
Bend allowance is a term which describes how much material is needed between two panels to accommodate a given bend. Bend allowance, while being oftentimes tricky to determine for all cases, is fairly easy to predict and calculate for many standard circumstances. Determining bend allowance is commonly referred to as “Bend
What is a bend allowance in sheet metal?
When the sheet metal is put through the process of bending the metal around the bend is deformed and stretched. As this happens you gain a small amount of total length in your part. The Bend Allowance is defined as the material you will have to add to the initial length of your flat sheet in order to arrive at the length of formed part.
What is the difference between K-factor and bend allowance?
In practice, K-Factor is used when you don’t know the process or machine that is going to be used to bend the sheet. The Bend Allowance (BA) is the arc length of the bend as measured along the neutral axis of the material.
How do you calculate the setback and bend allowance?
The values of the setback, bend allowance, and bend deduction can be calculated from the sheet thickness, bend radius, bend angle, and K-factor. Learn more about Bending.
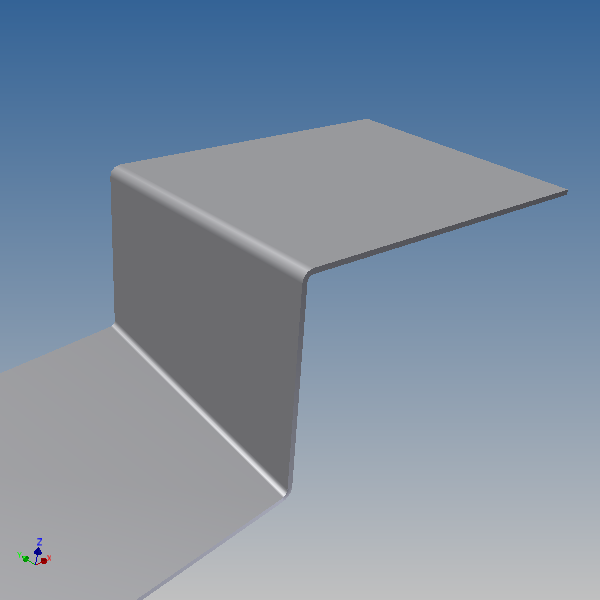
What is a bending allowance?
Bend allowance is defined as the material required to add to the overall length of the sheet metal in order for it to get cut in the right size. Density in metals can be measured in GPa, or gigapascal. The more gigapascal in a material, the stiffer it is.
How do I get bend allowance?
To calculate bend allowance: Obtain the properties of the bend (bend radius, angle, and method used). Obtain the characteristics of your material (thickness and K-factor for this specific bend). Input everything into the bend allowance formula: BA = angle × (π/180) × (radius + K-factor × thickness) .
Why is bend allowance important?
Bend allowance (also known as bend deduction) can be used to predict this initial flat length (see Figure 2). Bend allowance depends on how the final sheet dimensions are measured and on several important variables, such as the material properties, sheet thickness, and bend radius.
What is meant by bending allowance in sheet metal fabrication?
The bend allowance (BA) is the length of the arc of the neutral line between the tangent points of a bend in any material. Adding the length of each flange as dimensioned by B in the diagram to the BA gives the Flat Pattern length.
What is bend allowance and bend deduction?
Bend Allowance and Bend Deduction Value By definition, the bend allowance is the arc length of the bend as measured along the neutral axis of the material. By definition, the bend deduction is the difference between the bend allowance and twice the outside setback.
Why bend deduction is calculated?
Considering the Bend Deduction and Bend Allowances is a critical first step in designing sheet metal parts as it affects nearly every following step in the fabrication process. More so, it will allow you to achieve the correct size and dimensions needed in the flat pattern.
What is an example of bending?
For example, a closet rod sagging under the weight of clothes on clothes hangers is an example of a beam experiencing bending.
Is bend allowance the same as K factor?
The K factor is defined as the ratio between the material thickness (T) and the neutral fibre axis (t), i.e. the part of the material that bends without being compressed nor elongated. Bend allowance is a fundamental parameter to calculate sheet elongation.
How do you use bend allowance chart?
0:422:40How to find the sheet metal bend allowance and Setback ... - YouTubeYouTubeStart of suggested clipEnd of suggested clipOn an acute angle bend b a equals a x pi 180 r plus k x t the bend angle a in degrees. Inside bendMoreOn an acute angle bend b a equals a x pi 180 r plus k x t the bend angle a in degrees. Inside bend radius r in m k factor k for different types of materials.
What is K factor in sheet metal?
In sheet metal, the K-factor is the ratio of the neutral axis to the material thickness. When a piece of metal is being formed, the inner portion of the bend compresses while the outer portion expands (see Figure 1).
