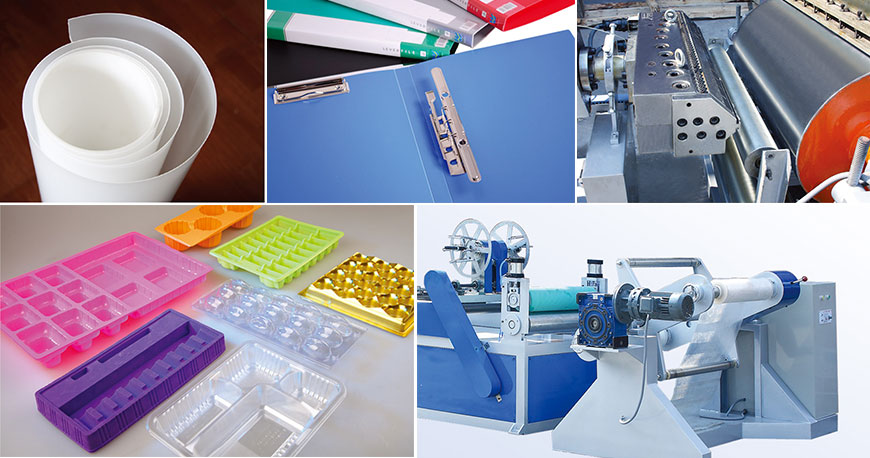
Conclusion
- Vacuum forming is an ancient technique that is used for manufacturing plastic products.
- It is the simplest form of thermoforming process which uses vacuum suction pumps for work.
- It has two types of molds: male mold and female mold.
- The vacuum forming process has the following steps for manufacturing
What is vacuum forming and what are the benefits?
The vacuum forming method offers a range of benefits to manufacturers with high volume capability and the simplicity of storing large stocks of plastic sheets. These benefits carry down to clients offering good quality and high volumes at low costs, so the process has found its way into many industries and uses.
What is the difference between thermoforming and vacuum forming?
Vacuum forming is a simplified version of thermoforming, where a sheet of plastic is heated to a forming temperature, stretched onto a single-surface mold, and forced against the mold by a vacuum. This process can be used to form plastic into permanent objects such as turnpike signs and protective covers.
Why vacuum form plastic parts?
Plastic vacuum forming has several distinct advantages over other methods of manufacturing plastic parts. hief among these is the low cost of tooling for short and long run production parts. Many products once thought to be injection molded parts, can many times be redesigned for Vacuum, Pressure forming or even Fabrication processes.
What can DIY vacuum forming machines be used for?
