
Is precast concrete better than modular building?
Precast is perfect for buildings which are typical in layout and plan. If the loads coming onto the floor is non moving and lighter. Both are fast paced. Logistic is an issue. We also have issues fixing the Precast concrete panels. Modular is better if buildings are divided into various functional units.
How much do precast concrete panels cost?
To create precast concrete, manufacturers pour concrete into a mold and create a panel. Rather than having a truck come to your property to pour onsite, specialists lift these panels into place. A prefab concrete wall costs most homeowners between $1,650 and $8,000. Prefabricated concrete is another word for precast concrete.
Is precast concrete used for flooring or not?
Precast hollowcore concrete is widely used in various residential, commercial and municipal applications that require a floor or roof system comprised of standard components, manufactured in a controlled environment. Due to the significant benefits of superior fire
How to repair precast concrete?
Steps
- Clean the damaged portion of the concrete step. Remove all loose gravel, sand, dirt, and cement with a clean, stiff wire brush.
- Make a form. Screw 2 short pieces of 1 inch by 6 inch (2.54 cm by 15.24 cm) lumber together at a 90-degree angle to form an "L" shape.
- Align the wood form. ...
- Lubricate the form. ...
- Apply bonding liquid. ...
- Prepare quick-setting cement. ...
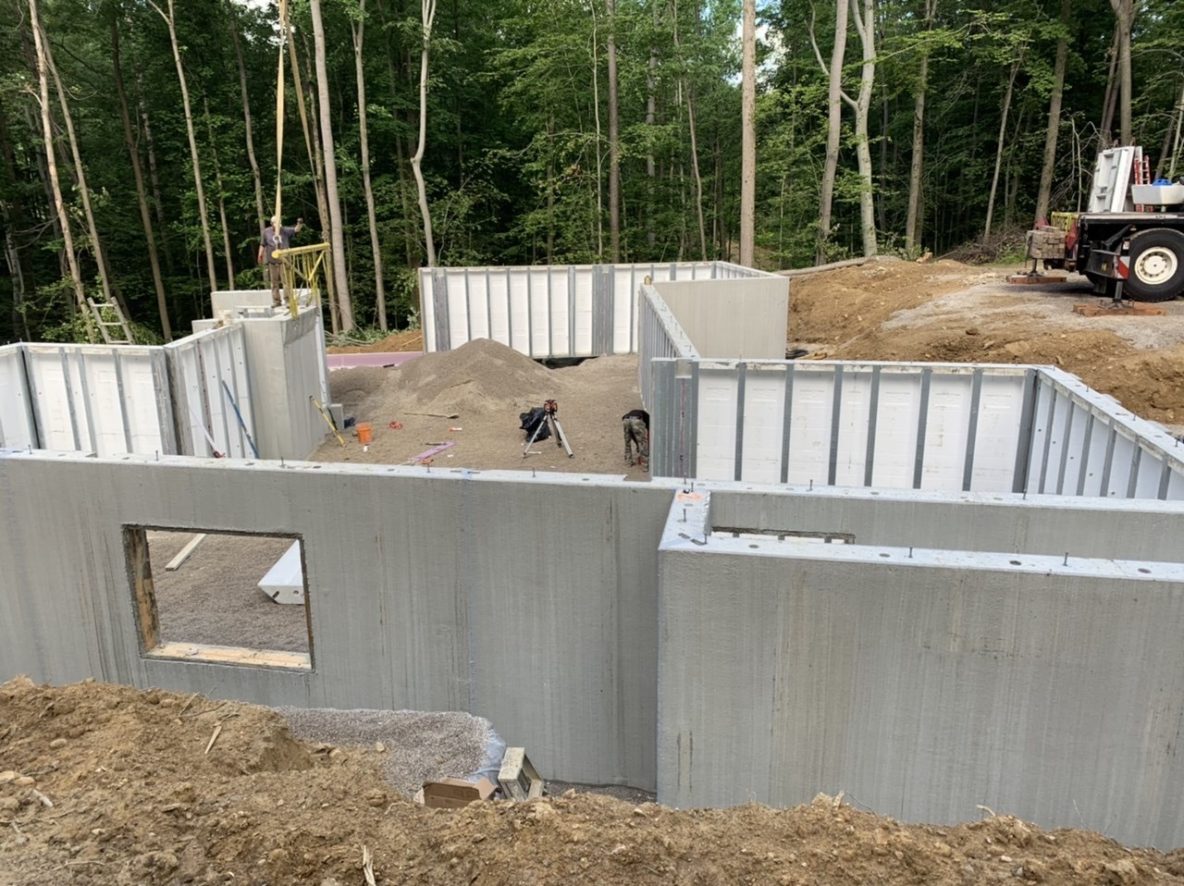
What are the advantages of using precast concrete walls?
