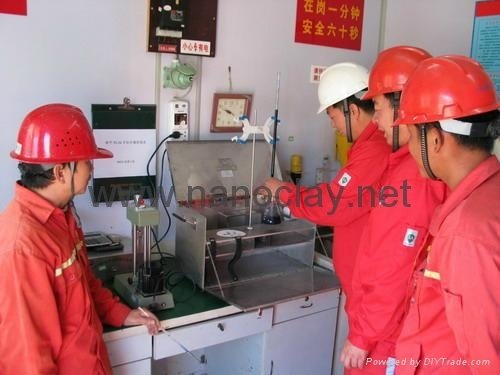
The Types of Drilling Fluid Additives
- 1. Dispersant (also known as diluent)
- 2. Fluid loss control additives
- 3. Weighting agent
- 4. Friction reducer (diluent, dispersant, water reducing agent, turbulence inducing regulator)
- 5. Thickening time regulator
- 6. Specific gravity regulator
How to mix drilling fluid?
To achieve these tasks, a number of process requirements must be satisfied:
- Mixing equipment must be capable of rapidly incorporating and dispersing powders into the water.
- The bentonite particles must be reduced to their finest constituent parts to expose the maximum surface area to the surrounding liquid and activate the gelling effect.
- A degree of shear is required to obtain functionality.
What chemicals are used in drilling?
The principal ones used and their typical applications are as follows:
- Sodium Cyanide: Depression of iron sulfide minerals such as pyrite, pyrrhotite and arsenopyrite. ...
- Sodium Ferro cyanide: Depression of Cu and Fe sulfide in Cu/Mo separation.
- Zinc Sulfate: Used alone, or in combination with cyanide, for depression of Zn minerals in the flotation of Pb/Zn, Cu/Zn, and Cu/Pb/Zn ores.
What makes petroleum oil suitable as a hydraulic fluid?
This chapter explores the mineral base oils. The largest class of hydraulic fluids today is composed of refined hydrocarbon base oils, i.e., petroleum oils, containing suitable additives to supplement the base oils' inherent properties. Petroleum base oils are manufactured by a variety of refining processes from carefully selected crude oils.
Can you mix engine oil with hydraulic fluid?
No you cannot use Motor Oil in a Hydraulic System. Motor Oil runs at a much higher temperature and Hydraulic Oil starts to fail at around 45c. You cannot as water is one of the worst contaminates for Hydraulic Oil.

What are the three basic components of a drilling fluid?
The Components of Drilling Fluids/Mud Water-based drilling mud most commonly consists of Bentonite clay (gel) with additives such as Barium sulfate (Barite), Calcium carbonate (chalk) or Hematite. Various thickeners are used to influence the viscosity of the fluid, e.g. xanthan gum, guar gum, glycol, or starch.
What is emulsifier in drilling fluids?
Emulsifiers are critical to establishing and maintaining strong emulsions in oil-and-synthetic based drilling fluid systems. This key product provides some important functions in order to maintain a stable fluid system throughout a broad range of challenging drilling conditions.
What are the types of drilling fluid?
Drilling fluids include three main types: water-based muds, oil-based muds, and air. Air drilling fluids, such as mist, foams, and stiff foams, are used in only very specific, limited applications.
Which acid is used in drilling fluid?
Citric acidCitric acid is used to reduce pH and remove calcium when drilling cement, to reduce the potential of crosslinking polymers (xanthan and others) from iron, and to prevent fish-eyes when mixing polymers.
What does wetting agent do in oil based mud?
Wetting agents improve the preferential oil-wetting of solids in oil-based drilling muds, thereby maintaining the rheological and fluid loss properties. They also help to improve the emulsion and thermal stability of the mud system.
Is mud an emulsion?
A water-base drilling fluid that contains dispersed oil or synthetic hydrocarbon as an internal phase. Early emulsion muds used diesel or crude oil dispersed into alkaline water-base muds. Synthetic liquids are now being substituted for oils in emulsion muds.