What is Y factor in sheet metal?
What is Y factor? The Y-factor represents the part constant used in the formula to calculate the unfolded length of a sheet metal part bending with a specific radius and angle in the design. The Y-factor is defined by the position of the neutral bending line (in relation to the thickness) of the sheet metal part.
How do you calculate a 90 degree bend?
To use the deduct figure, measure the distance to the far edge of the 90 and subtract the deduct figure. If ½" pipe is being bent and the distance is 56", place a mark on the conduit at 51"; this is where the bender will be placed. Work the bender onto the conduit with the conduit mark at the arrow of the bender.
How are bend deductions calculated?
Here's the formula: Bend deduction = (2 × Outside setback) - Bend allowance. With the bend deduction in hand, you can determine the appropriate flat blank size, and program the press brake so that the backgauge fingers accommodate for material elongation during each bend.
Do you add or subtract bend allowance?
Bend Allowance = Angle * (π / 180) * (Radius + K-factor * Thickness). So the flat pattern length is 1.625” + 2.625” + 0.475" which is equal to 4.725". So if you add up the flat length of all the flanges and add one Bend Allowance for each bend area you have the correct flat length of the part.
How do you use bend allowance chart?
0:422:40How to find the sheet metal bend allowance and Setback ... - YouTubeYouTubeStart of suggested clipEnd of suggested clipOn an acute angle bend b a equals a x pi 180 r plus k x t the bend angle a in degrees. Inside bendMoreOn an acute angle bend b a equals a x pi 180 r plus k x t the bend angle a in degrees. Inside bend radius r in m k factor k for different types of materials.
What is bend allowance What is K-factor its value?
To perform a bend allowance calculation, always use the complementary bend angle. This formula uses a K-factor of 0.446. Still, if you have any change in the method of forming, type of material, or the ratio of inside bend radius to material thickness, you will have a different K-factor value.
What is bend allowance?
The Bend Allowance is defined as the material you will add to the actual leg lengths of the part in order to develop a flat pattern. The leg lengths are the part of the flange which is outside of the bend radius.
What happens when you bend metal?
When the sheet metal is put through the process of bending the metal around the bend is deformed and stretched. As this happens you gain a small amount of total length in your part. Likewise when you are trying to develop a flat pattern you will have to make a deduction from your desired part size to get the correct flat size.
Is sheet metal bending the same?
Unfortunately sheet metal bending is not always going to be the same in every shop. The largest variations come from the materials themselves. Protective coatings, variations in the alloy and thickness as well as many other small factors all add up to give you Bend Allowances unique to your operation. This chart will get you close enough for most applications and may not require fine tuning on your part, however if you are truly dedicated to precise bending, download the excel sheet and begin plugging in your own values.
How to find bend allowance?
In this formula here the bend allowance equals 2 times pi, multiplied by A that’s the angle, multiplied by the sum of R the bend radius, plus the k-factor, multiply by T the thickness of the material, and then you divide all of this by 360.
Which approach is the most accurate for calculating bend allowance?
The bend table approach is probably the most accurate approach for calculating bend allowance.
What happens to the neutral axis during bending?
The neutral axis is in my diagram here and red. They don’t change during the bending process. During the bending process, the material inside the neutral axis will compress, and material outside the neutral axis will stretch. The neutral axis would be closer to the inside bend.
Which axis is closer to the inside bend?
The neutral axis would be closer to the inside bend. The inside bend is indicated in blue in the diagram. The more the part bends, the closer the neutral axis will lie to the inside of the part. Bend allowance calculation formula with K-factor:
What is the K factor of a soft bend?
On the other hand, a soft bend or for example the gradual bend that I’ve got on the other side of this part is got a higher k-factor of about 0.5, and this concludes our lesson on bend allowance.
What happens if you compare the length of a part before and after bending?
If you compare the length of this part, before and after the bending, you’re going to find that they’re different.
When a sheet is bent in the press brake, what happens?
Well, when a sheet is bent in the press brake, the part of the sheet close to and in contact with the punch elongate to compensate for the given bend. If you compare the length of this part, before and after the bending, you’re going to find that they’re different. As engineers, if you don’t compensate for this variation, ...
What Is Bend Allowance?
Bend allowance is defined as the material required to add to the overall length of the sheet metal in order for it to get cut in the right size.
Why is bend allowance important?
Bend allowance is important to understand when you are modifying multiple kinds of sheet metal. To minimize errors in production, take bend allowance into account and utilize bend deduction whenever necessary.
What Metals Do Not Bend Well, Or Break When Bending Too Far?