Precast concrete wall panels provide numerous long term cost advantages with exceptional durability, lower energy costs and lower maintenance costs when compared with insulated metal panel systems. and ability to be produced and erected year-round shortens project schedules.
What is precast concrete in simple words?
Precast concrete is a construction product produced by casting concrete in a reusable mold or "form" which is then cured in a controlled environment, transported to the construction site and maneuvered into place; examples include precast beams, and wall panels for tilt up construction.
How do precast panels work?
0:373:07Pre-Cast Concrete Walls | How It's Made - YouTubeYouTubeStart of suggested clipEnd of suggested clipThey place one cage at the top of the form and one at the bottom. Then a team inserts a sheet ofMoreThey place one cage at the top of the form and one at the bottom. Then a team inserts a sheet of welded wire mesh. It's been cut to fit the size of the form. They're now ready to pour concrete.
Why is precast concrete used?
Precast concrete allows efficient, economical construction in all weather conditions and provides the long clear spans and open spaces needed in parking structures.
Which are examples of precast concrete?
What is precast concrete?Light pole and sign bases.Pillars and columns.Parking structures.Culverts.Retaining walls.Building construction.
What type of concrete is used for precast?
Ordinary Portland CementsCement for Precast Concrete Buildings General-purpose- Ordinary Portland Cements [OPC] 43 grade [IS:8112] and 53 [IS:12269] are normally used in precast concrete construction. Avoid high silica cement as it suffers reversion and loses a large portion of its strength in warm and humid conditions.
Is precast wall strong?
Structural precast concrete panels are comprised of high-strength concrete and prestressed steel strand. It's relatively routine for precast concrete wall panels have a compressive strength of approximately 7,000 PSI.
How thick is precast concrete wall?
4 to 12 in.Typical thicknesses: 4 to 12 in. Finishes: Since wall panels are cast in a flat orientation, the form side is typically the side that will be exposed to view in the final construction.
How long does precast wall last?
Precast concrete structures have a lot to live up to; they must endure all manner of environmental conditions. Ideally, such products should last 50 to 100 years or more. Curing the concrete in a controlled environment is key to its longevity.
Is precast concrete strong?
Durability: Precast Concrete structure has a longer service time period and minimal maintenance. The high-density Precast Concrete is more durable to acid attack, corrosion, impact, reduces surface voids and resists the accumulation of dust.
Does precast concrete crack?
These cracks occur when the surface dries quickly due to heat or wind and no controls are used to cure the surface at a slower rate maintaining moisture while the cement hydrates. These types of cracks may also present themselves if there is a high water to cement ratio in concrete mix design.
What are the disadvantages of precast concrete?
Disadvantages of Precast Concrete If not properly handled, the precast units may be damaged during transport. It becomes difficult to produce satisfactory connections between the precast members. It is necessary to arrange for special equipment for lifting and moving of the precast units.
What is the definition precast?
Definition of precast : being concrete that is cast in the form of a structural element (such as a panel or beam) before being placed in final position.
What is concrete in simple words?
concrete • \kahn-KREET\ • adjective. 1 : naming a real thing or class of things 2 : formed by coalition of particles into one solid mass 3 : relating to or involving specific people, things, or actions rather than general ideas or qualities 4 : relating to or made of concrete.
How is precast concrete constructed?
Precast concrete is a form of concrete that is prepared, cast and cured off-site, usually in a controlled factory environment, using reusable moulds. Precast concrete elements can be joined to other elements to form a complete structure.
What is the exterior surface of precast concrete?
The exterior surface of precast concrete can vary from an exposed aggregate finish that is highly ornamental to a form face finish that is similar to cast-in-place. Some precast panels act as column covers while others extend over several floors in height and incorporate window openings.
How are precast panels supported?
Typically, each precast panel is independently supported to the building structure using an assemblage of metal components and anchors. Joints around each of the precast panels are usually filled with sealant.
What is the ACI code for precast concrete?
The concrete panels are designed in accordance with PCI Design Handbook-Precast and Prestressed Concrete (MNL-120), Design Responsibility for Architectural Precast Concrete Projects (ACI 533.1R-02), and ACI 318 Structural Concrete Building Code. Steel elements of a wall system are designed in accordance with AISC specifications for steel construction. Precast concrete elements are designed in accordance with ACI and PCI specifications.
What are the different types of precast panels?