DIY vacuum forming machines can also get the job done, and the building process makes a great educational project for kids and teens. When using a vacuum forming machine, remember to always follow the manufacturer’s instructions, wear safety gear, and only use the machine in a well-ventilated area.
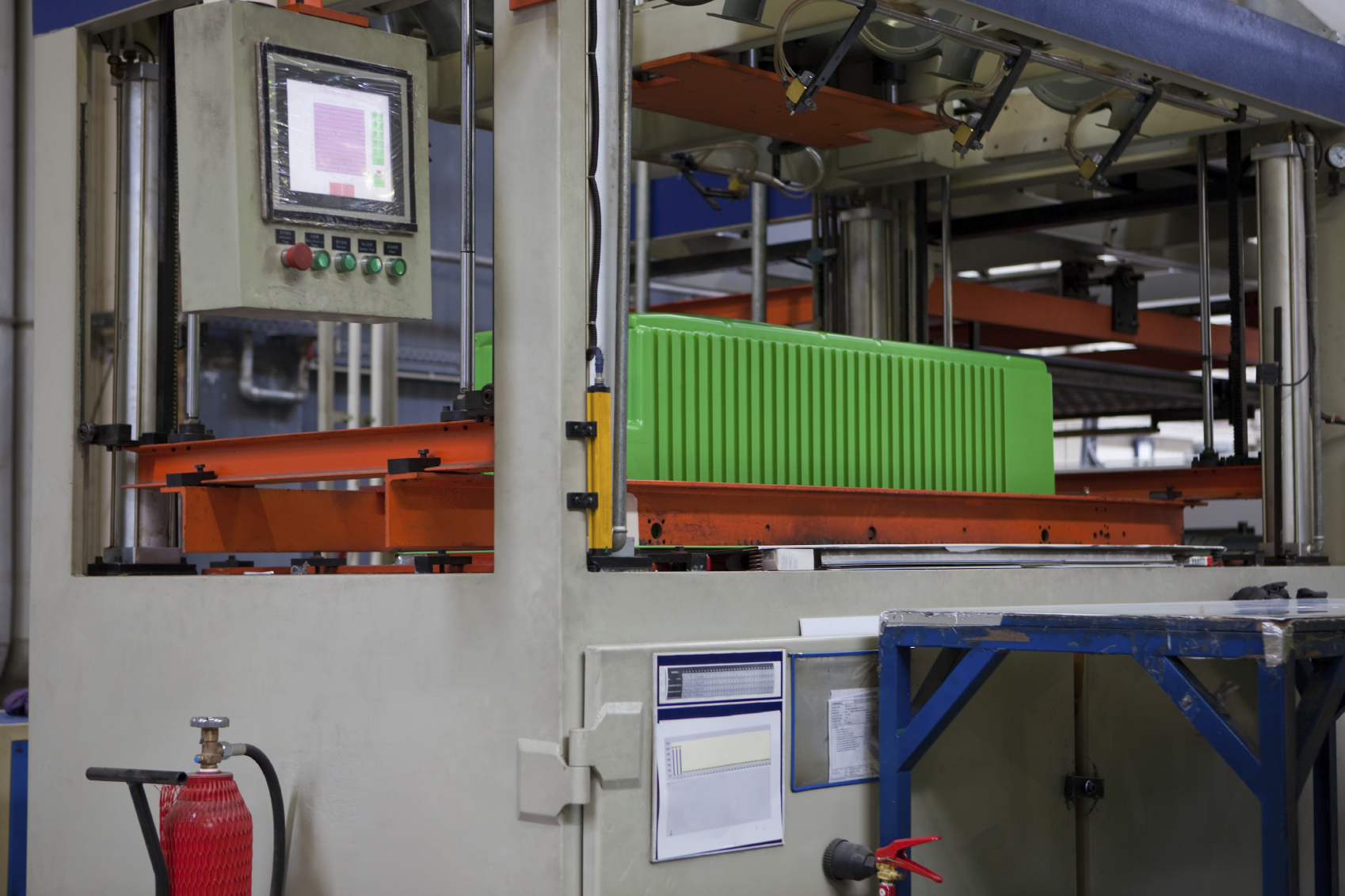
What is vacuum form used for?
Vacuum forming is a manufacturing method used to shape plastic materials. During the vacuum forming process, a sheet of plastic is heated and then pulled around a single mold using suction.
What are the pros and cons of vacuum forming?
What Are the Advantages and Disadvantages of Vacuum Forming?AdvantagesDisadvantages✔ Excess plastic can be recycled into more sheets for future production needs✖ Excess moisture can cause unwanted bubbles to form✔ Supports rapid prototyping processes✖ Clear or light-colored parts can show debris from the mold6 more rows•Sep 7, 2020
How is vacuum forming used in society?
One of the biggest uses for vacuum forming is the construction of modern boat hulls. Using a combination of fiberglass and carbon fibers, boat manufacturers are able to produce extremely strong and rigid hulls that are much lighter than more traditional metallic or wooden hulls.
Who uses vacuum forming?
Vacuum forming is used by a large number of companies to manufacture a range of plastic or acrylic based products. Vacuum forming is used to make industrial & automotive components; enclosures and trays; POS retail display; stage and film props; signage, and for product development / rapid prototyping.
What products are made by vacuum forming?