If a material doesn't bend, it will certainly break right at the point that it is being bent. Among all the alloys, tungsten is the stiffest metal, at a whopping 411 GPa. Even in the thinnest of forms, tungsten is very hard to bend and thus will likely break just like glass. The second most stiff metal is beryllium copper at 304 GPa. Chromium, a material found in diamonds and other gems, is the third most with 279 GPa. Both wrought iron and cobalt have 211 GPa. At 210 GPa, you have many more common metals for sheet metal, such as steel, stainless steel, cobalt, and nickel. As you can tell, most metals are considered very stiff, but as explained before, some metals are less stiff than others.
What Is Bend Deduction?
Bend deduction, however is the material required for users to remove from the total length in order to achieve flat metal again. Manufacturers tend to rely on bend deduction in order to negate bend allowance if they need metal to have reduced or no deformations.
What does BA stand for in metal?
BA stands for bend allowance. A stands for angle , representing the degree to which the angle is bent. R stands for the bend radius in the metal. K is the K-factor or constant, which is the ratio between the point of the metal's neutral axis to the metal's thickness. The K-factor will typically end up being in between 0 to 0.5. T stands for the material's thickness.
Can metal bend?
Metal can in fact bend. When sheet metal is being fabricated, metal has to bend in order to not just be molded into a certain shape, but also pass safety regulation in times which impact is dealt to the metal, causing it to bend instead of break. Regardless of the type of metal as well as what shape and thickness the metal has, ...
What is bend allowance?
The Bend Allowance is defined as the material you will add to the actual leg lengths of the part in order to develop a flat pattern. The leg lengths are the part of the flange which is outside of the bend radius. Unfortunately sheet metal bending is not always going to be the same in every shop.
When a bend is smaller than the radius required, what happens?
When bends are made smaller than the required min. radius, metal will crack at the outside heel of the bend. The min. radius of a bend is determined by the hardness and thickness of the metal. There are four methods for finding bend allowances. In the form below uses the empirical formula.
What happens when you bend metal?
When the sheet metal is put through the process of bending the metal around the bend is deformed and stretched. As this happens you gain a small amount of total length in your part. Likewise when you are trying to develop a flat pattern you will have to make a deduction from your desired part size to get the correct flat size. ...
What is the bend allowance?
The Bend Allowance (BA) is the arc length of the bend as measured along the neutral axis of the material. Understanding the Bend Allowance and consequently the Bend Deduction of a part is a crucial first step to understanding how sheet metal parts are fabricated.
What is bend deduction?
The Bend Deduction is defined as the material you will have to remove from the total length of your flanges in order to arrive at the flat pattern.
What happens when you bend metal?
When the sheet metal is put through the process of bending the metal around the bend is deformed and stretched. As this happens you gain a small amount of total length in your part. The Bend Allowance is defined as the material you will have to add to the initial length of your flat sheet in order to arrive at the length of formed part.
90 Degrees Bend Angle
Figure 2 illustrates the sheet that is bent with the bend angle of 90 degrees. We will start by calculating the Bend Allowance. From there we can calculate the K-Factor and the Bend Deduction. After bending the sheet we need to do some measurements as shown in Figure 2.
Bending Angles Less Than 90 degrees
For our second scenario we are going to discuss the calculations for bending angles less than 90 degrees. As an example we are going to use 60 degrees as our bending angle. Again we have to do some measurements as shown in Figure 3. Then we have to calculate Leg Length 1 and Leg Length 2.
Bend Deduction Calculation
As explained in my first post the Bend Deduction can be calculated using the following equation:
Saeed Mojarad (CSWE)
Saeed Mojarad is an application engineer at Javelin Technologies. He received his B.S from Mazandaran University, Iran; and his M.S. from École de technologie supérieure (ETS), Canada. He has several years of experience using SOLIDWORKS in different industries such as manufacturing and aerospace.
What is bend allowance?
The bend allowance describes the length of the neutral axis between the bend lines, or in other words, the arc length of the bend. Therefore, the bend allowance added to the flange lengths is equal to the total flat length.
What is bend deduction?
The bend deduction, sometimes called the bend compensation, describes how much the outside of the sheet has been stretched. Therefore, the bend deduction equals the difference between the mold line lengths and the total flat length. The mold line lengths are the distances measured to the outside mold line and are equal to ...
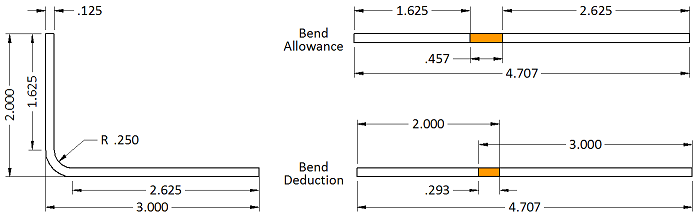