There are generally four types of precast panels used as part of building envelopes: Cladding or curtain walls. Load-bearing wall units. Shear walls. Formwork for cast-in-place concrete. Precast cladding or curtain walls are the most common use of precast concrete for building envelopes.
Why are joints important in a precast concrete envelope?
The joints between precast units or between precast and other building components must be maintained to prevent leakage through the precast wall system.
What is precast shear wall?
Precast concrete shear wall panels are used to provide lateral load resisting system when combined with diaphragm action of the floor construction. The effectiveness of precast shear walls is largely dependent upon the panel-to-panel connections.
Why is my precast concrete wall cracking?
Most distress and deterioration encountered with precast concrete wall systems can be attributed to problems during erection, an chors used to attach panels to the structure, or corrosion of the embedded reinforcing steel. Panel cracking, displacements, or other distress conditions can occur at locations where anchors are inadequately or improperly connected. Poor construction is often the result of poor quality control and out of tolerance fabrication or erection of the panels. Also, damage from handling during construction can result in panel cracking, some of which may not become evident for several years.
How many layers of concrete are there in a panel?
A typical panel has two outer concrete layers, or “wythes”, separated by rigid insulation (Figure 2), and is cast in a long-line form in a plant (Figure 3). One or both wythes are usually prestressed to reduce cracking and improve performance (Figure 4).
What is a composite panel?
Fully-composite: In fully-composite panels, the wythes act together as a unit for full horizontal shear transfer. A typical composite panel is eight times stiffer , can take three times the stress without cracking and has twice the ultimate strength of a non-composite panel of similar thickness. Composite panels are typically less expensive than non-composite panels, primarily because they can carry more load and can be made taller and thinner. The inside and outside wythes are usually stressed with prestressing strand and made of equal thickness in order to minimize internal strains. (Figure 8) Sometimes, the panel is made solid below the floor line and above the parapet (outside the building envelope) to help with composite action.
Why are composite panels less expensive than non-composite panels?
Composite panels are typically less expensive than non-composite panels, primarily because they can carry more load and can be made taller and thinner. The inside and outside wythes are usually stressed with prestressing strand and made of equal thickness in order to minimize internal strains.
What is wet cast hollow core?
Wet-cast hollow-core uses inflatable diaphragms, insulation, or gravel to create the voids. Dry-cast hollow-core uses a zero-slump concrete mix and the “plank” is extruded from a machine-like pasta. Window and door openings are typically saw-cut in the field.
Can precast concrete be erected all at once?
Anticipate the erection sequence. It is preferable for the precast concrete products to be erected all at one time. If the precast erector has to come back later to place additional panels supported by steel framing, then it may be desirable to convert this steel framing to precast.
Can a panel carry roof load?
Panels can carry roof and floor loads or just act as cladding (load-bearing vs. non-loadbearing, (Figure 6A, B and C).
Is precast concrete a good alternative to masonry?
This in turn can reduce the size of HVAC units needed. Competitive cost: Precast concrete wall panels can be a cost-effective alternative to masonry or other hard wall systems and does not require as much labor as other systems.
What are the types of buildings that use precast concrete?
Here are some common types of buildings regularly using precast concrete: Schools: Schools can be built in a timely and efficient manner, keeping the project schedule on track. Permacast Walls provide sound-proof security walls along the perimeters of schools, creating a safer environment for students and staff.
What is the difference between precast and site cast concrete?
The main difference between precast concrete and site-cast concrete is that pre cast concrete is poured off-site, usually at a plant, using a mold. Site cast concrete, in comparison, is poured on the construction site itself, subjecting it to environmental factors, weather, unstable schedules, and much wasted excess material. When concrete is precast in a plant, on the other hand, the entire process in controlled before bringing the cured concrete to the construction site. Weather is no longer a factor, nor are other environmental factors that can be huge obstacles with on-site concrete pours. In precast concrete, the mold often includes a pre-stressed cable. While this is not always necessary or included, the process of curing the concrete releases a tension that transfers strength to the concrete itself, making it even more durable.
Why is precast concrete cured?
Control: Since precast concrete is cast and cured in a controlled environment like a plant, the chances of error are greatly reduced. Environmental factors like weather are no longer pertinent to the production of pieces. The most ideal conditions are used each time, building confidence that each piece will be poured and cured precisely as required. This minimizes wasted excess materials, since the process is so predictable, and allows for construction timelines and schedules to be met more readily each time.
What are the natural materials used in precast concrete?
With precast concrete, natural materials like sand, gravel, rock, and water are used as aggregates, and the water used is often recycled. These natural materials are typically harvested locally, cutting down on hauling trips that are expensive and environmentally unfriendly.