What is the most common drilling fluid?
water-base mudsAqueous drilling fluids, generally referred to as water-base muds, are the most common and the most varied of the three drilling fluid types (Figure 1). They range in composition from simple blends of water and clay to complex inhibitive, or clay stabilizing, drilling fluid systems that include many components.
Why water is used in drilling?
Water is used during drilling to lubricate and cool the drill and remove drilling mud and rock debris. For hydraulic fracturing operations, water is mixed with chemicals that improve its ability to create fractures in the rock, and with sand to hold the fractures open and allow oil or gas to flow into the well.
What is drilling fluid made of?
Selection of drilling fluid mainly depends on the type of formation and the borehole depth. The various kinds of drilling fluid normally used are water, bentonite mud, cutting oil, and polymers (both water-based and mud-based). Water: It is freely available fluid and is primarily used in core drilling operation.
Why is bentonite used for drilling mud?
The most common use of bentonite is in drilling fluids. The bentonite in the flush fluid lubricates and cools the cutting tools whilst protecting against corrosion. As the drilling fluid generates hydrostatic pressure in the borehole, it hinders fluid and gas penetration.
Why mud is used in drilling?
The function of drilling muds conduct cuttings away from the drill face, provide a hydrostatic head that counters the pressure of gas or oil, and provide a physical and chemical means of stabilizing and protecting the rock formation that is being drilled.
What is base oil used for in drilling?
BASE FLUIDS FOR ON & OFFSHORE DRILLING & STIMULATION APPLICATIONS. Drilling operations usually require a fluid (commonly called mud); either a water-based mud, or an oil-based mud to help clean out drilled formations, to lubricate the drill bit and maintain wellbore stability.
What are types of mud?
ConclusionMud TypePrincipal ComponentsSimple freshwaterFreshwaterSimple seawaterSeawaterSpud mudBentonite, waterSaltwaterSeawater, brine or saturated saltwater; saltwater clay, starch, cellulosic polymer8 more rows•Mar 3, 2022
What is mud and its types?
Mud is soil, loam, silt or clay mixed with water. It usually forms after rainfall or near water sources. Ancient mud deposits harden over geological time to form sedimentary rock such as shale or mudstone (generally called lutites).
What is the difference between drilling fluid and drilling mud?
drilling mud, also called drilling fluid, in petroleum engineering, a heavy, viscous fluid mixture that is used in oil and gas drilling operations to carry rock cuttings to the surface and also to lubricate and cool the drill bit.
What is MD in oil and gas?
In the oil industry measured depth (commonly referred to as MD, or just the depth) is the length of the drilled borehole. In conventional vertical wells, this coincides with the true vertical depth, but in directional or horizontal wells, especially those using extended reach drilling, the two can deviate greatly.
What additives are used in drilling fluid?
Broad classes of water-based drilling-fluid additives are in use today. Clays, polymers, weighting agents, fluidloss-control additives, dispersants or thinners, inorganic chemicals, lost-circulation materials, and surfactants are the most common types of additives used in water-based muds. Weighting Agents. The most important weighting additive in ...
What is drilling fluid?
Water-based drilling fluids consist of a mixture of solids, liquids, and chemicals, with water being the continuous phase. Solids may be active or inactive. The active (hydrophilic) solids such as hydratable clays react with the water phase, dissolving chemicals and making the mud viscous. The inert (hydrophobic) solids such as sand and shale do not react with the water and chemicals to any significant degree. Basically, the inert solids, which vary in specific gravity, make it difficult to analyze and control the solids in the drilling fluid (i.e., inert solids produce undesirable effects).
What is surfactant used for?
Surfactants are used in drilling fluids as emulsifiers, dispersants, wetting agents, foamers and defoamers, and to decrease the hydration of the clay surface. The type of surfactant behavior depends on the structural groups of the molecules. Various Other Additives. There are a plethora of other additives for drilling fluids.
What additives are used to control fluid loss?
