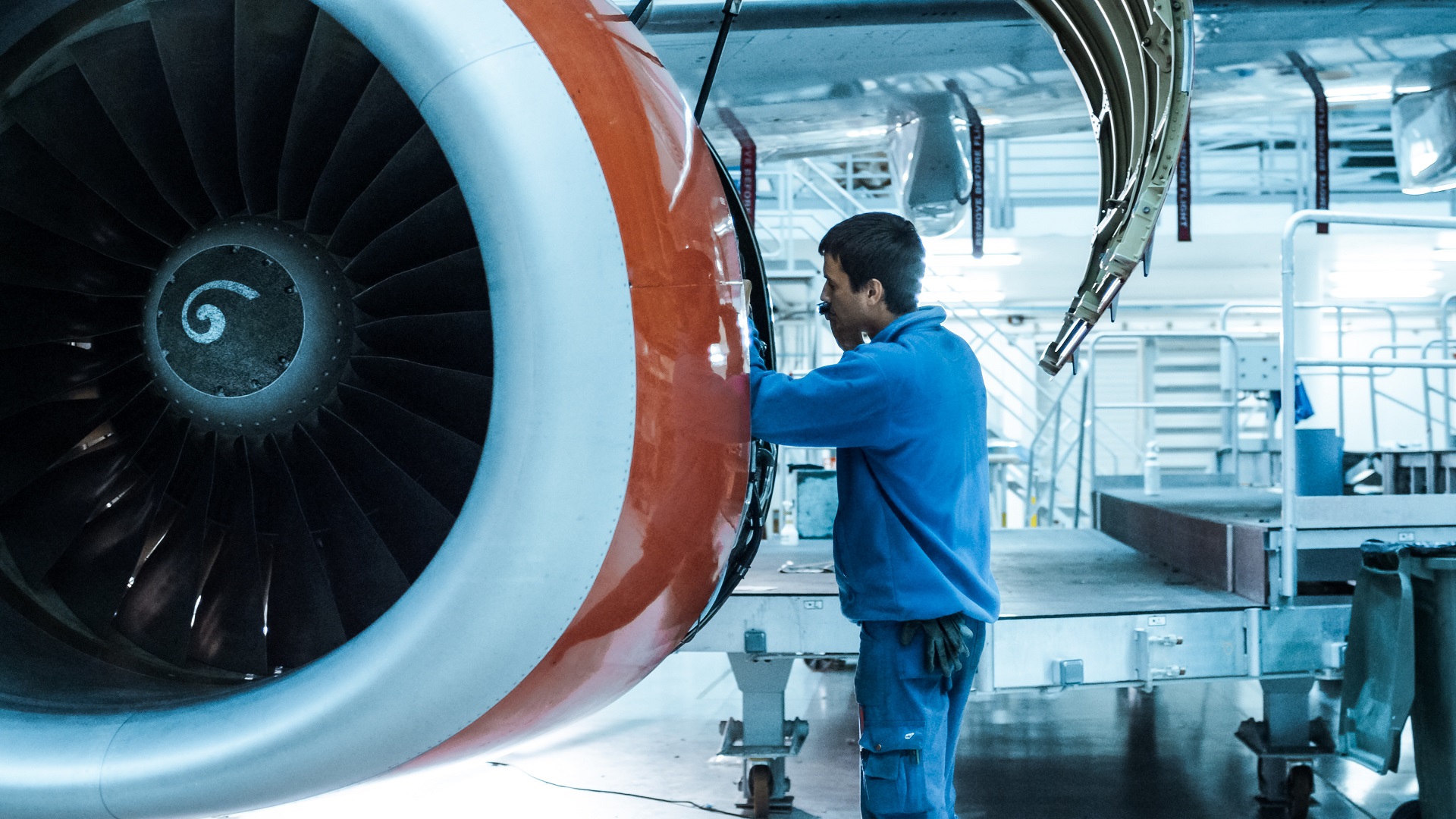
About Corrective Maintenance
About Preventive Maintenance
- Preventive maintenance (PM) is maintenance that is proactively performed on an asset with the goal of lessening the likelihood of failure, reducing unexpected downtime, and prolonging its useful life.Examples of preventive maintenance include: 1. Changing the oil on a riding lawn mower 2. Cleaning an air duct 3. Replacing rusted bolts on a machine 4. Inspecting a productio…
Difference Between Corrective and Preventive Maintenance
- If you’ve been getting by without a preventive maintenance plan in place, is shifting the focus to preventing machine failure really worth the effort? See the chart below for a comparison of corrective and preventive maintenance. The recommended balance for maintenance is 80% preventive to 20% corrective. While you want to lean toward preventive maintenance whenever p…
Preventive Maintenance
Potential Drawbacks of PM
Corrective Maintenance
Combining Corrective Maintenance with A Preventive Approach
Operational Monitoring and Corrective Maintenance
Corrective vs. Preventive Maintenance: Which Is Right For Your Business
- Both corrective and preventive maintenance are common approaches to machine maintenance. In general, preventive maintenance will cost more in the short run but provide significant long-term savings compared to reactive or solely corrective maintenance. Running a machine to failure tends to be much more expensive than maintaining it, but those high ...