Typical industry examples besides product packaging include: fascias for outdoor kiosks and automated teller machines, enclosures for medical imaging and diagnostic equipment, engine covers in a truck cab or for construction equipment, and railcar interior trim and seat components.
How thick can you vacuum form?
Vacuum forming sheet thickness may range from 0.0005 to 0.50 inch (0.0127 to 12.7 mm). However, for prototype applications, the Formech machines are limited to sheet thicknesses between 0.0005 to 0.25 inch (0.0127 to 6.35 mm). After a prototype is vacuum formed, it will shrink and grip the tool.
What polymer is used when vacuum forming?
There are many different types of plastics that are used in vacuum forming and these are some of the more common ones: Acrylonitrile Butadiene Styrene (ABS) Acrylic – Perspex (PMMA) Co-Polyester (PETG)
How does vacuum forming work?
Vacuum forming heats a plastic sheet until it becomes pliable, stretches the material onto a mold, and then uses vacuum pressure to obtain the desired part geometry. The simplest type of plastic thermoforming, vacuum forming uses wooden patterns and epoxy tools in addition to temperature-controlled aluminum tooling.
What temperature is needed for vacuum forming?
high-density polyethylene (HDPE), which requires a core temperature of approximately 280°F for optimal forming.
How many steps are there in vacuum forming?
six stepsThere are six steps and processes involved in professional vacuum forming.
What are the limitations of vacuum casting?
DisadvantagesProduction Restriction: Vacuum casting is born for low volume production. ... Loose Tolerance: The silicone molding is formed by tightly clinging to the master model. ... Continuous Flaw: Molding manufacturing can cause continuous flaws easily.More items...•
What are the advantages and disadvantages of injection Moulding?
Plastic injection moulding advantages centre around great precision and high repeatability, combined with speed, a low cost per part and a huge choice of available plastics. Disadvantages include a higher initial cost and lead time than some other processes.
What are potential issues with vacuum forming a large former?
The most common vacuum forming problems we come across include: Mold or tool is too high in relation to its base area. Sharp vertical corners with minimal draught angles. Deep male molds in close proximity to each other.
What are the disadvantages of injection molding?
The disadvantages of injection moldingStart-up costs are high. Since custom tooling must be created for each injection molded part, initial start-up costs are high and this isn't economical for low-volume production runs. ... Initial lead times are long. ... Design changes are expensive.
Why do manufacturers use vacuum forming?
Manufacturers often use vacuum forming to produce food-grade containers and parts for the medical industry because it is compatible with plastics that can be sterilized or kept free of contaminants. For example, high-density polyethylene (HDPE) is frequently used to vacuum form food storage containers.
Why do people use vacuum forming?
Many manufacturers, designers, and other professionals choose vacuum forming because it offers a blend of design flexibility at a relatively low cost compared to other manufacturing methods. The benefits of vacuum forming include:
What Is Vacuum Forming?
Vacuum forming is a manufacturing method used to shape plastic materials. During the vacuum forming process, a sheet of plastic is heated and then pulled around a single mold using suction.
How to vacuum form plastic?
The step-by-step vacuum forming process works as follows: 1 Clamp: A sheet of plastic is placed in an open frame and clamped into place. 2 Heat: The plastic sheet is softened using a heat source until it reaches the appropriate forming temperature and becomes pliable. 3 Vacuum: The framework containing the heated, pliable sheet of plastic is lowered over a mold and pulled into place via a vacuum on the other side of the mold. Female (or convex) molds need to have tiny holes drilled into crevices so that the vacuum can effectively pull the thermoplastic sheet into the appropriate form. 4 Cool: Once the plastic has been formed around/into the mold, it needs to cool. For larger pieces, fans and/or cool mist are sometimes used to speed up this step in the production cycle. 5 Release: After the plastic has cooled, it can be removed from the mold and released from the framework. 6 Trim: The completed part will need to be cut out of the excess material, and edges may need to be trimmed, sanded, or smoothed.
What is the difference between pressure forming and vacuum forming?