Fluid-Loss-Control Additives. Clays, dispersants, and polymers such as starch are widely used as fluid-losscontrol additives. Sodium montmorillonite (bentonite) is the primary fluid-loss-control additive in most waterbased drilling fluids. The colloidal-sized sodium-bentonite particles are very thin and sheetlike or platelike with a large surface area, and they form a compressible filter cake. Inhibitive mud systems inhibit the hydration of bentonite and greatly diminish its effectiveness. Therefore, bentonite should be prehydrated in fresh water before being added to these systems. The larger and thicker particles of sodium montmorillonite do not exhibit the same fluid-loss-control characteristics.
What are some dispersants that reduce fluid loss?
For this reason, some dispersants such as lignosulfonate (a highly anionic polymer) are more effective than others as fluid-loss reducers (IMCO 1981).
What is used to bind calcium from cement cuttings?
There are various contaminate reducers such as sodium acid polyphosphate (SAPP) used while drilling cement to bind up calcium from the cement cuttings. There are corrosion inhibitors, especially H 2 S scavengers. There are defoamers to knock out foaming and foaming agents to enhance foaming.
What is surface active agent?
A surface-active agent is a soluble organic compound that concentrates on the surface boundary between two dissimilar substances and diminishes the surface tension between them. The molecular structure of surfactants is made of dissimilar groups having opposing solubility tendencies such as hydrophobic and hydrophilic.
What is the additive that breaks up the network structure of a drilling fluid?
The additive that can break up the network structure, release free water and reduce the viscosity and shear force of the drilling fluid is called the dispersant.
What is the chemical agent used to reduce the filtration rate of the drilling fluid into formation and protect the colloidal stability?
The chemical agent used to reduce the filtration of the drilling fluid into formation and protect the colloidal stability of the drilling fluid is called fluid loss control additives. The material that can reduce the filtration rate of the cement slurry is called cement slurry filtrate reducer. At present, polyacrylamide is the most commonly used filtrate reducer.
What additives change the density of cement slurry?
The additives that can change the density of the cement slurry are called gravity regulators, including lightening agents and weighting agents.
When the fluid column pressure of the drilling fluid cannot balance the formation the pressure or well killing is required for blowout?
When the fluid column pressure of the drilling fluid cannot balance the formation the pressure or well killing is required for blowout, it is necessary to add the weighting agent to the system to increase the proportion of the drilling fluid, so as to achieve the purpose of balancing the formation pressure and preventing blowout accidents.
Can a friction reducer control cement slurry?
Satisfactory results can often be obtained by pumping cement slurry with turbulent flows. Friction reducer can control the fluidity of cement slurry and cause turbulent flows at low pump displacement.
What to consider with drilling fluids
Before diving into details about the additives that make up a drilling fluid, here is what you need to think about when mixing mud.
Water
The main ingredient of HDD drilling fluid, water, is sometimes used alone in certain soil conditions. However, water offers very little in the way of lubrication and lacks viscosity to maintain hole integrity and gel strength to float cuttings out of the hole. What water does do is provide a good base for additives and help cool HDD tooling.
Soda ash
Not all water is the same — its acidity/alkalinity pH levels can vary depending on the source. The optimal pH level for mixing HDD drilling fluid is between 8 and 9. Adding soda ash to water is an easy way to raise pH levels to that desired range, helping attain optional product hydration/yield.
Bentonite
A staple of almost all HDD drilling fluid mixes, bentonite helps create higher viscosity downhole, provides some gel strength for flushing cuttings and creates a filter cake to help reduce fluid lost into surrounding formations.
Polyanionic cellulose (PAC) polymer
PAC polymers should be added to the drilling fluid mix when working in porous zones in loose ground conditions like sand. The main benefits that PAC polymers provide are helping prevent fluid loss downhole and avoiding oversaturation to the bore formation, which can result in the hole collapsing.
Partially hydrolyzed polyacrylamide (PHPA) polymer
PHPA polymers should be used in reactive clays and shale. Downhole, PHPA bonds with the outer layers of the ground material and cuttings to help prevent fluid from absorbing and swelling, which also helps reduce it from sticking to HDD tooling.
Other HDD drilling fluid additives to consider
High molecular weight (HMW) polymer should be used in cobble, sand and gravel ground conditions. It increases the drilling fluid’s gel strength so heavier cuttings can be flushed from the bore path.