How does casting concrete affect the environment?
Casting concrete in a plant greatly reduces the amount of waste from packaging, excessive concrete, bracing and form work, and other debris that builds up on a construction site. Also, less raw material is used leaving the environment in and around the construction site untouched and less polluted.
Is precast concrete good for parking?
Parking Garages: Many parking garage structures are created with precast concrete, and it’s easy to see why. From columns and paving slabs to stairs and traffic barriers, bringing each piece pre-designed from the factory aides in the economic construction of a durable, efficient parking structure. Whether single structure or multi-level, the sleek, modern look of precast concrete can enhance any urban area design or blend into the existing local decor. Plus, in growing metropolitan areas, completing a reliable, useful structure in a fraction of the time is a huge bonus.
Can you use precast concrete for a foundation?
Foundations: Even if your entire building won’t be created using precast concrete, laying a precast concrete foundation can be a huge advantage in the construction of new buildings. A precast basement will fit perfectly the first time, without rain delays or other environmental factors to sidestep.
What is Fabcon precast?
Fabcon’s precast panels can support roof structures for dead and live loads and act as the building’s lateral stabilizing piece to withstand seismic shaking. The wall panels also support the building structure for mezzanines and multiple floors.
What is Fabcon sandwich panel?
Fabcon’s panels are also capable of meeting all R-Value requirements—regardless of the climate zone. The sandwich panel is the company’s highest R-Value product; in addition to the core and web insulation pieces, it also features a continuous insulation piece across the width and length of the panel (or bedfoam).
How many panels can Fabcon install in a day?
If things go smoothly out in the field, Fabcon can install 20 to 30 eight-foot panels in a day.
Is concrete a fire barrier?
Concrete itself is an effective barrier for fire. Fabcon’s precast concrete wall panels are capable of providing a two- to four-hour fire rating. And their precast walls stay intact even in hot chemical fires. Warehouses often use Fabcon’s wall panels as dividers to protect goods on the other side of fire-prone areas. “The more delay you can create from one side to the other, the better chance of getting people out safely without having any incident and also the higher probability of protecting goods and services,” Miks says.

Introduction
Description
- Precast Panel Types for Building Envelopes
There are generally four types of precast panels used as part of building envelopes: 1. Cladding or curtain walls 2. Load-bearing wall units 3. Shear walls 4. Formwork for cast-in-place concrete Precast cladding or curtain walls are the most common use of precast concrete for building env… - Support and Anchorage Systems
The connections for precast concrete panels are an important component of the envelope system. Precast manufacturers utilize numerous different types of anchors but they are often characterized as gravity and lateral types of connections. The primary purposes of the connecti…
Fundamentals
- Structural Aspects of Design
Precast concrete wall systems are most often constructed as a curtain wall or veneer, in which no building loads are transferred to the concrete panels. Most typically the precast concrete wall system must resist lateral loads directly imparted on it, such as from wind and earthquake; as w…
Applications
- Precast concrete wall systems allow a wide variety of colors, finishes and architectural shapes. Precast concrete can be used in environments that allow the use of conventional cast-in-place concrete. In addition, precast concrete may be made in a controlled environment and erected in an environment that would not allow site casting of concrete. The concrete used in precast pane…
Details
- The following details can be downloaded in DWG format or viewed online in DWF™ (Design Web Format™) or Adobe Acrobat PDF by clicking on the appropriate format to the right of the drawing title. Architectural Precast Window Jamb and Sill DWG | DWF | PDF Architectural Precast Round Penetration DWG | DWF | PDF Architectural Precast Square Penetration DWG | DWF | PDF Archit…
Emerging Issues
- The necessity to make building envelopes blast-resistantforces reconsideration of precast concrete joint and connection designs.
Relevant Codes and Standards
- American Concrete Institute ACI 318—Building Code Requirements for Structural Concrete
- American Concrete Institute ACI 301—Specifications for Structural Concrete
- Precast/Prestressed Concrete Institute PCI Design Handbook-Precast and Prestressed Concrete(MNL 120)
Additional Resources
- American Concrete Institute
1. ACI 318—Building Code Requirements for Structural Concrete 2. ACI 301—Specifications for Structural Concrete 3. ACI 201.2—Guide to Durable Concrete 4. ACI 533.1R—Design Responsibility for Architectural Precast Concrete Projects - ASTM International
1. ASTM C 33—Aggregates in Concrete 2. ASTM C 457—Air Void 3. AGGREGATE REACTIVITY 4. ASTM C 856—Petrographic Analysis of Hardened Concrete