The main difference between pressure forming and vacuum forming is the number of molds that are used. Vacuum forming is the simplest type of plastic thermoforming, that uses one mold and vacuum pressure to obtain the desired part geometry.
What is thermoforming in manufacturing?
Thermoforming is a manufacturing process where a sheet of plastic is heated to become pliable, then shaped or contoured using a mold, and trimmed to create a final part or product. Vacuum forming and pressure forming are both different types of thermoforming processes.
Why is vacuum forming used in packaging?
Vacuum forming is often used for food packaging because it is compatible with food-grade plastic and can produce parts that are easy to sanitize. These ornate chocolates were produced in vacuum formed molds and are resting in a clear vacuum formed tray.
Why is vacuum forming used?
Why Vacuum Forming is a Popular Method. Many industries use vacuum forming because it’s a streamlined manufacturing method. The process involves placing a sheet of plastic inside vacuum forming equipment and heating the sheet until it’s soft.
Why is it important to work with a manufacturer?
This is why it’s important to work with a manufacturer that offers multiple options and capabilities. Even if vacuum forming isn’t the right choice for your project, an experienced and capable manufacturer will guide you to a more viable alternative that will get your product to market fast and at the lowest possible cost. ...
What can you use to cut off plastic?
After letting the plastic cool, engineers can then use a CNC machine or another tool to cut off any excess plastic. They can also perform an additional pressure forming step, where positive air pressure pushes plastic into crevices in the mold for added detail.
Is vacuum forming good for a product?
Vacuum forming is more appropriate for some projects and uses than for others. For example, if you need the walls of your product or component to be extremely thick and durable, this may not be possible to achieve using this method alone.
Is vacuum forming good for short run manufacturing?
As long as the product or component you’re making isn’t too thick or complex, vacuum forming is likely a good option. It’s also recommended for short run manufacturing. If any of these qualities apply to your project, you should discuss vacuum forming options with your manufacturer.
What Is Vacuum Forming?
Vacuum forming is one of the most economical thermoforming technologies and works best on products that are simple and don’t require great detail. Vacuum forming plastics is a good choice for tight budgets, time constraints, items with large dimensions and lower-volume, shorter runs.
Advantages of Vacuum Forming
Plastic product manufacturing companies use industrial vacuum forming as a suitable replacement for other custom forming processes that use sheet metal, fiberglass or wood. Compared to traditional methods, vacuum forming plastic offers several advantages, including:
Vacuum Forming vs. Pressure Forming
Choosing between vacuum forming and pressure forming all depends on the benefits you need.
Turn Your Vision Into a Reality
The team at Joslyn Manufacturing will work with you to make sure the vacuum forming process is labor- and material-efficient, maintains consistency from piece to piece, produces parts with the correct dimensions, rigidity, features, texture and finish, as well as satisfies your need for affordable, durable plastic parts.
Why use vacuum forming?
1.3 Why use Vacuum Forming? Plastic vacuum forming has several distinct advantages over other methods of manufacturing plastic parts. hief among these is the low cost of tooling for short and long run production parts. Many products once thought to be injection molded parts, can many times be redesigned for Vacuum, Pressure forming or even Fabrication processes. Another advantage of vacuum forming is the ability to generate prototypes and tooling rapidly. PDI Plastics generates tooling in house using AD 3D geometry and N machining to produce all molds. We typically machine molds directly out of aluminum. We also work with synthetic tooling board and wood depending on the project.
What is thermoforming?
1.1 What is Thermoforming/Vacuum Forming? Thermoforming is a relatively simple process to convert a flat plastic sheet into a three-dimensional object. In its simplest form thermoforming involves heating up a plastic sheet until it is pliable, then stretching it over a mold and letting it cool, so it sets to the mold shape. y adding small holes through the mold and attaching a vacuum pump, the heated plastic can be sucked down over the mold. This is vacuum forming, the most widely used type of thermoforming. We use the term vacuum forming as that is what we do. 1.2 What is Vacuum Forming used to make? It is used to make a wide range of things from clear packaging for salad and cupcakes, all the way up to hot tubs and truck bed liners.
Why is angle important in molds?
angle allows the material to stretch more evenly over the mold which prevents 'cold capping'.
What is Vacuum Forming?
In case you don’t know, vacuum forming is the oldest and most common process of processing plastic materials. It is vastly used around the globe for a variety of works and the importance of vacuum forming is undeniable in our day to day lives. Vacuum forming can be considered as a simplified version of thermoforming. In this process, the sheet of plastics is heated to reach a certain forming temperature.
What material is used for vacuum forming?
There is a different variation of the materials used in the vacuum forming. However, the most suitable material for vacuum forming is mainly thermoplastics. As an example, we can talk about high-impact polystyrene sheets (HIPS). There are different things that are used around the mold that include structural foam, cast, wood, and sometimes machined molds.
Why are thermoplastics used in vacuum forming?
As we discussed prior, a lot of different varieties of plastic are used in the vacuum forming method. Most of them are thermoplastics because of the advantage it offers. It can be repeatedly heated and cooled as needed and it can revert to the original shape. For these benefits, thermoplastics are mostly used in the vacuum forming method. There are also different variations of thermoplastics. Below, we will let you know some of the thermoplastics that are used in vacuum forming.
Can you use plastic for vacuum forming?
There is a different variation of plastics used in vacuum forming. However, that doesn’t mean that you can use any variation of the plastic for vacuum forming. Below we will let you know about the plastics that can be used for vacuum forming as well as the ones that cannot be used.
Is polycarbonate a good vacuum forming plastic?
There are some other variations of the vacuum forming plastics which include polycarbonate, polyvinylchloride, etc. The polycarbonate is pretty strong and impact-resistant and also very costly. The polyvinylchloride is inexpensive and also transparent, making it a good choice for a variety of purposes.

Overview
Vacuum forming is a simplified version of thermoforming, where a sheet of plastic (in various forms HIPS (High impact polystyrene) for low impact products, or for Bathroom shower trays ABS, and exterior vehicle parts HDPE, plus various other types of vacuum formable materials) is heated to a forming temperature, stretched onto a single-surface mould, and forced against the mo…
Typical applications
Original equipment manufacturers (OEMs) utilize heavy gauge vacuum formed components for production quantities in the range of 250–3000 units per year. Vacuum-formed components can be used in place of complex fabricated sheet metal, fiberglass, or plastic injection molding. Typical industry examples besides product packaging include: fascias for outdoor kiosks and automated teller ma…
Common problems
There are some problems encountered in the vacuum forming process. Absorbed moisture can expand, forming bubbles within the plastic's inner layers. This significantly weakens the plastic. However, this can be solved by drying the plastic for an extended period at high but sub-melting temperature. Webs can form around the mold, which is due to overheating the plastic and so must be carefully monitored. Webbing can also occur when a mold is too large or parts of the mold ar…
Types of molds
There are numerous patterns one can make with vacuum forming. The most inventive way to use vacuum forming is to take any small item, replicate it many times and then vacuum form the new pattern to create a more cohesive form. The vacuum forming helps tie the individual pieces together and make one mold out of many pieces that can easily be replicated. From there plaster, concrete, …
Finishing methods
Once a vacuum forming has been created out of a sheet of plastic, a finishing operation will be needed in most cases to turn it into a usable product. Common vacuum forming finishing methods include:
• Guillotining: The product is cut out of the sheet by pressing a blade through the product into a die underneath. This is a clean way of removing vacuum formed …
Further reading
• Soroka, W. Fundamentals of Packaging Technology, IoPP, 2002, ISBN 1-930268-25-4
• Walsh, D. E. Do It Yourself Vacuum Forming for the Hobbyist (rev. ed.), Workshop Publishing, Lake Orion, MI, 2002, OCLC 46798883
• Yam, K. L. Encyclopedia of Packaging Technology, John Wiley & Sons, 2009, ISBN 978-0-470-08704-6